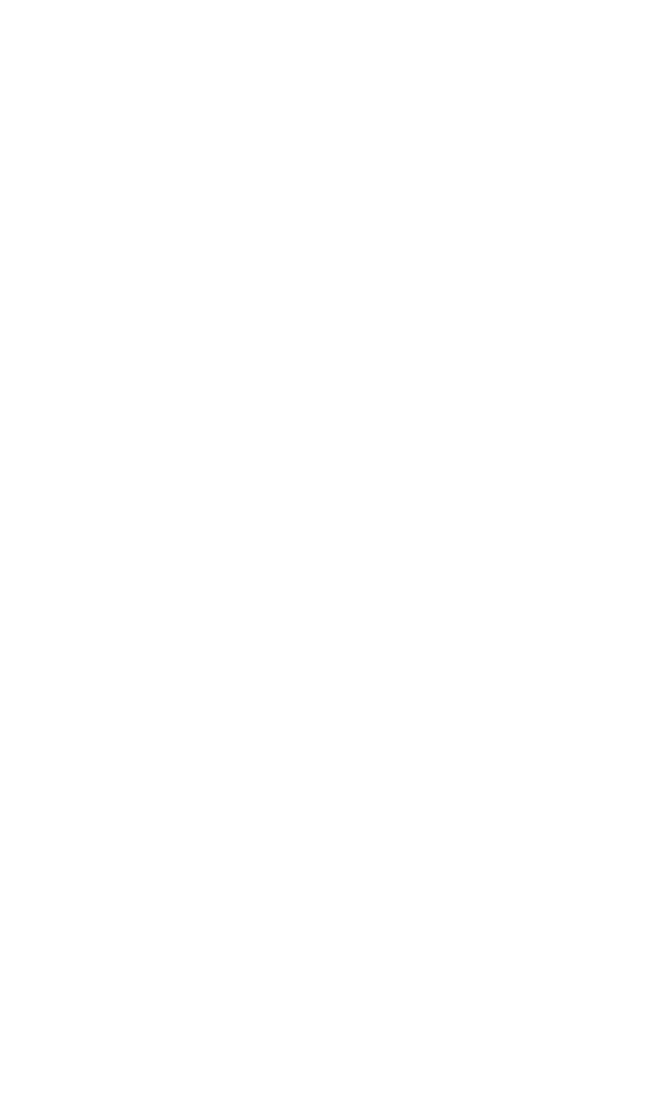
minimizes the motion of the corners of the equipment and allows the most efficient
installation from the standpoint of space requirements and isolation efficiency.
If the isolators cannot be located so as to provide a center-of-gravity installa-
tion, then the system analysis is more difficult and more space must be allowed
around the equipment to accommodate rocking motion (i.e., rotational modes) of
the system. Finally, the isolators must be double-checked to ensure that they
are capable of withstanding the additional loads and motions from the non-
translational movement of the equipment. This is particularly true when the
center-of-gravity is a significant distance above or below the plane in which the
isolators are located. Rule of thumb: The distance between the isolator plane and
the center-of-gravity should be equal to or less than one-third of the minimum
spacing between isolators. This helps to minimize rocking of the equipment and
the resultant high stress in the isolators.
Weight and Center-of-Gravity of Supported Equipment. The weight and loca-
tion of the center-of-gravity of the supported equipment should be determined. The
location of the center-of-gravity is necessary for calculating the load supported on
each mount. It is best to keep the equipment at least satatically balanced [essentially
equal deflections on all isolators (see Fig. 32.17)]. The preferred approach is to use
the same isolator at all points, choosing isolator locations such that static loads (and
thus deflections) are equalized. If this is not practical, isolators of different load rat-
ings may be required at different support points on the equipment for optimum iso-
lation.The size of the equipment and the mass distribution are important in dynamic
analyses of the isolated system.
Space Available for Equipment Motion. The choice of an isolator may depend
on the space available (commonly called sway space) around a piece of equipment.
The spring constant of the isolator should be chosen carefully so that motion is kept
within defined space limits. The motion which must be considered is the sum of (1)
the static deflection due to the weight supported by the isolator, (2) the deflection
caused by the dynamic environment, and (3) the deflection due to any steady-state
acceleration (such as in a maneuvering aircraft).
If there is a problem of excessive motion of the supported mass on the isolator,
then a snubber (i.e., a device which limits the motion) can be used.A snubber may be
an elastomeric compression element designed into an isolator. Captive-type isola-
tors (see Fail-Safe Installation) have built-in motion-limiting stops. Also, elastomers
stressed in compression have natural snubbing due to the nonlinear load-deflection
characteristics. In some cases it may be necessary to limit motion by separately
installed snubbers such as a compression pad at the point of excessive motion as
shown in Fig. 32.18. The spring constant of such a snubber must be carefully selected
to avoid transmission of high-impact loads into the supported equipment.
Ambient Environment. The environment in which an isolator is to be used
affects its selection in two ways:
1. Some environmental conditions may degrade the physical integrity of the isola-
tor and make it nonfunctional.
2. Some environmental conditions may change the operating characteristics of an
isolator, without causing permanent damage.
This may alter the characteristics of the isolation system of the supported equip-
ment; for example, frequency responses could change significantly with changes in
SHOCK AND VIBRATION ISOLATORS AND ISOLATION SYSTEMS 32.19
8434_Harris_32_b.qxd 09/20/2001 12:32 PM Page 32.19