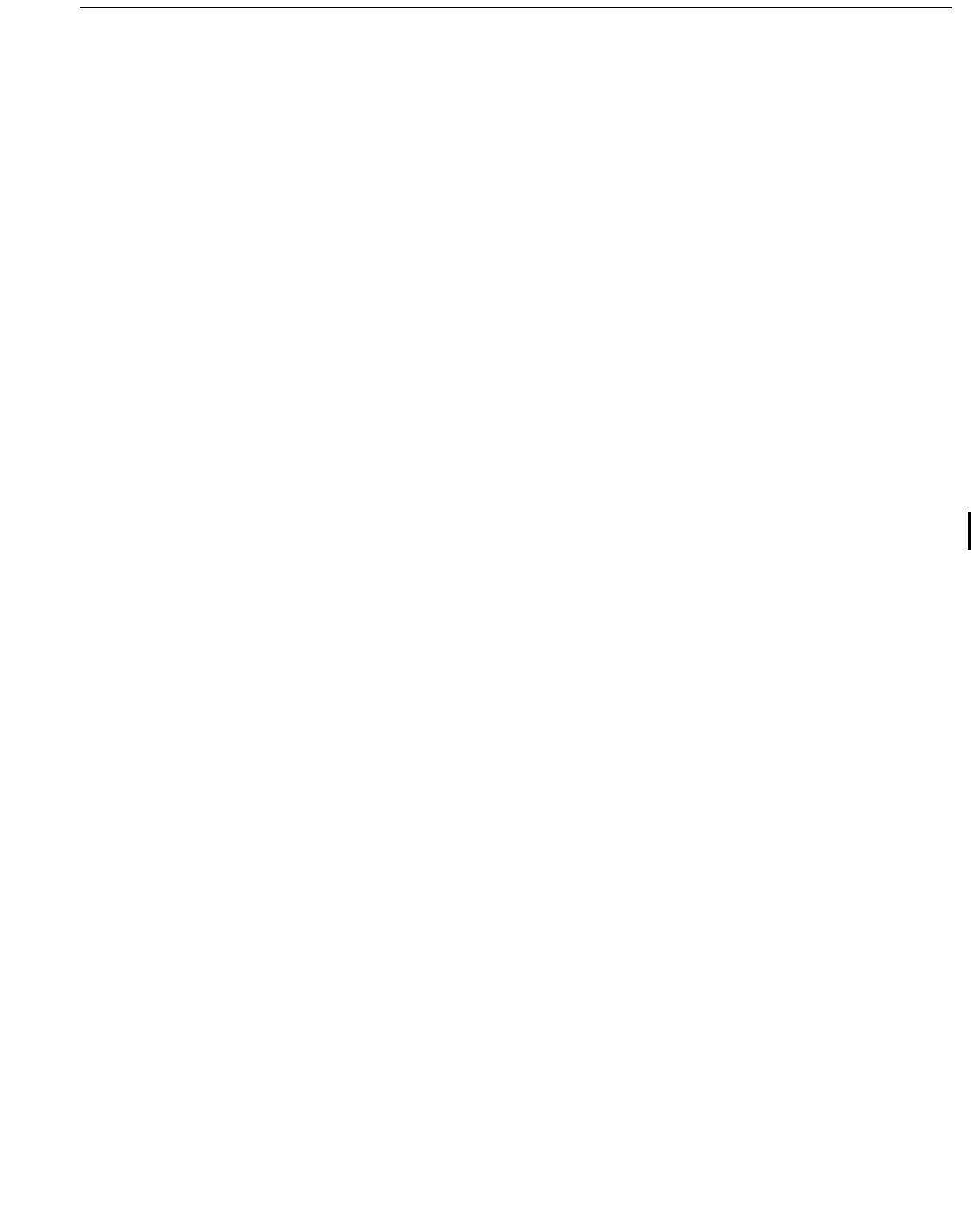
RECOMMENDED PRACTICE FOR PLANNING, DESIGNING AND CONSTRUCTING FIXED OFFSHORE PLATFORMS—WORKING STRESS DESIGN 93
11.3.3 Material Identification
Material receiving and handling is normally a fabrication
contractor’s function. Upon receipt of material and prior to
fabrication, a material identification system should be estab-
lished by the fabricator which will trace each primary struc-
tural member within the completed structure back to the
original mill certificates. The identification system should
eliminate any conflict or duplication of any primary structural
element. The system should identify materials from manufac-
turing through transport, receipt, storage, fabrication and final
erection. The system should be such that all NDT can also be
identified.
