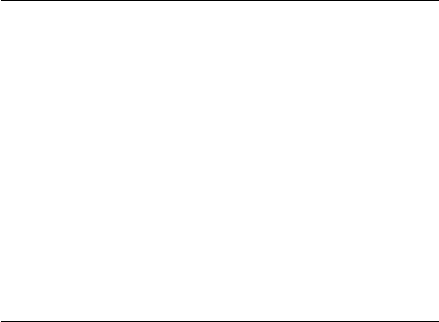
UPGRADING RESIDUES 453
Table 11.2. Typical operating conditions and yields from
flexi-coking
Feed
Cut range,
◦
F TBP + 1,050
◦
API 3.0
Sulfur, wt% 6.0
Nitrogen, Wppm 4,800
Condradson carbon, wt% 27.7
Metals, Wppm 269
Yields based on fresh feed
H
2
S, wt% 1.45
C
4
s and lighter, wt% 10.29
C
5
to 370
◦
F, LV% 15.0
370–650
◦
F, LV% 16.7
650–975
◦
F, LV% 28.4
Purge coke, wt% 0.69
Coker gas, Scf/Bbl 10.79 (LHV = 127 Btu/Scf)
The coke leaving the reactor enters the heater vessel, where sufficient coke is converted
into CO/CO
2
in the presence of air. This conversion of the coke provides the heat for
cracking which is subsequently transmitted to the reactor by a hot coke stream. The net
coke make leaves the heater and enters the gasifier vessel. Air and steam are introduced
into the gasifier to react with the coke producing a low Btu gas consisting predomi-
nately of hydrogen, CO, CO
2
, and nitrogen. This gas together with some excess air is
transferred to the heater, and leaves this vessel to be suitably cleaned and cooled.
Flexi-coking is an extinctive process. By continuous recycle of heavy oil stream all
the feed is converted into distillate fractions, refinery gas, and low Btu gas. There is
a very small coke purge stream which amounts to about 0.4–0.8 wt% of fresh feed.
When suitably hydrotreated the fractionated streams from the flexi-coker provide good
quality products. Hydrotreated coker naphtha provides an excellent high-naphthene
feed to the catalytic reformer. Typical yields from a flexi-coker based on Arabian
residue are shown in Table 11.2.
This process is quite flexible as to the quality of the feedstock, most of the metals are
removed with the coke purge. Condradson carbon content of the feed does not affect
the yield as may be expected. Where an economic use can be found for the low Btu
gas, the process offers an attractive route for upgrading low quality fuel oil.
The principles of and correlations associated with thermal cracking processes
The soaking volume concept
The design of a thermal cracker is keyed to the configuration and temperature pro-
file across the heater and soaking drum or soaking coil. The degree of cracking is