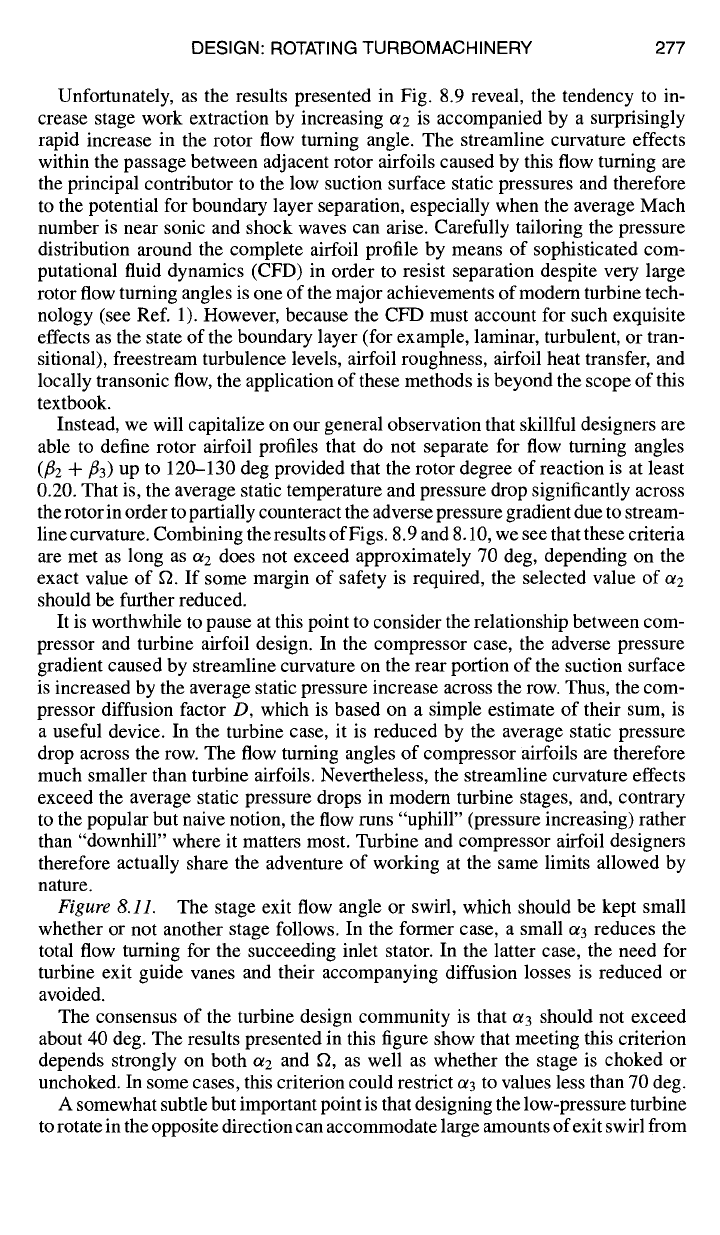
DESIGN: ROTATING TURBOMACHINERY 277
Unfortunately, as the results presented in Fig. 8.9 reveal, the tendency to in-
crease stage work extraction by increasing a2 is accompanied by a surprisingly
rapid increase in the rotor flow turning angle. The streamline curvature effects
within the passage between adjacent rotor airfoils caused by this flow turning are
the principal contributor to the low suction surface static pressures and therefore
to the potential for boundary layer separation, especially when the average Mach
number is near sonic and shock waves can arise. Carefully tailoring the pressure
distribution around the complete airfoil profile by means of sophisticated com-
putational fluid dynamics (CFD) in order to resist separation despite very large
rotor flow turning angles is one of the major achievements of modern turbine tech-
nology (see Ref. 1). However, because the CFD must account for such exquisite
effects as the state of the boundary layer (for example, laminar, turbulent, or tran-
sitional), freestream turbulence levels, airfoil roughness, airfoil heat transfer, and
locally transonic flow, the application of these methods is beyond the scope of this
textbook.
Instead, we will capitalize on our general observation that skillful designers are
able to define rotor airfoil profiles that do not separate for flow turning angles
(/32 +/33) up to 120-130 deg provided that the rotor degree of reaction is at least
0.20. That is, the average static temperature and pressure drop significantly across
the rotor in order to partially counteract the adverse pressure gradient due to stream-
line curvature. Combining the results of Figs. 8.9 and 8.10, we see that these criteria
are met as long as or2 does not exceed approximately 70 deg, depending on the
exact value of f2. If some margin of safety is required, the selected value of a2
should be further reduced.
It is worthwhile to pause at this point to consider the relationship between com-
pressor and turbine airfoil design. In the compressor case, the adverse pressure
gradient caused by streamline curvature on the rear portion of the suction surface
is increased by the average static pressure increase across the row. Thus, the com-
pressor diffusion factor D, which is based on a simple estimate of their sum, is
a useful device. In the turbine case, it is reduced by the average static pressure
drop across the row. The flow turning angles of compressor airfoils are therefore
much smaller than turbine airfoils. Nevertheless, the streamline curvature effects
exceed the average static pressure drops in modern turbine stages, and, contrary
to the popular but naive notion, the flow runs "uphill" (pressure increasing) rather
than "downhill" where it matters most. Turbine and compressor airfoil designers
therefore actually share the adventure of working at the same limits allowed by
nature.
Figure 8.11.
The stage exit flow angle or swirl, which should be kept small
whether or not another stage follows. In the former case, a small or3 reduces the
total flow turning for the succeeding inlet stator. In the latter case, the need for
turbine exit guide vanes and their accompanying diffusion losses is reduced or
avoided.
The consensus of the turbine design community is that or3 should not exceed
about 40 deg. The results presented in this figure show that meeting this criterion
depends strongly on both oe2 and f2, as well as whether the stage is choked or
unchoked. In some cases, this criterion could restrict ~3 to values less than 70 deg.
A somewhat subtle but important point is that designing the low-pressure turbine
to rotate in the opposite direction can accommodate large amounts of exit swirl from