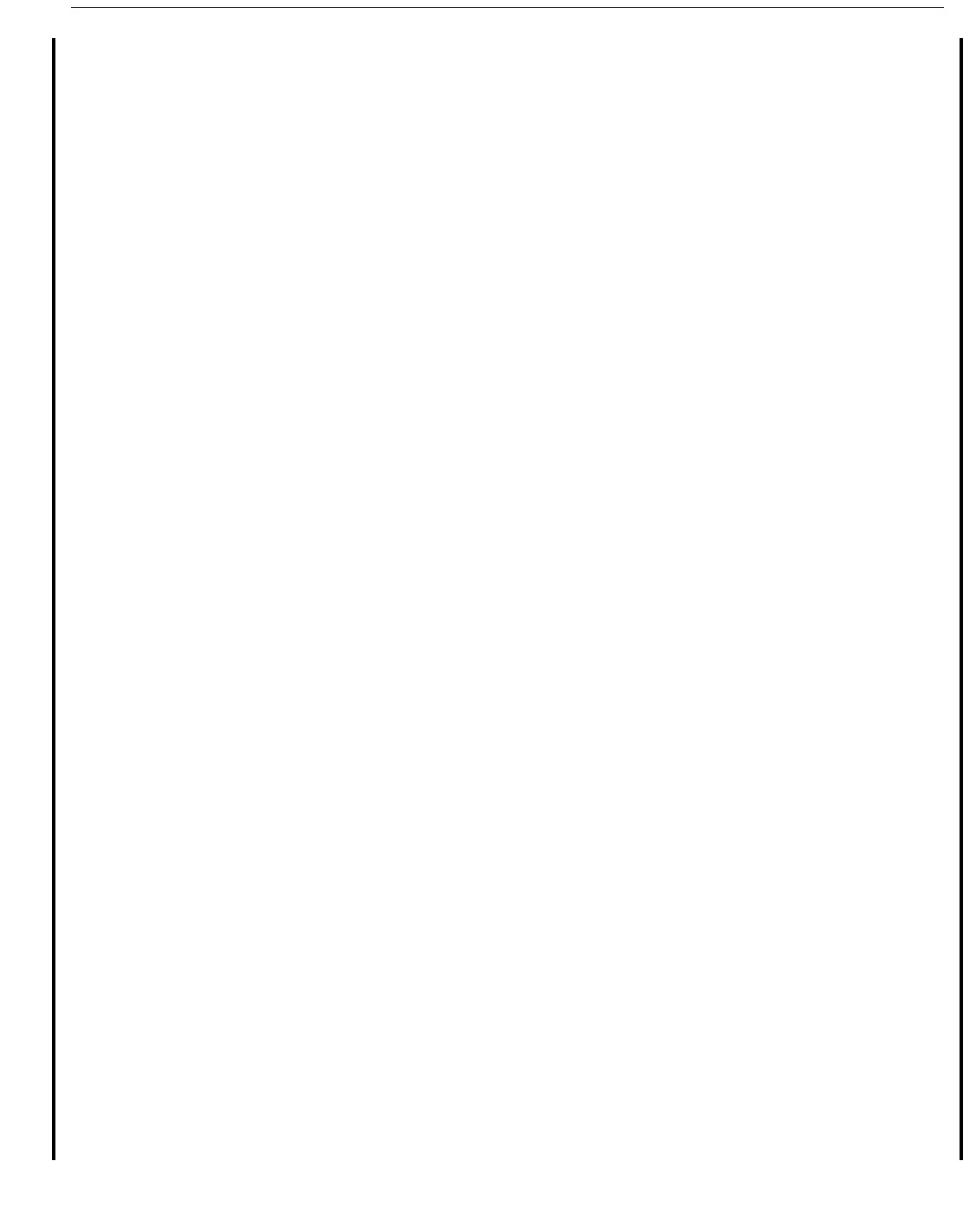
216 API RECOMMENDED PRACTICE 2A-WSD
endurances. Ref. 37 presents the results from fracture mechan-
ics evaluations, and illustrates the detrimental effect of seawa-
ter relative to air for joints with and without adequate cathodic
protection. Therefore, use of the new S-N curves given in
Table 5.5.1-1 include a penalty factor of 2 for the low cycle
end of the S-N curve (the m = 3 portion).
For joints in freely corroding conditions, or for joints with
corrosion protection levels more negative than -1100mV at the
welds, a penalty factor of 3 on N on the air m = 3 life, extended
for all endurances without a change of slope, is recommended.
Most contemporary coatings used offshore will afford an
effective barrier to ingress of seawater. Their effectiveness as
an ionic barrier to hydrogen is less certain. Unless a particular
coating is very brittle in nature, or may become subject to
hydrogen blistering during the service life of the structure, use
can be made of the in-air S-N curves.
