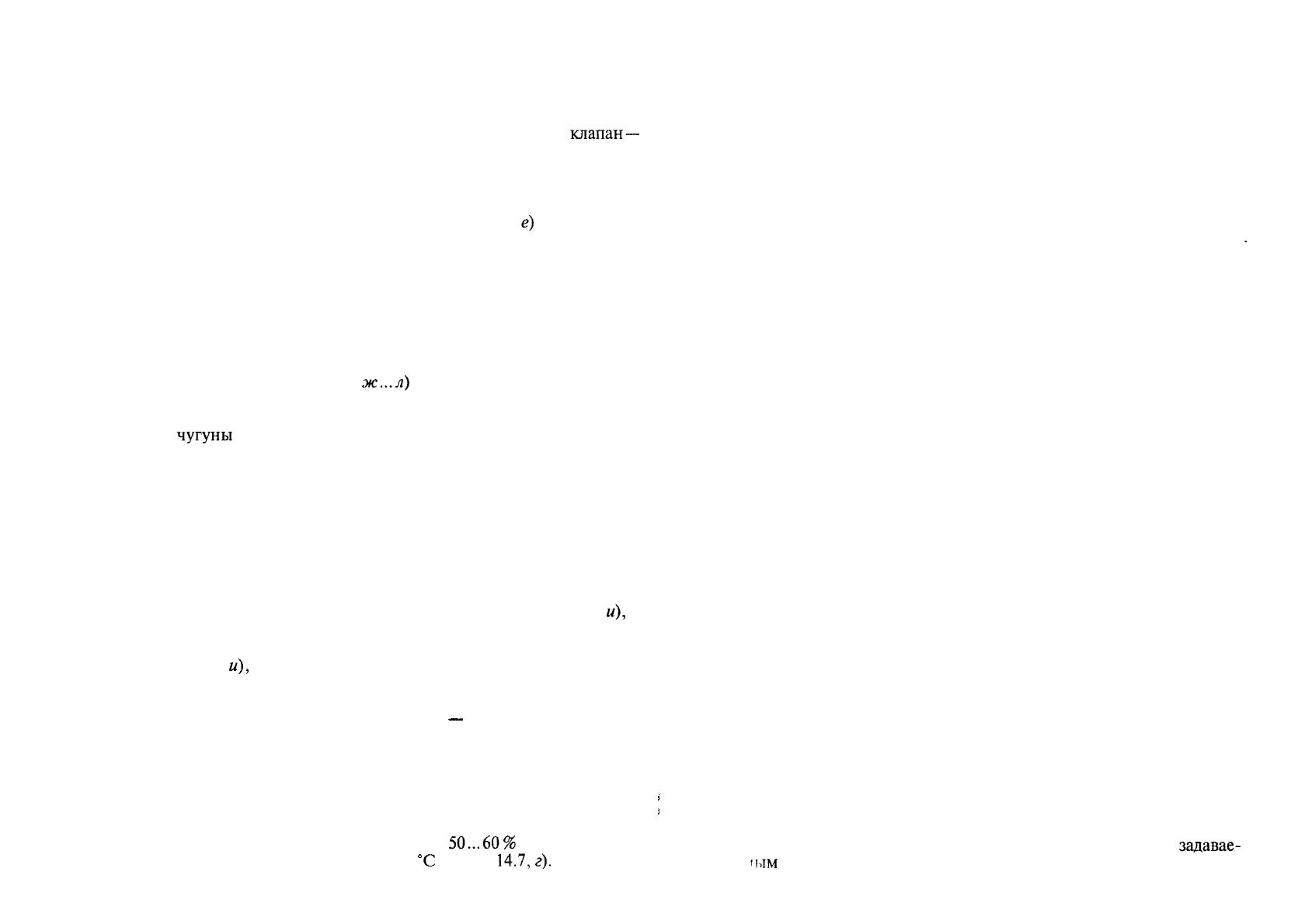
В верхней части стержня клапана для установки сухарей делают
специальные выточки: цилиндрическую с галтелями (рис. 14.7, а),
с одним или двумя поясками (рис. 14.7, в) или коническую.
Поворотный механизм клапана используется для увеличения
долговечности и надежности работы фасок в сопряжении
клапан—
седло головка клапана. Конструктивно он может быть выполнен в
виде обоймы, на которую опирается пружина, или дополнитель-
ной конической втулки. Обойма вращается за счет перекатывания
шариков в наклонных углублениях из-за изменения сил, вызыва-
ющих перемещение клапана. Втулка 4 (рис. 14.7,
е)
нижним тор-
цом опирается на днище тарелки по небольшой площади. В опре-
деленные моменты времени, когда суммарная сила, действующая
вдоль оси клапана, невелика и сила трения в плоскости контакта
мала, вибрация двигателя вызывает колебания втулки, отрывает
ее от тарелки и поворачивает вместе с клапаном.
