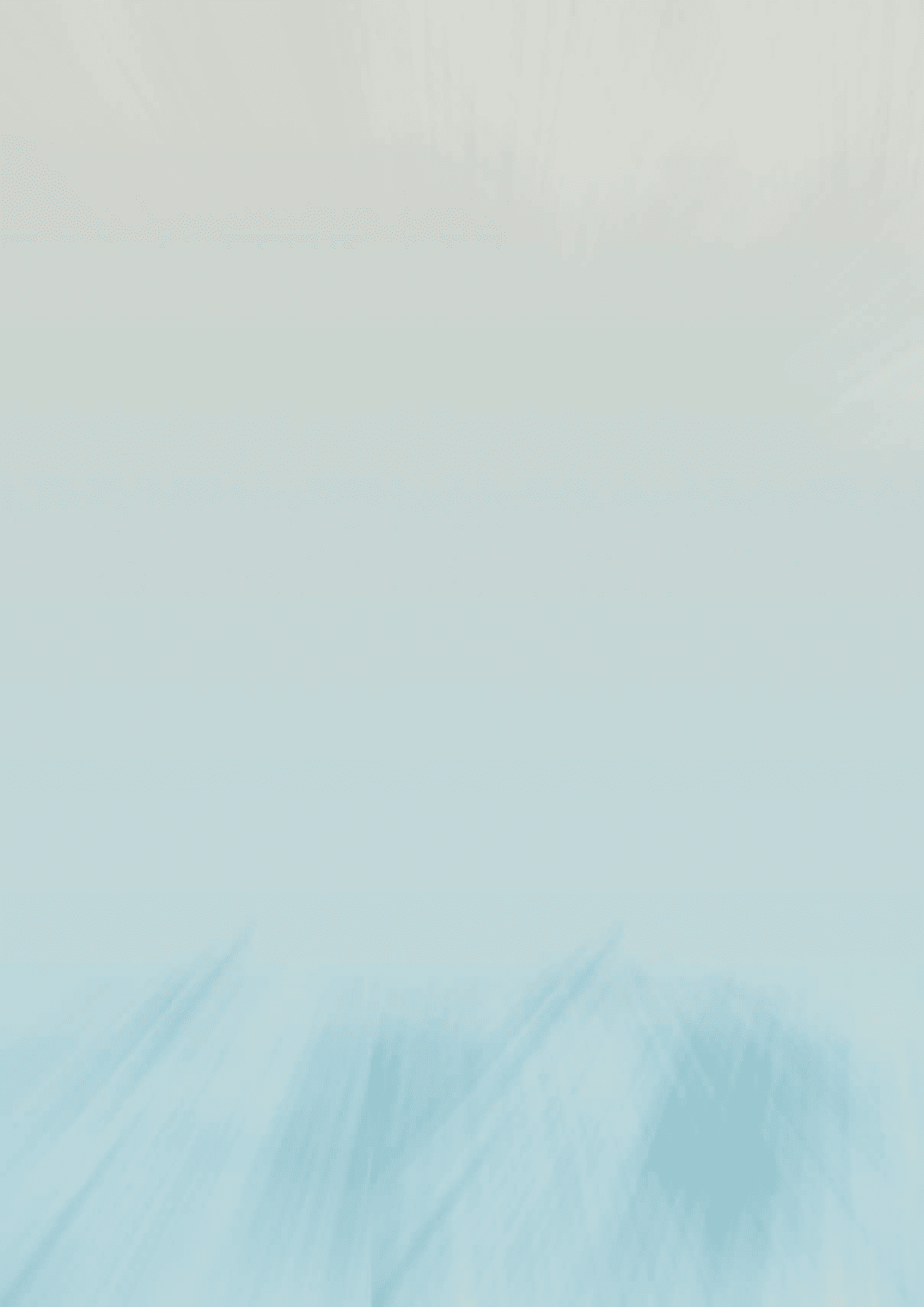
• высокое качество поверхности и геометрическая точ-
ность отливок;
• значительное уменьшение в них поверхностных и внут-
ренних дефектов;
• снижение трудоемкости финишных операций и меха-
нообработки;
• возможность использования недорогой деревянной
модельной оснастки;
• существенное снижение расхода формовочных мате-
риалов из-за отсутствия модельной смеси
• высокая экологичность процесса.
Подготовка производства начинается с разработки техно-
логии изготовления отливок с использованием программы
MAGMAsoft, разработки чертежей оснастки для изготовления
отливок с использованием конструкторской САПР на базе
программы «Solid Edge».
Оснастка производится на станках с ЧПУ, стержни – на
восьми автоматах фирмы Laempe (Германия). Выплавка
стали – в пяти дуговых печах ДСП-25-Н2-У4.
Известно, что «Промлит» первым в России освоил зна-
чительные объемы производства крупных стальных же-
лезнодорожных отливок инновационным ВПФ-процессом.
