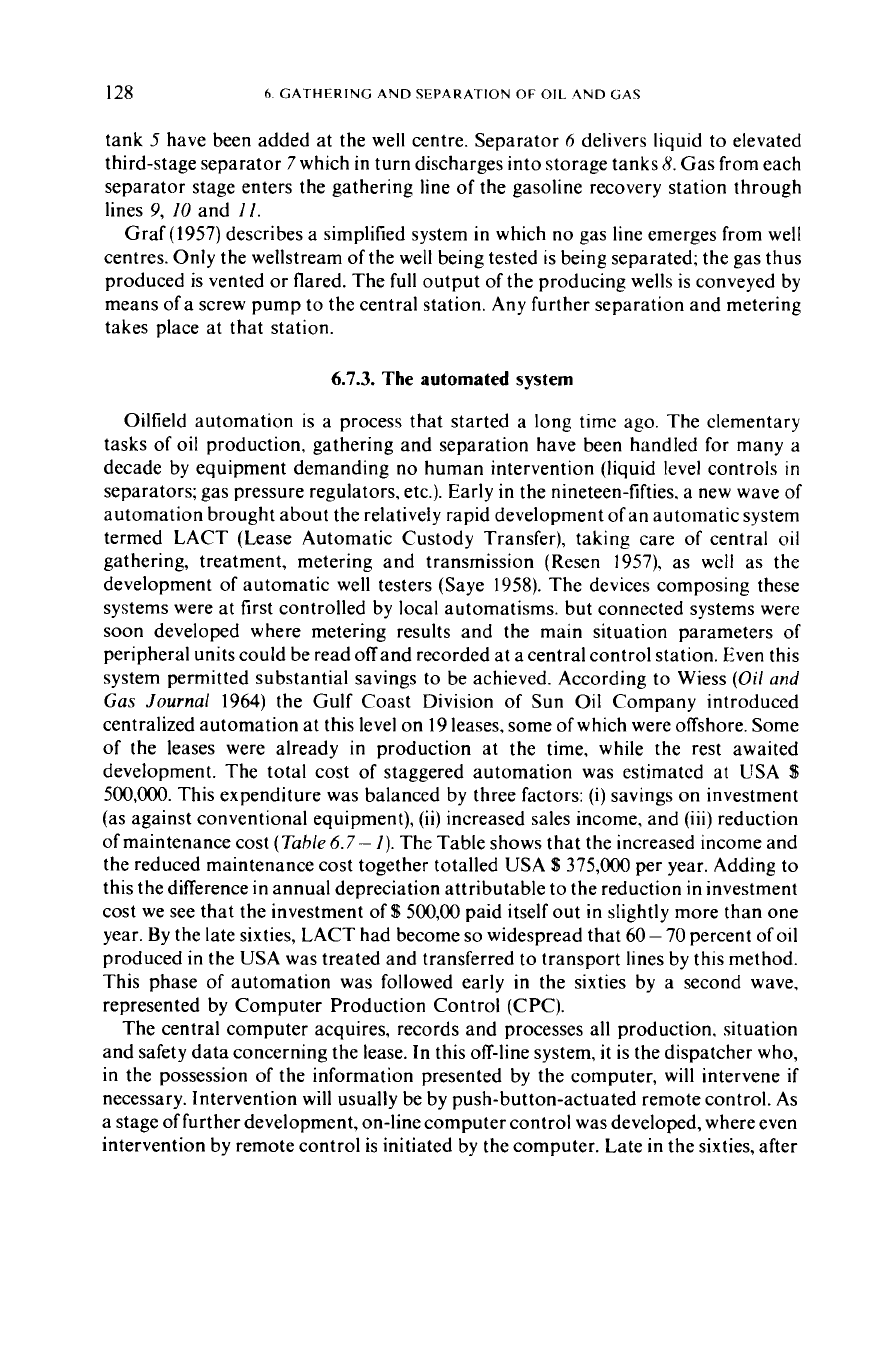
128
h
GATHERING AND SEPARATION
OF
OIL
AND
GAS
tank
5
have been added at the well centre. Separator
6
delivers liquid to elevated
third-stage separator
7
which in turn discharges into storage tanks
8.
Gas from each
separator stage enters the gathering line
of
the gasoline recovery station through
lines
9,
10
and
11.
Graf (1957) describes a simplified system in which no gas line emerges from well
centres.
Only
the wellstream of the well being tested is being separated; the gas thus
produced is vented
or
flared. The
full
output of the producing wells is conveyed by
means of a screw pump to the central station. Any further separation and metering
takes place at that station.
6.7.3.
The
automated system
Oilfield automation is a process that started a long time ago. The elementary
tasks of oil production, gathering and separation have been handled for many a
decade by equipment demanding no human intervention (liquid level controls
in
separators; gas pressure regulators, etc.). Early
in
the nineteen-fifties. a new wave
of
automation brought about the relatively rapid development of an automatic system
termed LACT (Lease Automatic Custody Transfer), taking care of central oil
gathering, treatment, metering and transmission (Resen 1957).
as
well as the
development of automatic well testers (Saye 1958). The devices composing these
systems were at first controlled by local automatisms. but connected systems were
soon developed where metering results and the main situation parameters of
peripheral units could be read off and recorded at a central control station. Even this
system permitted substantial savings to be achieved. According to Wiess
(Oil
and
Gas
Journal
1964)
the Gulf Coast Division of
Sun
Oil Company introduced
centralized automation at this level on 19 leases. some of which were offshore. Some
of the leases were already
in
production at the time, while the rest awaited
development. The total cost of staggered automation was estimated at USA
$
500,000. This expenditure was balanced by three factors:
(i)
savings on investment
(as against conventional equipment),
(ii)
increased sales income, and
(iii)
reduction
of maintenance cost
(Tuhle
6.7-
I).
The Table shows that the increased income and
the reduced maintenance cost together totalled
USA
8
375,000
per
year. Adding to
this the difference
in
annual depreciation attributable to the reduction
in
investment
cost we see that the investment of $500,00 paid itself out
in
slightly more than one
year. By the late sixties, LACT had become
so
widespread that
60
-
70 percent of
oil
produced
in
the USA was treated and transferred to transport lines by this method.
This phase of automation was followed early in the sixties by a second wave,
represented by Computer Production Control (CPC).
The central computer acquires, records and processes all production, situation
and safety data concerning the lease. In this off-line system,
it
is
the dispatcher who,
in
the possession of the information presented by the computer, will intervene
if
necessary. Intervention will usually be by push-button-actuated remote control. As
a stage of further development, on-line computer control was developed, where even
intervention by remote control is initiated by the computer. Late in the sixties, after