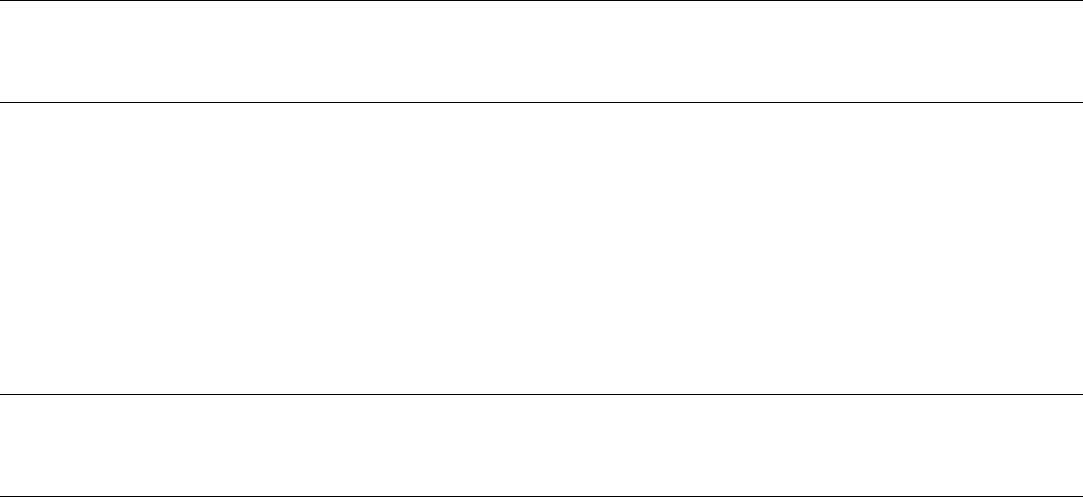
Precautions to be taken if the firing circuit has been energized and the charge does not go off include a check of the
continuity of the circuit. If the circuit is good, another attempt should be made to fire the charge. If this fails, the firing
circuit should be disconnected from the power source and the power source tested for proper output. If no failure is found
in the power source, the lead wires in the firing circuit can be inspected visually from a distance to determine if any shorts
have occurred. Under no circumstances should the charge be brought to the surface for examination until 15 min has
elapsed from the last time attempts were made to fire the charge. All personnel should leave the area during this waiting
period. After the specified time has elapsed, the charge should be brought to the surface and a new cap installed. When
defective blasting caps are found, they should be destroyed with any other scrap explosive at the close of operations for
each working day.
Explosive Forming
Revised by A.E. Doherty, Explosive Fabricators, Inc.
References
1. M.C. Noland et al., "High-Velocity Metalworking," NASA SP-
5062, National Aeronautics and Space
Administration, 1967, p 183
2. J.S. Rinehart and J. Pearson, Explosive Working of Metals, Macmillan, 1963, p 19-20, 263-266
3. A.E. Doherty, Applications of Commercial Explosives to Production of HERF Parts, in
International Conference on High-Energy Rate Fabrication, 1986, p 246-250
Electromagnetic Forming
Revised by Michael M. Plum, Maxwell Laboratories, Inc.
Introduction
ELECTROMAGNETIC FORMING (EMF) is an assembly technique that is widely used to both join and shape metals
and other materials with precision and rapidity, and without the heat effects and tool marks associated with other
techniques. Also known as magnetic pulse forming, the EMF process uses the direct application of a pressure created in
an intense, transient magnetic field. Without mechanical contact, a metal workpiece is formed by the passage of a pulse of
electric current through a forming coil.
The parameters that determine the applicability of the EMF process are:
•
Forming can be accomplished through a nonmetallic coating or container because the magnetic field passes
through electrical nonconductors
• Most of the forming takes place after the pressure impulse has ended, in contrast to most metal-
processes. The metal is rapidly accelerated, gaining a large amount of kinetic energy by moving only a short
distance during the impulse. This kinetic energy subsequently does the actual work of forming
• The metals that
are most efficiently formed by EMF are those with relatively high electrical conductivity, such as
copper, aluminum, low-
carbon steel, brass, and molybdenum. Metals with lower conductivity, such as stainless
steel, can be formed by using either very high energy or an intermediate, highly conductive "driver"
•
The ratio of the masses of pieces used in assembly operations may be much more significant than their relative
mechanical strength or elastic properties. Because EMF does not use static forces, relative
be used to support the dies
•
No torque is applied to the workpiece in swaging and expanding operations, in contrast to spinning and rolling.
Because the magnetic field behaves much like a compressed gas, it exerts a uniform pressure
independent of variations in spacing between the workpiece and the forming coil
• No lubricant is required because the contact between the magnetic field and the workpiece is frictionless
• The peak pressure is limited (by the strength of the forming-
coil material) to much lower values than are