11.4 LOADOUT
Loadout and tie-down is normally performed by the fabri-
cation contractor. Loadout and tie-down should be performed
in accordance with the loadout plan, Section 12, and owner
requirements.
11.5 RECORDS AND DOCUMENTATION
The fabrication contractor should maintain the mill certifi-
cates as discussed in 11.3.2 which are necessary to demon-
strate that proper materials were used in the structure. In
addition, the fabricator should also compile and maintain the
material identification records as discussed in 11.3.3 neces-
sary to trace and identify the origin of each primary member.
At the completion of the job the fabricator will compile and
deliver to the owner these documents for permanent record.
During the course of fabrication, revisions may be
approved to the primary structural members such as wall
thickness, member size, type material, etc. For any substitu-
tions and revisions made during fabrication, suitable records
should be documented by the fabricator and listed as correc-
tions to the fabrication drawings. The responsibility for the
compilation of these records with other documentation
related to the construction and inspection of the structure and
the retention of these permanent records should be as speci-
fied by the owner.
12 Installation
12.1 GENERAL
12.1.1 Planning
The installation of a platform consists of loading out and
transporting the various components of the platform to the
installation site, positioning the platform on the site and
assembling the various components into a stable structure in
accordance with the design drawings and specifications.
The installation of a platform should be accomplished in
such a manner that the platform can fulfill the intended
design purpose.
An installation plan should be prepared for each installa-
tion. This plan should include the method and procedures
developed for the loadout, seafastenings and transportation of
all components and for the complete installation of the jacket,
pile/conductors, superstructure and equipment. This may be
in the form of a written description, specifications and/or
drawings. Depending upon the complexity of the installation,
more detailed instructions may be required for special items
such as grouting, diving, welding, inspection, etc. Any
restrictions or limitations to operations due to items such as
environmental conditions, barge stability or structural
strength (i.e., lifting capacity), should be stated.
The installation plan is normally to be subdivided into
phases, for example: Loadout, Seafastenings, Transportation,
and Installation. The party responsible for the execution of
each phase of the work should prepare the installation plan
for that phase, unless otherwise designated by the Owner.
Coordination and approval procedures between all parties
should be established by the Owner.
12.1.2 Records and Documentation
During the loadout, transportation and installation, all daily
reports logs, NDE reports, pile driving records, survey indicat-
ing platform orientation and verticality, etc., are to be prepared,
compiled and retained by the party responsible for that phase
of the work. These documents should also record any variation
from intended installation procedures, all unusual environmen-
tal conditions which occurred during the installation. All “field
modifications” which were made should be noted to record as-
built condition of the structure. At the completion of the job
each party will compile and deliver to the owner these docu-
ments in a form suitable for use as a permanent record. The
responsibility for the compilation of these records with other
documents related to the construction and inspection of the
structure and for the retention of these permanent records will
be in accordance with the requirements of the Owner.
12.1.3 Installation Forces and Allowable Stresses
The forces applicable to each phase of the installation
should be calculated as described in Section 2.4. Analysis
should be performed to ensure that the structural design is
sufficient to withstand the type and magnitude of those forces
or force combinations. The calculated stress in structural
members should be in accordance with Section 3 as further
qualified in Section 2.4.
12.1.4 Temporary Bracing and Rigging
Procedures covering the calculation of forces, load factors,
allowable stresses and factors of safety for component parts
of the structure as well as slings, shackles and fittings are
listed in 2.4.2. Should any installation aids, temporary struts,
bracing or rigging be required during any phase of the instal-
Copyright American Petroleum Institute
Provided by IHS under license with API
Licensee=Indonesia location/5940240008
Not for Resale, 10/22/2008 00:07:12 MDT
--`,,```,,,`,,,,,,,,,,,,,,`,``,`-`-`,,`,,`,`,,`---