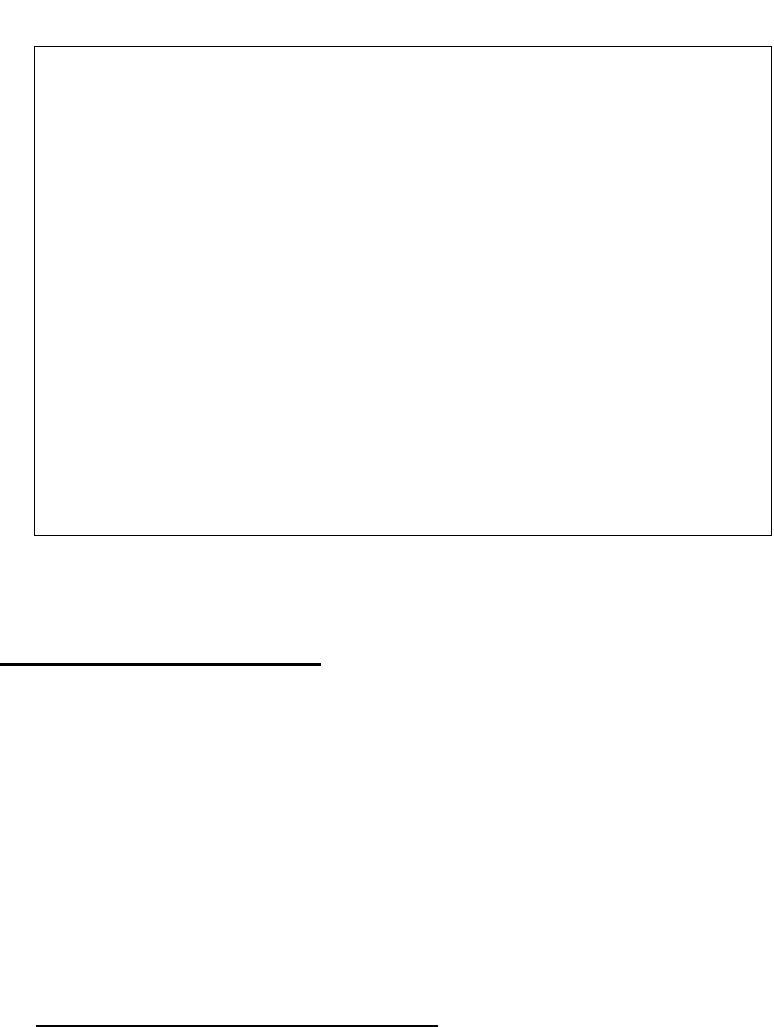
5. Monitor the effectiveness of administrative, technical, and physical controls, and
identify deficiencies that must be resolved.
EC:SG3 MANAGE FACILITY ASSET RISK
Operational and environmental risks to facility assets are identified and managed.
The management of risk for facility assets is the specific application of risk man-
agement tools, techniques, and methods to the facility assets whether or not they
are owned by the organization. Facility assets are more prone to certain types of
operational risk, particularly external conditions such as failures of public infra-
structure and natural disasters. In addition, because facility assets are often not in
the direct control of the organization (because they are leased or shared), the
organization may be exposed to additional risks that would generally be
detectable and controllable if the organization owned and maintained them. As
hubs of activities and services, facility assets are subject to risks that can result in
widespread and cascading consequences to the organization.
EC:SG3.SP1 IDENTIFY AND ASSESS FACILITY ASSET RISK
Risks to facility assets are periodically identified and assessed.
Operational risks that can affect facility assets must be identified and mitigated in
order to actively manage the resilience of these assets and, more important, the
resilience of services to which these assets are associated. Special attention
• doors—fire rating, directional opening, resistance to being forced open, intrusion
detection alarms, type of locks
• windows—characteristics of window material, intrusion detection mechanism,
placement of windows
• ceiling—fire rating, load, waterproof (especially in shared tenant facilities), drop ceiling
• floor—fire rating, load, raised floor, electrical grounding, non-conductive material
• heating, ventilation, air conditioning (HVAC)—power source, protected intake vents
to prevent tampering, emergency power off, air pressure, specialized chilling and
cooling for technical equipment
• power supplies—backup or redundant power supply, clean power supply, circuit
breakers, access to power distribution panels, emergency power off
• liquid and gas lines—accessible shutoff valve, positive flow, leakage sensor, placement
of liquid and gas lines
• fire detection and suppression—fire or smoke detector and alarm, gas discharge
system, placement of detectors and sprinkler heads
• emergency lighting—essential power supply and battery for emergency lighting
• moisture—water or liquid detection and alarm
• cables and cableways—routing, protection from fire, moisture, and unauthorized
access
280 PART THREE CERT-RMM PROCESS AREAS