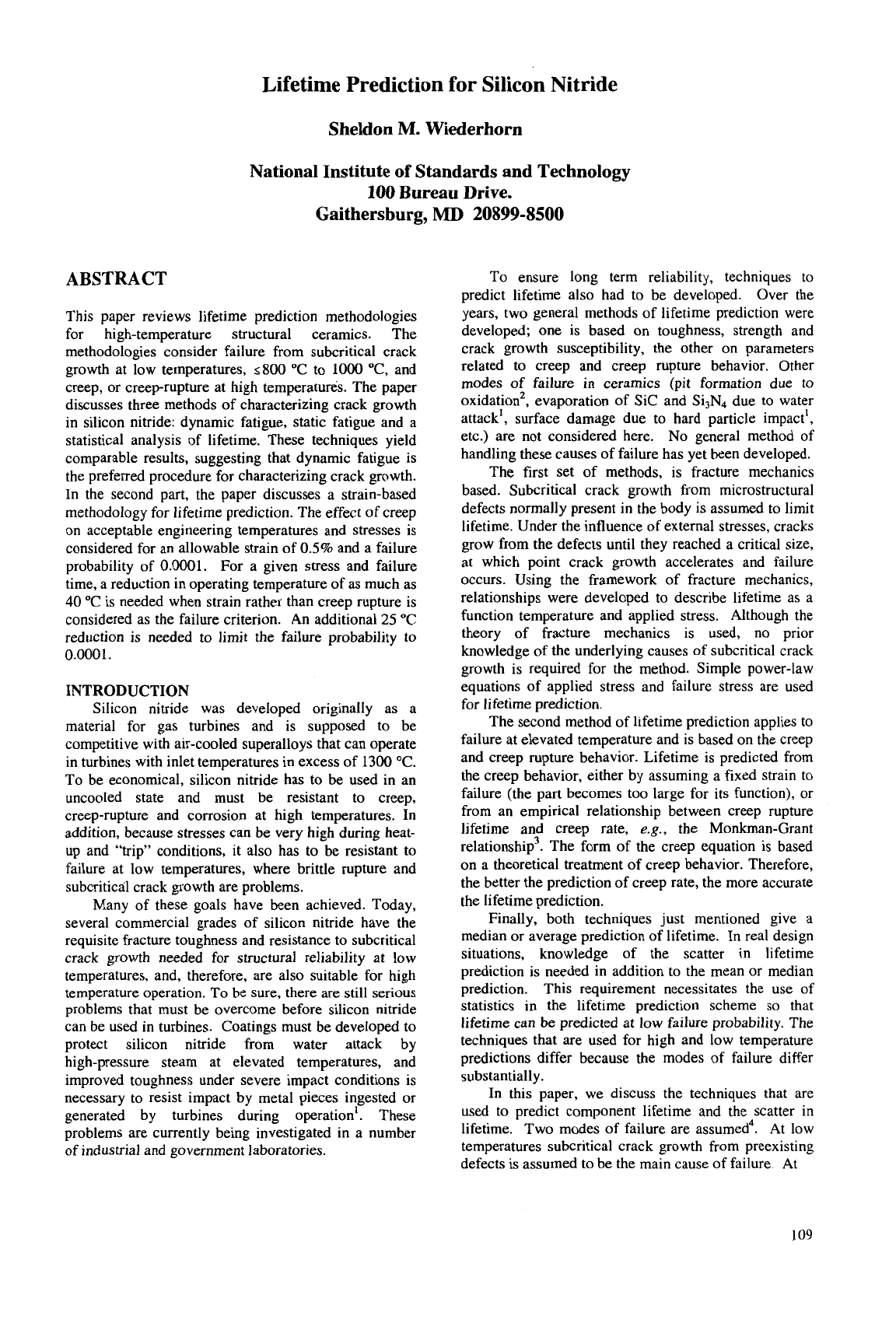
Lifetime Prediction for Silicon Nitride
Sheldon
M.
Wiederhorn
National Institute
of
Standards and Technology
100
Bureau Drive.
