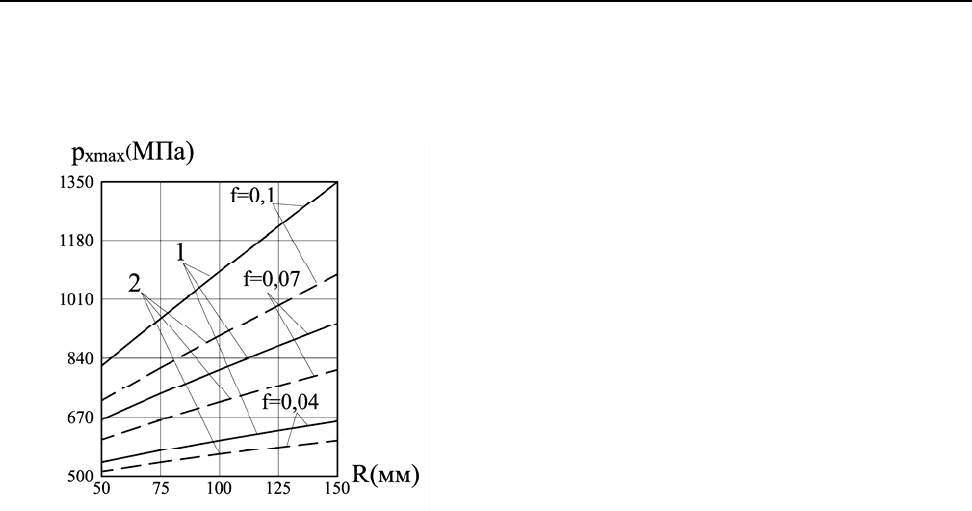
Обработка материалов давлением № 1 (20), 2009
Для гарантированной точности геометрических характеристик необходимо обеспечивать
в предыдущих переделах колебание продольной разнотолщинности не более 10 %, что обеспечи-
вается современным прокатным производством [2]. Равенство вытяжек в этом случае обеспечива-
ется путем саморегулирования толщины за счет межслойных сил трения [3].
Рис. 3. Расчетные распределения
максимальных контактных напряжений
maxx
p при сдвоенной прокатке в рабочих
валках радиусом
R
при различных значениях
коэффициента внешнего трения
(1 – , 2 – ммh
3,0
0
=
Σ
; 3,0=
; сталь 08кп)
Важнейшим вопросом, касающимся
оценки условий реализации различных техноло-
гических схем процесса сдвоенной прокатки,
является прогнозирование вероятности схваты-
вания (сваривания) поверхностей сдваиваемых
лент и полос, определяемой максимальными
значениями нормальных контактных напряже-
ний
maxx
p [4]. При этом в момент разрушения
окисных пленок и начала схватывания поверх-
ностей, уровень максимальных нормальных кон-
тактных напряжений в очаге деформации, со-
гласно критерию С. А. Голованенко [5], состав-
ляет
тx
p
3
max
.
Из результатов анализа представленных
расчетных распределений (рис. 3), следует, что
снижение уровней
maxx
p , а вместе с этим и
обеспечение сдвоенной прокатки без схватыва-
ния внутренних поверхностей полос могут быть
обеспечены за счет уменьшения радиусов рабо-
чих валков.
ВЫВОДЫ
Получены критериальные оценки обеспечения стабильности процесса сдвоенной про-
катки с точки зрения равенства вытяжек составляющих в виде технологических требований к
предыдущим переделам горячей и холодной прокатки. Было установлено, что колебание ме-
ханических свойств и геометрических характеристик сдваиваемых полос относительно друг
друга не должно превышать 10 %. Снижение вероятности свариваемости сдваиваемых лент
при
фиксированных значениях их исходной и конечной толщины может быть обеспечено за
счет уменьшения радиусов рабочих валков.
ЛИТЕРАТУРА
1. Раздельное регулирование толщин полос при прокатке их в наложенном состоянии / С. Д. Адамский,
В. И. Мелешко, А. П. Качайлов, А. И. Шевченко // Прокатка широкополосной стали : сб. науч. тр. – ИЧМ МЧМ СССР. – М.:
Металлургия, 1988. – С. 49–52.
2. Математическое моделирование исходных данных на проектирование гидравлических нажимных устройств
прокатного стана / В. А. Федоринов, С. В. Новоселов, С. К. Добряк и др. // Удосконалення процесів та обладнання обробки
тиском у металургії і машинобудуванні : зб. наук. пр. – Краматорськ: ДДМА. – 2001. – С. 441–445.
3. Исследование напряженно-деформированного состояния металла и энергосиловых параметров при сдво-
енной
прокатке лент и полос / В. А. Федоринов, А. В. Сатонин, В. В. Дворжак, А. А. Сатонин // Сб. науч. тр. – Алчевск :
ДГТУ. – 2007. – С. 126–134.
4. Внедрение автоматической системы транспортировки и смотки тончайших полос широкополосного стана /
П. П .Чернов, В. А. Третьяков, Е. А. Варшавский и др. // Черная металургія: Бюл. НТИ. – 2004. – № 8. – С. 53–56.
5. Голованенко А. С. Сварка прокаткой биметаллов / Голованенко А. С. – М.: Металлургия, 1977. – 158 с.
Федоринов В. А. – канд. техн. наук, проф. ДГМА;
Махмудов К. Д. – канд. техн. наук, доц., филиал ДагГТУ;
Дворжак В. В. – канд. техн. наук, ст. преп. ДГМА;
Закарвашевич Н. А. – студент ДГМА.
ДГМА - Донбасская государственная машиностроительная академия, г. Краматорск;
ДагГТУ – Дагестанский государственный технический университет, г. Каспийск, Россия.
E-mail: amm@dgma.donetsk.ua