Колпачок или манжета 5 (рис. 14.7, е), выполненные из масло-
бензостойкой резины, предотвращают попадание масла в камеру
сгорания.
Седло клапана (рис. 14.7,
ж...л)
предназначено для повыше-
ния долговечности зоны контакта клапана с головкой цилинд-
ра. Для изготовления седла применяют специальные легирован-
ные
чугуны
или жаростойкие сплавы. На рабочую поверхность
седла выпускного клапана иногда наносят слой тугоплавкого
материала.
Для получения хорошего уплотнения поясок седла шириной
около 2 мм изготовляют с переменным углом (рис. 14.7, ж). Наруж-
ная поверхность седла может иметь цилиндрическую (рис. 14.7, з)
или коническую форму (рис. 14.7, и).
Седла крепят запрессовкой с натягом и расчеканкой головки,
а стальные седла дополнительно развальцовывают в верхней части
(рис. 14.7, к). На наружной поверхности цилиндрического и кони-
ческого седел вытачивают кольцевые канавки (рис. 14.7, з,
«),
в
которые при запрессовке затекает металл головки. Коническое
седло запрессовывают в гнездо с небольшим торцевым зазором
(рис. 14.7,
«),
а цилиндрические — до упора.
Тепловой поток от рабочего тела в камере сгорания восприни-
мается головкой клапана (особенно выпускного) и передается через
фаску седлу, а через стержень клапана
—
направляющей втулке,
что обусловливает необходимость интенсивного охлаждения ука-
занных деталей. Для этого могут применяться конструктивные ре-
шения: подвод охлаждающей жидкости к наиболее нагретым зо-
нам; увеличение диаметра стержня клапана и длины его направ-
ляющей втулки; перенос теплоты от головки к стержню за счет
взбалтывания жидкого натрия в стержне клапана при его движе-
нии (полость в клапане заполняют на
50...60%
солями натрия
температура плавления которого 97
°С
— рис.
14.7,
г).
208
Для предотвращения заклинивания клапана во втулке при вы-
сокой температуре и возможном перекосе (в приводе клапана не-
посредственно кулачком вала) нижнюю внутреннюю поверхность
втулки выполняют конусной (рис. 14.7, г) или уменьшают диа-
метр стержня клапана у головки (рис. 14.7, б).
Характерные дефекты клапанного узла:
деформация и поломка клапанов в результате ударов поршня о
незакрывшийся клапан из-за обрыва ремня или цепи привода рас-
пределительного вала, заклинивания подшипника вала при недо-
статочном смазывании или превышении частоты вращения;
деформация торцовой поверхности клапанов (вогнутая фор-
ма) при перегреве двигателя;
неравномерный износ головки клапана и седла при образова-
нии нагара на поверхности фаски клапана и седла;
трещины и глубокие раковины на седле и фаске клапана из-за
недостаточного охлаждения, плохого контакта с седлом (нагара,
большого клапанного зазора), удара в момент посадки, попада-
ния посторонних предметов, веществ через систему впуска, рабо-
ты двигателя на позднем зажигании и бедной смеси;
прогар клапана из-за перегрева при образовании нагара на ра-
бочих фасках седла и клапана (резко уменьшается теплоотвод от
головки клапана), а также при малом зазоре в приводе («зависа-
нии» клапана);
износ стержня клапана и втулки из-за неравномерного расшире-
ния стержня при неровном распределении температуры клапана;
скопление нагара на направляющих втулках из-за низкого ка-
чества масла (наличия загрязняющих веществ, малой вязкости и
плохих смазочных свойств).
14.3. Профилирование кулачков
Профиль кулачка для МГР должен обеспечивать максимальную
гидродинамическую эффективность клапанной щели при прием-
лемых динамических нагрузках на элементы привода клапана.
С точки зрения получения эффективного газообмена желатель-
но иметь мгновенное открытие клапана, постоянное максималь-
ное пропускное сечение и мгновенное его закрытие. Однако это
приводит к возникновению в механической системе бесконечно
больших ускорений в начале и в конце подъема и, следовательно,
динамических нагрузок.
Высокие динамические нагрузки на элементы привода клапа-
на могут вызывать большие значения контактных напряжений в
сочленениях деталей МГР, интенсивные упругие колебания в си-
стеме механизма. Последние могут приводить к существенным
искажениям закона движения клапана по сравнению с
задавав-
1ым
профилем кулачка. В предельном случае наличие упругих ко-
209