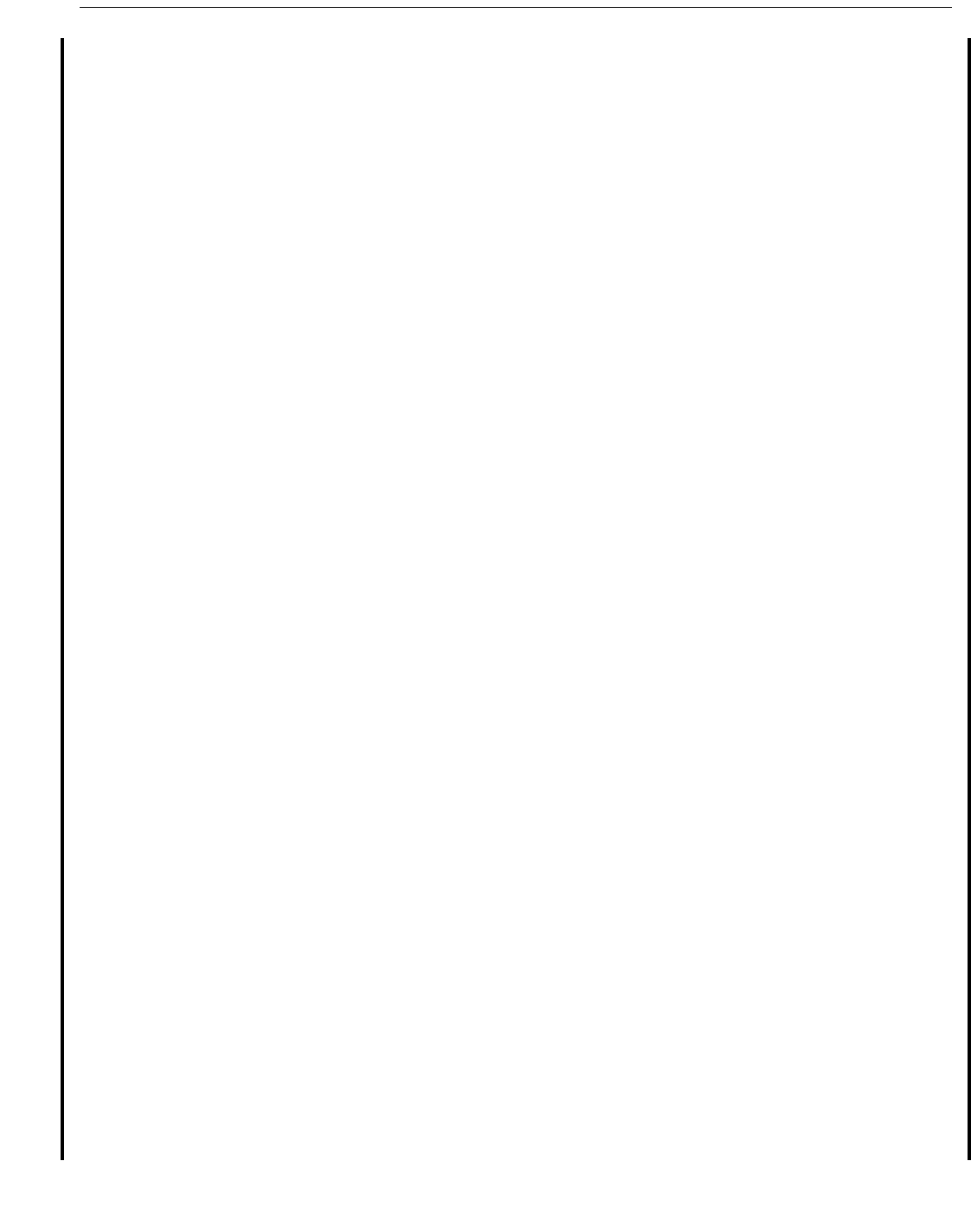
RECOMMENDED PRACTICE FOR PLANNING, DESIGNING AND CONSTRUCTING FIXED OFFSHORE PLATFORMS—WORKING STRESS DESIGN 205
how these sorts of risk should be addressed in the design
phase.
A recent study (Ref 59) has indicated that significant
increase in predicted fatigue life can be obtained by the
appropriate consideration of the local joint flexibility of tubu-
lar connections, particularly where out-of-plane bending is
important (Ref. 43). This is supported by studies of in-service
platform underwater inspection records (Ref 60) that show
that substantially less fatigue damage occurs than is predicted
using conventional rigid-joint assumptions. Where the struc-
tural analysis has been conducted on the basis of flexible joint
assumptions, consideration should be given to adjusting the
safety factors.
