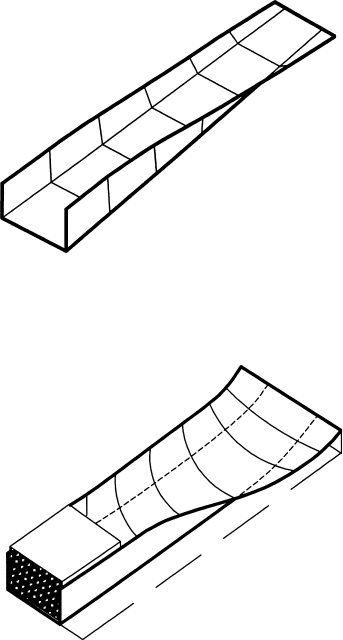
15.2.3 Equipment and Tooling
Roll forming equipment purchased today wi ll operate well in the mid and second partofthe twenty-first
century. Therefore, progressivecompanies should look ahead into the futurewhen procuring equipment,
rather than applying the “good old” (40 to 50 years old), but outdated, technology.
Average roll forming lines are still running between 60 to 180 ft/min (20 to 60 m/min). To increase
efficiency,manynew roll forming lines will run at aspeed of 600 to 800 ft/min (200 to 250 m/min)
or faster.
The speed of the rollforming lines, in manycases, has been restricted by the number of strokes per
minute of the mechanical, pneumatic, or hydraulic presses. The new compact hydraulic or other presses
havethe capacity of 150 to 200 strokes per minute.
Increased speed is not an impossible dream, lines havealready been developed and are operated at
750 ft/min speed (230 m/min), cutting 7500 pieces per minute, in other wordsproducing about half a
million 1-in. (25-mm) long pieces per hour.
15.2.4 Flow of Material in the Mill
In the present systems, in almost all cases, the pass line is kept in astraight horizontal plane or it is
inclined with asmall increment frompass to pass. When forming asection, say, a“U” channel, the
straight bend lines travel in the horizontal plane, and the edges not only move the same distanceforward,
but also move upwards at the same time. Hence,
the edges travelalonger path than the straight
bends as shown in Figure15.1.Ifthe stresses at the
edges exceed the yield point, then the finished
edges will remain permanently wavy.
It can be easily demonstrated that the “natural
flow” is different. After forming the last 10 to 12 in.
(about 250 to 300 mm) of a60to70in. (about
2-m) long metal strip to the finished shape, or
bending awallpaper of the same length to a2£ 4
(Figure15.2)and keeping the other end of the strip
straight, the strip willtake the shape of the “least
resistance” or “lowest stress.”
Viewingthismodel from theside(Figure 15.3a),it
is obvious that thebottompartofthe sectiondoes
nottravelinastraightplane.The edgesofthe
wallpaperare nottorn, whichindicates that the
aboveshape,followingthe “natural flow” (often
called “downhillflow”) hasgenerated theleast
amount of stressand strain.Inthe presentlyused
roll formingsystems,the entry endis“forced down”
to travel horizontally (see Figure 15.3b),thus
creating stresses at theedges.
If the“naturalflow”isbetterthanthe
“horizontal flow, ”then whyisthis method not
used? The main reason is that for the sake of cost,
convenience, and habit, the mill driveshafts are
positioned on the same level, especially in North
America.
To followthe “natural flow” with all the drive
shafts in one level, the mill would require larger
FIGURE 15.1 The edge of the “U” channel travels a
longer path than the bent corner.
FIGURE 15.2 The stresses are minimized when the
“natural flow” is followed.
Unusual, New,and Future Roll Forming Technologies 15-3