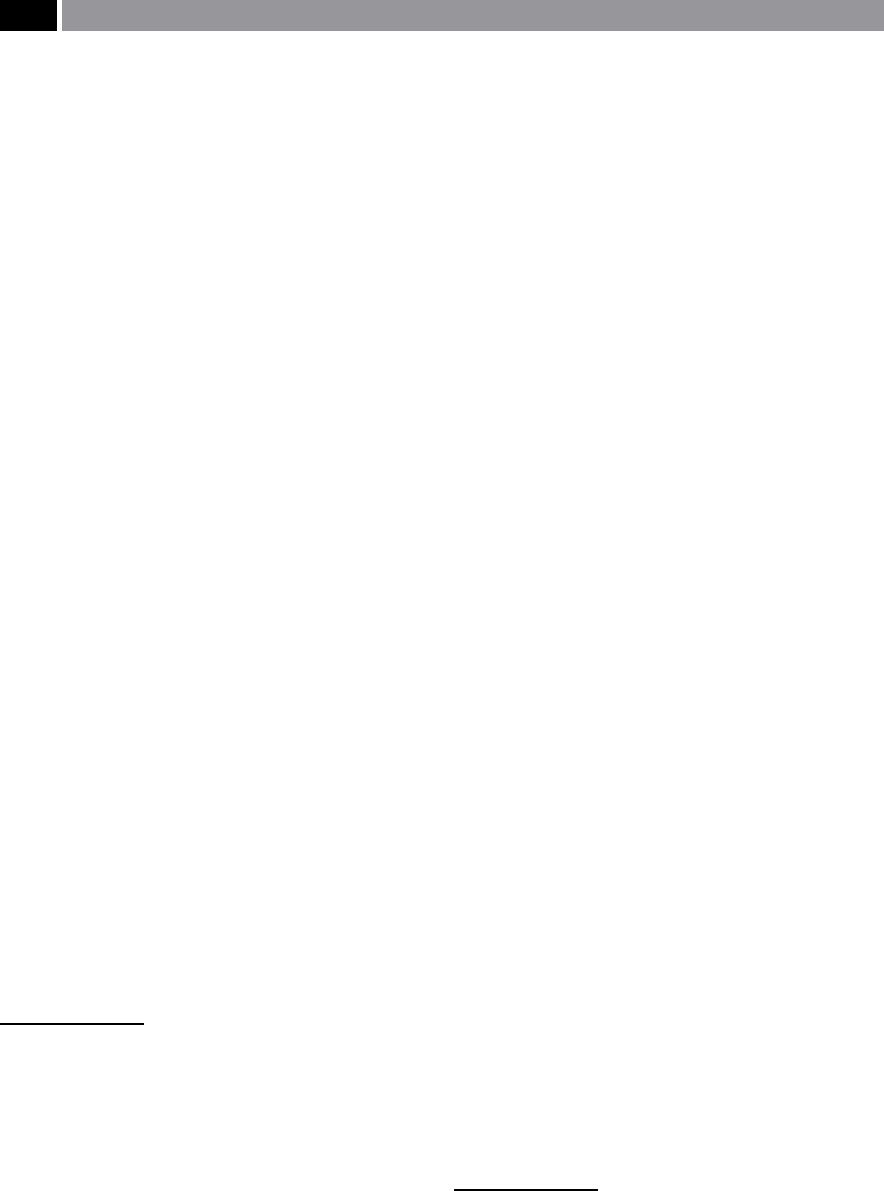
3.1.6 Special-Purpose, or Customised
Drilling and Multi-Spindle
Drilling
Most of today’s Special-purpose, or Customised Drills
and Multi-spindle drills are normally designed and
manufactured to meet the following criteria:
•
Long production runs
25
– these enable the extra
cost of this purpose-designed and built tooling to
amortised
26
over the cost of the production period,
•
Short cycle times
27
– when time is the ‘essence of
importance’ in the production of the component,
but it is not necessarily related to the overall quan-
tity of the production run,
•
Tooling accuracy is reected in the part’s manufac-
ture – if for example the precision part must have
all its component features in accurate alignment,
or in a specic relationship to a particular datum
28
:
face, plane or point.
Special-purpose, or Customised tooling is normally
required if one, or several of the criteria mentioned
above are to be met. To have a tooling manufacturer
design special-purpose tooling to meet the production
demands of manufacture, is not undertaken lightly, as
for complex tooling, its: design, build and prove-out,
prior to use, could prove to be expensive. However,
many companies resort to this type of custom-built
tooling, because it is the only way that the product can
be manufactured economically. Oen, multiple fea-
tures are incorporated into just one tool, typically for
hole- and post-hole making operations, such as those
depicted in Fig. 56a. A relatively simple example of
this special-purpose tooling is illustrated in Fig. 56b,
where three production operations for the manufac-
ture of the female part of the pull-stud mechanism for
a milling cutter toolholder is depicted, namely, drilling,
25 Long production runs usually refers to some form of continu-
ous production , or large batch sizes, of > 5,000 components,
to make the cost of the Special-purpose tooling viable.
26 Amortisation, refers to the ‘pay-back’ of the tooling over the
‘life’ of the production of the parts produced.
27 Short cycle times, are considered to be the quickest time that the
part can be produced, under ‘standard’ machining conditions.
28 Datum – the term refers to origin of the measurements for
the particular component feature, which could be from a face,
plane, or point.
chamfering and counter-boring. In this case, not only
does the usage of special-purpose tooling here seem
the obvious solution, as it combines these individual
operations in one, it has the advantage of meeting all
three of the production criteria listed above, with the
added advantages of both using fewer tools and utilis-
ing less space in the tool magazine. Some special-pur-
pose tools are very complex in their design and quite
sophisticated in operation, but their supplementary
cost more than outweighs this by the production gains
oered by their consequent implementation.
M
ulti-spindle drilling
29
tooling is ideal when a series
of hole patterns are required on a component, such as
for specic congurations of: pitch circle diameters,
hole grid patterns, line of holes, or a combination of
these (i.e. see examples of specic patterns in Fig. 57
– top right). Hole pitch circle diameters can easily be
accommodated, for large and small pitch diameters on
the same tooling, Likewise, hole line and grid patterns
can be quite diverse, within the diametral area of the
‘cluster plate’ (i.e. see Fig. 57 – top le).
Multi-spindle drilling heads utilise a main drive
gear which is engaged with an idler and then onto the
drill spindle gear, this being attached to the individual
drill (i.e. see Fig. 57 – exploded view of a typical sys-
tem). e cluster plate orientates the individual drill
spindles and their rotational speeds can be margin-
ally increased, or decreased, by changing the driver-
to-driven gear ratio, moreover, their rotational direc-
tion can be changed by the introduction of another
idler into the gear train. erefore, if additional idlers
are present, to change the drill’s rotation, then the an
appropriate le-hand drill would be required here.
By purposefully modifying each drill’s rotational di-
rection, this has the advantage of minimising overall
torque eects on the multi-spindle drilling head, al-
lowing a large number of drills to be utilised for one
particular operation (i.e. see Fig. 57 – lower le-hand
photograph). An important point in utilising multi-
spindle drilling heads, is presetting their respective
drill lengths, so that they engage with the workpiece’s
surface at the correct height.
By the correct production application of both Spe-
cial-purpose and Multi-spindle drilling tooling, then
29 Multi-spindle tools, refer to more than one individual tool ro-
tating in its respective toolholder, enabling several holes to be
manufactured in just one operation.