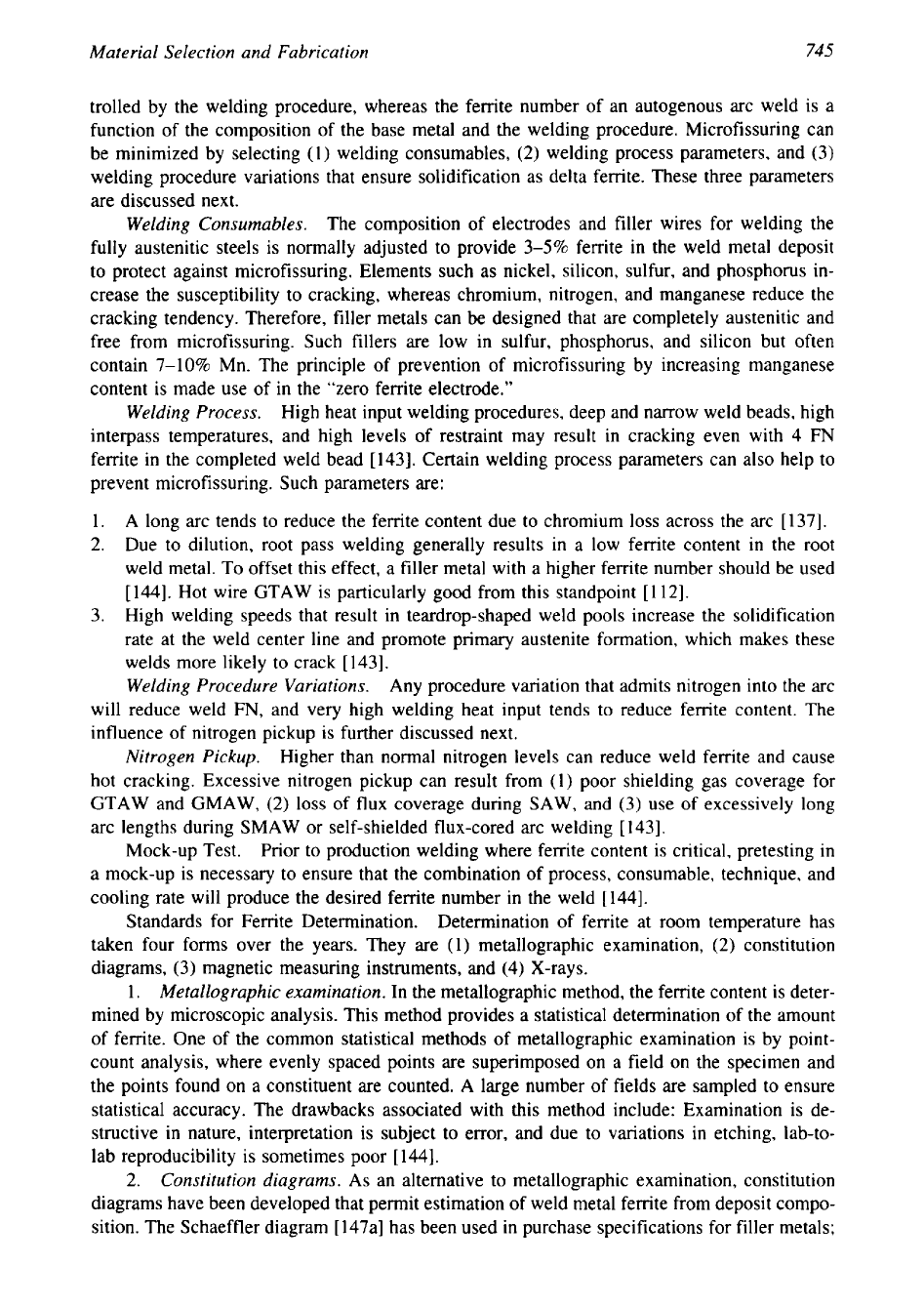
745
Material Selection and Fabrication
trolled by the welding procedure, whereas the ferrite number of an autogenous arc weld is a
function of the composition of the base metal and the welding procedure. Microfissuring can
be minimized by selecting
(1)
welding consumables,
(2)
welding process parameters, and
(3)
welding procedure variations that ensure solidification as delta ferrite. These three parameters
are discussed next.
Welding Consumables.
The composition of electrodes and filler wires for welding the
fully austenitic steels is normally adjusted to provide
3-5%
ferrite in the weld metal deposit
to protect against microfissuring. Elements such as nickel, silicon, sulfur, and phosphorus in-
crease the susceptibility to cracking, whereas chromium, nitrogen, and manganese reduce the
cracking tendency. Therefore, filler metals can be designed that are completely austenitic and
free from microfissuring. Such fillers are low in sulfur, phosphorus, and silicon but often
contain
7-10%
Mn. The principle of prevention of microfissuring by increasing manganese
content is made use of in the “zero ferrite electrode.”
Welding Process.
High heat input welding procedures, deep and narrow weld beads, high
interpass temperatures, and high levels of restraint may result in cracking even with
4
FN
ferrite in the completed weld bead
[
1431.
Certain welding process parameters can also help to
prevent microfissuring. Such parameters are:
1.
A long arc tends to reduce the ferrite content due to chromium loss across the arc
[137].
2.
Due to dilution, root pass welding generally results in a low ferrite content in the root
weld metal. To offset this effect, a filler metal with a higher ferrite number should be used
[
1441.
Hot wire GTAW is particularly good from this standpoint
[
1121.
3.
High welding speeds that result in teardrop-shaped weld pools increase the solidification
rate at the weld center line and promote primary austenite formation, which makes these
welds more likely to crack
[
1431.
Welding Procedure Variations.
Any procedure variation that admits nitrogen into the arc
will reduce weld
FN,
and very high welding heat input tends to reduce ferrite content. The
influence of nitrogen pickup is further discussed next.
Nitrogen Pickup.
Higher than normal nitrogen levels can reduce weld ferrite and cause
hot cracking. Excessive nitrogen pickup can result from
(1)
poor shielding gas coverage for
GTAW and GMAW,
(2)
loss of flux coverage during
SAW,
and
(3)
use of excessively long
arc lengths during SMAW or self-shielded flux-cored arc welding
[
1431.
Mock-up Test.
Prior to production welding where ferrite content is critical, pretesting
in
a mock-up is necessary to ensure that the combination of process, consumable, technique, and
cooling rate will produce the desired ferrite number in the weld
[
1441.
Standards for Ferrite Determination. Determination
of ferrite at room temperature has
taken four forms over the years. They are
(1)
metallographic examination,
(2)
constitution
diagrams,
(3)
magnetic measuring instruments, and
(4)
X-rays.
1.
Metallographic examination.
In the metallographic method, the ferrite content is deter-
mined by microscopic analysis. This method provides a statistical determination of the amount
of
ferrite. One of the common statistical methods of metallographic examination is by point-
count analysis, where evenly spaced points are superimposed on a field on the specimen and
the points found on a constituent are counted. A large number of fields are sampled to ensure
statistical accuracy. The drawbacks associated with this method include: Examination is de-
structive in nature, interpretation is subject to error, and due to variations in etching, lab-to-
lab reproducibility is sometimes poor
[
1441.
2.
Constitution diagrams.
As an alternative to metallographic examination, constitution
diagrams have been developed that permit estimation of weld metal ferrite from deposit compo-
sition. The Schaeffler diagram
[
147al
has been used in purchase specifications for filler metals;