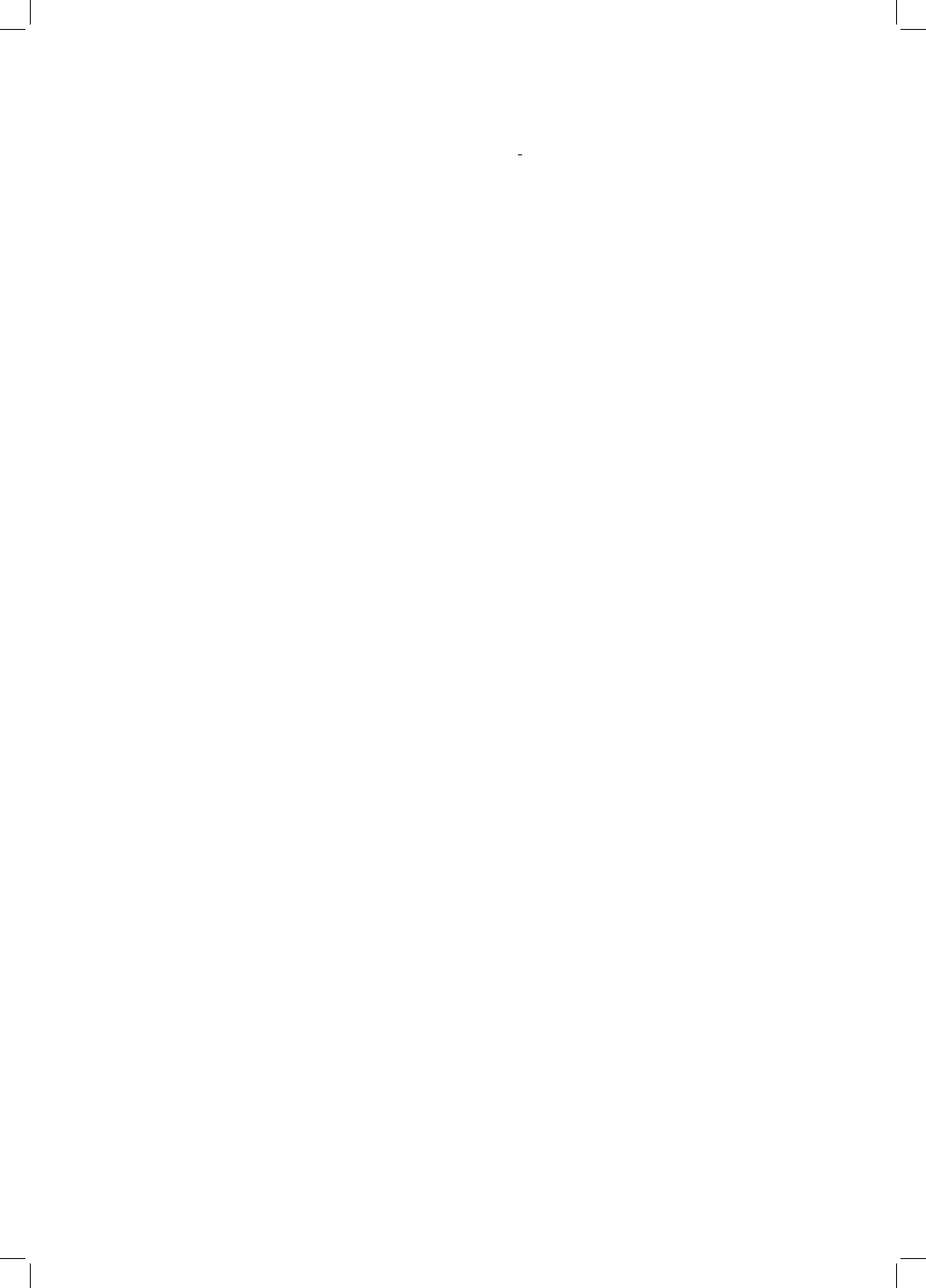
K
IC
C
2r
c
1
2
12:6
where
C
is usually identi®ed with
F
(eq. 12.2), the local stress required to
propagate a microcrack nucleus.
F
varies with carbide thickness, or more
generally, with the size of the microcrack nuclei resulting from the fracture
of a brittle phase in the steel; it is relatively independent of temperature.
The interpretation of the distance r
C
is less straightforward. The sample used
in a fracture toughness test contains a machined notch, but to make the speci-
men representative of failure during service, it is fatigue loaded to form a sharp
crack which grows slowly from the root of the notch. Fatigue loading is
stopped as soon as a uniform crack front is established. The specimen is
then ready for toughness testing. The fatigue crack tip is sharp, but not as
sharp as the tip of a cleavage crack. It does not therefore propagate when
the specimen is tensile loaded for the K
IC
test. Instead, the stress ®eld extending
from the fatigue crack tip causes brittle particles within a distance r
C
of the tip
to fracture. The resulting microcrack nuclei are atomically sharp and propagate
into the matrix if the stress
C
is exceeded. The cleavage cracks then link up
with the original fatigue crack and failure occurs rapidly across the specimen
section.
It is emphasised that both r
C
and
C
are for most materials, statistically
averaged quantities, since all microstructural features exhibit variations in
size, shape and distribution. If the carbide particle size and spatial distribution
is bimodal, due perhaps to the presence of a mixture of microstructures, then
the K
IC
values obtained are likely to show much scatter. The stress ®eld extend-
ing from the crack tip effectively samples a ®nite volume and it is the micro-
structure of that volume which determines toughness. Bowen et al. (1986)
found that K
IC
values determined for mixed microstructures of upper and
lower bainite (the former containing coarser cementite) exhibited a large
degree of scatter when compared with a microstructure of just upper bainite
or just martensite.
The microstructural interpretation of K
IC
evidently requires a knowledge of a
local tensile stress and a microstructural distance. This approach has been
successful in explaining the toughness of mild steels with a microstructure
of ferrite and grain boundary cementite (McMahon and Cohen, 1965; Smith,
1966, Knott, 1981) and to a limited extent of steel weld-deposits which have
complex microstructures containing nonmetallic inclusions which initiate fail-
ure (Tweed and Knott, 1983; McRobie and Knott, 1985). In some of these cases,
the critical microstructural features controlling cleavage fracture resistance
have been identi®ed directly, giving faith in the r
C
concept.
Dif®culties arise when attempts are made to use this approach for clean
bainitic or martensitic structures. The carbides particles are so ®ne as to
make a direct identi®cation of r
C
impossible. The fracture stress
F
can never-
Mechanical Properties
[13:38 3/9/01 C:/3B2 Templates/keith/3750 BAINITE.605/3750-012.3d] Ref: 0000 Auth: Title: Chapter 00 Page: 303 285-342
303