There are instances where the cited safety factors may be
reduced. An example could be a component above water, for
which inspection may be either easier or more frequent. A
reduction in safety factor may also be appropriate if loss of
the component does not jeopardize personnel safety or the
environment. Lesser safety factors may be justified if the
fatigue analysis algorithm has been calibrated to the structural
type and load conditions being considered, e.g., for a struc-
ture which has already demonstrated a long service life.
In selecting safety factors, inspectability and inspection
technique need careful consideration. In general, the in-ser-
vice inspection being addressed is more thorough than a gen-
eral diver or ROV survey (Level II) described in Section
14.3.2. Some complex joints, such as internally stiffened
ones, may have cracking originating from the inside (hidden)
surfaces. Hence, the possible need for inspection prior to
crack penetration through thickness should be considered at
the design stage. A trade-off may exist between introducing a
lower safety factor (assuming the component is not failure
critical) and inspecting in-service with a more complex tech-
nique such as MPI.
Although a given component may be considered readily
inspectable from exposed surfaces, inspection frequency may
still have to be balanced with the fatigue safety factor. Refer-
ences 12 and 61 (among others) discuss the relationship
between inspection interval and calculated fatigue life, as
they affect structural reliability. It is anticipated that most
tubular joints spend about half their fatigue lives in the detect-
able crack growth stage. However, in some components, such
as those with low SCFs, the period of crack growth can be a
much smaller proportion of the total life. And even with con-
ventional components, the usual inspection interval may not
be adequate if the planned service life is short.
Despite the need to address inspectability during the design
phase, there is no implied requirement in these provisions to
perform a regular, detailed inspection of each and every joint
for which a safety factor from the inspectable category is
adopted. The scope and frequency associated with the inspec-
tion plan involve considerations that extend well beyond the
issue of the fatigue analysis recipe alone. However, if no
inspection is clearly intended from the start for a particular
class of joint, then the safety factor should be selected from
the non-inspectable category. Joints in the splash zone should
normally be considered as uninspectable.
Uncertainties in fatigue life estimates can be logically eval-
uated in a probabilistic framework. A fatigue reliability
model based on the lognormal distributions is presented in
Refs. 11 and 25. This model is compatible with both the
closed form and detailed fatigue analysis methods described
above. The sources of uncertainty in fatigue life, which is
considered to be a random variable, are described explicitly.
The fatigue reliability model can be used to develop fatigue
design criteria calibrated to satisfactory historical perfor-
mance but also characterized by uniform reliability over a
range of fatigue design parameters.
C5.3 STRESS CONCENTRATION FACTORS
C5.3.1 General
The Hot Spot Stress Range (HSSR) concept places many
different structural geometries on a common basis, enabling
them to be treated using a single S-N curve. The basis of this
concept is to capture a stress (or strain) in the proximity of the
weld toes, which characterizes the fatigue life of the joint, but
excludes the very local microscopic effects like the sharp
notch, undercut and crack-like defects at the weld toe. These
local weld notch effects are included in the S-N curve. Thus
the Stress Concentration Factor (SCF) for a particular load
type and at a particular location along the intersection weld
may be defined as:
Consistency with the S-N curve is established by using a
compatible method for estimating the HSSR during the
fatigue test as used in obtaining SCFs. The Dovey 16-node
thick shell element (Ref.10) enforces a linear trend of shell
bending and membrane stress. This is consistent with the
experimental HSS extrapolation procedure, and was used to
derive Efthymiou’s SCF (Ref.48).
SCFs may be derived from finite element (FE) analyses,
model tests or empirical equations based on such methods.
When deriving SCFs using FE analysis, it is recommended to
use volume (brick and thick shell) elements to represent the
weld region and adjoining shell (as opposed to thin shell ele-
ments). In such models the SCFs may be derived by extrapo-
lating stress components to the relevant weld toes and
combining these to obtain the maximum principal stress and,
hence, the SCF. The extrapolation direction should be normal
to the weld toes.
If thin shell elements are used, the results should be inter-
preted carefully since no single method is guaranteed to pro-
vide consistently accurate stresses (Refs. 47 and 62).
Extrapolation to the mid-surface intersection generally over
SCF
HSSR at the location (excluding notch effect)
Range of the nominal brace stress
-------------------------------------------------------------------------------------------------------------=
Copyright American Petroleum Institute
Provided by IHS under license with API
Licensee=Indonesia location/5940240008
Not for Resale, 10/22/2008 00:07:12 MDT
--`,,```,,,`,,,,,,,,,,,,,,`,``,`-`-`,,`,,`,`,,`---