Gaithersburg,
MD
20899-8500
ABSTRACT
This paper reviews lifetime prediction methodologies
for high-temperature structural ceramics. The
methodologies consider failure from subcritical crack
growth at low temperatures,
~800
"C to
1000
"C, and
creep, or creep-rupture at high temperatures. The paper
discusses three methods of characterizing crack growth
in
silicon nitride: dynamic fatigue, static fatigue and a
statistical analysis of lifetime. These techniques yield
comparable results, suggesting that dynamic fatigue is
the preferred procedure for characterizing crack growth.
In
the second part, the paper discusses a strain-based
methodology for lifetime prediction. The effect of creep
on
acceptable engineering temperatures and stresses is
considered for an allowable strain of
0.5%
and a failure
probability of
0.0001.
For a given stress and failure
time, a reduction in operating temperature of as much as
40
"C
is needed when strain rather than creep rupture is
considered as the failure criterion.
An
additional
25
"C
reduction is needed to limit the failure probability to
0.0001.
INTRODUCTION
Silicon nitride was developed originally as a
material for gas turbines and is supposed to be
competitive with air-cooled superalloys that can operate
in turbines with inlet temperatures in excess of
1300
"C.
To be economical, silicon nitride has to be used in an
uncooled state and must be resistant to creep,
creep-rupture and corrosion at high temperatures.
In
addition, because stresses can be very high during heat-
up and "trip" conditions, it also has to be resistant to
failure at low temperatures, where brittle rupture and
subcritical crack growth are problems.
Many of these goals have been achieved. Today,
several commercial grades of silicon nitride have the
requisite fracture toughness and resistance to subcritical
crack growth needed for structural reliability at low
temperatures, and, therefore, are also suitable for high
temperature operation. To be sure, there are still serious
problems that must be overcome before silicon nitride
can be used in turbines. Coatings must be developed to
protect silicon nitride from water attack by
high-pressure steam at elevated temperatures, and
improved toughness under severe impact conditions is
necessary to resist impact by metal pieces ingested or
generated by turbines during operation'. These
problems are currently being investigated in a number
of industrial and government laboratories.
To ensure long term reliability, techniques to
predict lifetime also had to be developed. Over the
years, two general methods of lifetime prediction were
developed; one is based
on
toughness, strength and
crack growth susceptibility, the other
on
parameters
related to creep and creep rupture behavior. Other
modes of failure in ceramics (pit formation due to
oxidation*, evaporation of Sic and Si3N4 due to water
attack', surface damage due to hard particle impact',
etc.)
are
not considered here. No general method of
handling these causes of failure has yet been developed.
The first set of methods, is fracture mechanics
based. Subcritical crack growth from microstructural
defects normally present in the body
is
assumed to limit
lifetime. Under the influence of external stresses, cracks
grow from the defects until they reached a critical size,
at which point crack growth accelerates and failure
occurs. Using the framework of fracture mechanics,
relationships were developed to describe lifetime as a
function temperature and applied stress. Although the
theory of fracture mechanics is used,
no
prior
knowledge of the underlying causes of subcritical crack
growth is required for the method. Simple power-law
equations of applied stress and failure stress are used
for lifetime prediction.
The second method of lifetime prediction applies to
failure
at
elevated temperature and is based
on
the creep
and creep rupture behavior. Lifetime is predicted from
the
creep behavior, either by assuming a fixed strain to
failure (the part becomes too large for its function), or
from an empirical relationship between creep rupture
lifetime and creep rate,
e.g.,
the
Monkman-Grant
relationship3. The form of the creep equation is based
on
a theoretical treatment of creep behavior. Therefore,
the better the prediction of creep rate, the more accurate
the lifetime prediction.
Finally, both techniques just mentioned give a
median or average prediction of lifetime.
In
real design
situations, knowledge of
the
scatter in lifetime
prediction is needed in addition to the mean or median
prediction. This requirement necessitates the use of
statistics in the lifetime prediction scheme
so
that
lifetime can
be
predicted at low failure probability. The
techniques that are used for high and low temperature
predictions differ because the modes of failure differ
substantially.
In
this paper, we discuss the techniques that are
used to predict component lifetime and the scatter
in
lifetime. Two modes of failure are assumed4. At low
temperatures subcritical crack growth from preexisting
defects is assumed to be the main cause of failure. At
109