Прокомментируйте пожалуйста эффективность выбранной
технологии изготовления литейных форм и современный
уровень литейного производства «Промлита»?
В начале 2000-х гг. многие заводы, как «новички», так и
традиционно выпускавшие крупные ж/д- отливки, присту-
пили к модернизации литейного производства по новым
проектам с использованием ХТС, ЖСС и традиционных
песчано-глинистых смесей (ПГС). «Промлит» позднее дру-
гих вступил в конкурентную борьбу за выпуск отливок рама
боковая и балка надрессорная. Но при этом, первым освоил
значительный их объем для решения проблем РЖД. Более
того, практически сразу после монтажа АФЛ на эти отливки
были получены российские сертификаты, а позднее и сер-
тификат американских железных дорог.
Первые испытания отливок на циклические нагрузки сра-
зу дали наилучшие из всех известных на тот момент в РЖД
примеров результаты. Теперь можно смело утверждать, что
«Промлит» сделал тогда все возможное для создания нового
производства крупных стальных отливок, в сравнении с рядом
заводов, работающих десятки лет по отлаженным, традици-
онным технологиям. И в этом существенный вклад иннова-
ционной технологии ВПФ, более простой и управляемой, чем
традиционные процессы.
В чем вы видите существенное различие технологий
ПГС, ХТС и ВПФ применительно к номенклатуре крупных
ж/д- отливок?
«Промлит» имеет опыт производства этих отливок на двух
АФЛ с разными технологиями формообразования – ПГС и
ВПФ. Могу подтвердить, что брак на АФЛ по ВПФ в несколько
раз ниже, чем на АФЛ по ПГС-технологии. Так, брак отливок,
полученных ВПФ, снизился до 0,8%, что существенно мень-
ше, чем при производстве аналогичных отливок каким-либо
другим методом. При этом, себестоимость таких отливок
также существенно ниже. Этих двух факторов – высокого
качества отливок и низкой себестоимости их изготовления,
достаточно для качественного сравнения технологий.
Но проверкой стал опыт производства реальных отливок,
и сегодня «Промлит» – самый крупный из вновь созданных,
после 2000 г., производств ж/д- отливок. Ближайший наш
конкурент по объемам производства – завод «Тианруй» в
Китае, и также – на базе АФЛ по технологии ВПФ. Что каса-
ется ХТС-процесса, нам неизвестны сколь-либо значительные
объемы производства этой технологией рам боковых и балок
надрессорных в России, Белоруссии и Украине в последнее
время. А в Китае даже сняли лицензии на изготовление
крупных ж/д- отливок в формах из ХТС.
На «Промлите» технология ВПФ освоена на двух участках,
где производятся и другие отливки, например, корпус заднего
моста трактора. Также на «Курганмашзаводе» входящем в
наш Концерн, уже более 25 лет работает АФЛ по ВПФ для
самой широкой номенклатуры стальных отливок.
В структуре Концерна «Тракторные заводы» успешно
работают и современные АФЛ по ПГС-процессу, например,
на заводе Luitpoldhьtte в г. Амберг на юго-востоке Германии
– на двух АФЛ Сейатцу-процессом выпускается большая
номенклатура чугунных блоков цилиндров, некоторые из ко-
торых поставляются и моторостроительным заводам России.
Очевидно, что для каждой номенклатуры отливок и сплава
необходимо подбирать свою оптимальную технологию.
Какие российские заводы для модернизации литейного
производства крупных ж/д- отливок последовали по пути
выбранной вами технологии ВПФ?
Это, в первую очередь, три завода России; Тихвинский
вагоностроительный (ТВСЗ); «ВКМ-Сталь», г.Саранск;
«Ремпутьмаш», г.Людиново. После такого широкомасштаб-
ного распространения инновационной технологии формовки
«Промлит» стал более открытым и представил на выставке
«Литмаш» в мае 2010 г. усовершенствованную конструкцию
рамы №5. Мы сертифицировали четыре типа балок и три типа
боковых рам по технологии ВПФ и два типа рам по ПГФ-тех-
нологии. Также освоено производство «Коломенских» балок
и рам для тяжелой 100-т тележки (с нагрузкой на ось 25 т).
В чем сегодня вы видите первостепенную задачу
дальнейшей модернизации литейного производства «Про-
млита»?
Бесспорно это – широкомасштабная автоматизация и
роботизация производства-
Завод «Промлит», построенный в середине 70-х гг. одним
из последних во времена СССР, после преодоления последс-
твий очередного кризиса в отечественном машиностроении
одним из первых приступил к модернизации литейного
производства по инновационной технологии.
Стратегия продвижения и стремление быть первым
среди конкурентов в жестких условиях мировой экономики
не оставляют альтернативы программам автоматизации и
роботизации его литейного производства.
Благодарю за исчерпывающие ответы.
Интервью взяла И.А. Яскевич