A number of tubular joints used in deriving the basic S-N
curve had chord and braces with nearly equal diameters and
weld leg/branch thickness ratios up to 5. Some of these joints
showed extensive weld inter-run cracking in preference to
weld toe cracking. This could be significant in relation to the
application of weld improvement techniques, since clearly
improvement of the chord or brace weld toes alone may not
improve the fatigue performance of the joint. This would only
be achieved if the weld face is also ground to remove all of the
inter-run crevices. However an assessment of these joints,
using the recommended SCF equations indicate that the pre-
dicted lives are significantly above the basic S-N curve.
High strength steels are being used increasingly in the fabri-
cation of offshore structures, particularly for jack-up legs,
which are made from steels with typical yield strengths of
100–115 ksi (700–800 MPa). The effect of seawater on the
fatigue performance of these materials is thought to be more
detrimental than for medium strength structural steels because
of their greater susceptibility to hydrogen cracking under
fatigue loading in seawater. The susceptibility to hydrogen
embrittlement increases with increasing yield strength and
increasingly negative cathodic protection potential. A number
of studies have identified excessively negative cathodic pro-
tection potential as a cause of cracking due to the generation
of hydrogen, which enhances crack growth rates at the crack
tip. Evidence of hydrogen cracking found in jack-ups during
routine surveys has been reported in Ref. 38. It is therefore
important that the fatigue performance of selected high
strength steels is understood and that appropriate levels of
cathodic protection are applied.
There is insufficient data on the fatigue behavior of high
strength steel joints and the fatigue performance of higher
strength steels cannot be confidently predicted. A limited
amount of test data for plate joints with yield strengths up to
80 ksi (560 MPa) (Ref. 35) and tubular joints manufactured
from modem high strength steels with yield strengths up to
100 ksi (700 MPa) (Ref. 39) have suggested that the fatigue
performance in seawater under cathodic protection and under
free corrosion is similar to that for medium strength structural
steels. Test data or fracture mechanics analysis may be used to
determine appropriate S-N curves.
Following ISO proposals, the new API “WJ” curves are bi-
linear, with slope exponents of m = 3 and m = 5, and no endur-
ance limit. The specified chord size effect now depends on
chord thickness rather than weld or notch size. However, since
curves drawn at the reference thickness of 16mm do not give a
realistic picture of their impact on practical joint-can designs,
comparisons are made with reference to joints having t = 16
mm branch and T = 40 mm chord, as discussed below.
(a) Profiled welds – formerly Curve X. Modified profile
and size effects for this category of joints give them an effec-
tive reference thickness of √(tT) = 1 in. The resulting in-air
curve corresponds closely to the 25 mm S-N curve of ISO
14347 (Ref. 67), which comes from an IIW panel of technical
experts in tubular connections with access to the same pub-
lished database as ISO TC67/WG3.
Figure C5.5.1-1 shows a data comparison for improved
profile welds in air, including tubular joint data from Bomel
(Ref. 68), the OTJRC database (Mohr et al, Ref. 36) and large
coupon data from Rice (in Refs. 18 and 28). Run-outs are
retained here as especially useful information, although they
are typically excluded from screened data sets. Adjustment of
the test data to the 16 mm reference thickness also tests the
n
ew API adjustment for weld toe position, the new size effect
exponent, and the τ
–0.1
form of the profile effect expression.
The data trend justifies flattening of the S-N curve beyond ten
million cycles. The least conservative fit appears to be the
m = 3 part from ISO.
Figure C5.5.1-2 shows a comparison of data for improved
profile welds in seawater with cathodic protection, again
reduced to the 16mm reference. This includes data from the
following sources: Hartt API 87-24 (Ref. 33), Bignonnet PS5
and Vosikovsky TS44 (Ref. 17), Kochera OTC 2604 (in old
API Fig. C5.5-3), and Hartt (Ref. 9). This plot is most impor-
tant for calibrating the new criteria for practical design of off-
shore platforms with cathodic protection. Again, runouts are
particularly useful here.
Hartt’s butt welds are used to represent the edge condi-
tion of profile welds made according to the upgraded AWS
Figure C2.7. One might argue that these data points need to
be adjusted downward slightly to account for the fillet
radius effect as discussed for cast nodes. However, if this
were done, the butt weld tests would simply be brought into
alignment with the others, and the overall trend of the data
remains consistent with flattening the high cycle part of the
S-N curve, which is more optimistic than the extrapolation
proposed in Reference 34.
The m = 3 part of the curve remains the least conserva-
tive, even though it was derived from the proposed ISO base
case and includes the penalty factor of two. Using the air
curve here, as proposed by ISO (Draft E), would be unsafe
wherever it mattered.
Copyright American Petroleum Institute
Provided by IHS under license with API
Licensee=Indonesia location/5940240008
Not for Resale, 10/22/2008 00:07:12 MDT
--`,,```,,,`,,,,,,,,,,,,,,`,``,`-`-`,,`,,`,`,,`---