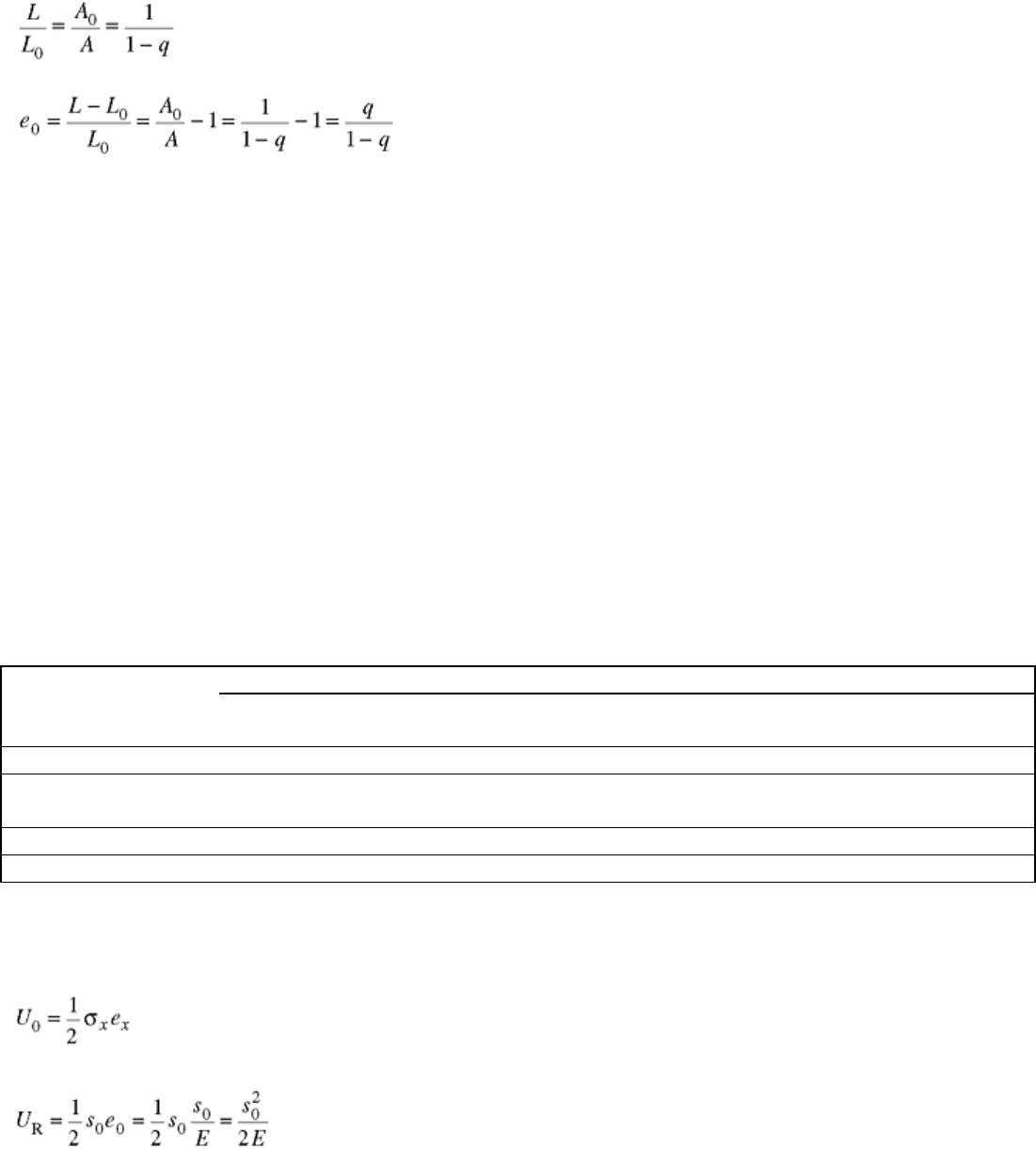
(Eq 7)
This represents the elongation based on a very short gage length near the fracture.
Another way to avoid the complications resulting from necking is to base the percentage elongation on the
uniform strain out to the point at which necking begins. The uniform elongation (e
u
), correlates well with
stretch-forming operations. Because the engineering stress-strain curve often is quite flat in the vicinity of
necking, it may be difficult to establish the strain at maximum load without ambiguity. In this case, the method
suggested in Ref 2 is useful.
Modulus of Elasticity. The slope of the initial linear portion of the stress-strain curve is the modulus of
elasticity, or Young's modulus, as shown in Fig. 3. The modulus of elasticity (E) is a measure of the stiffness of
the material. The greater the modulus, the smaller the elastic strain resulting from the application of a given
stress. Because the modulus of elasticity is needed for computing deflections of beams and other members, it is
an important design value.
The modulus of elasticity is determined by the binding forces between atoms. Because these forces cannot be
changed without changing the basic nature of the material, the modulus of elasticity is one of the most
structure-insensitive of the mechanical properties. Generally, it is only slightly affected by alloying additions,
heat treatment, or cold work (Ref 3). However, increasing the temperature decreases the modulus of elasticity.
At elevated temperatures, the modulus is often measured by a dynamic method (Ref 4). Typical values of the
modulus of elasticity for common engineering metals at different temperatures are given in Table 1.
Table 1 Typical values of modulus of elasticity at different temperature
Modulus of elasticity GPa (10
6
psi), at: Material
Room
temperature
250 °C (400
°F)
425 °C (800
°F)
540 °C (1000
°F)
650 °C (1200
°F)
Carbon steel 207 (30.0) 186 (27.0) 155 (22.5) 134 (19.5) 124 (18.0)
Austenitic stainless
steel
193 (28.0) 176 (25.5) 159 (23.0) 155 (22.5) 145 (21.0)
Titanium alloys 114 (16.5) 96.5 (14.0) 74 (10.7) 70 (10.0) …
Aluminum alloys 72 (10.5) 65.5 (9.5) 54 (7.8) … …
Resilience. The ability of a material to absorb energy when deformed elastically and to return it when unloaded
is called resilience. This property usually is measured by the modulus of resilience, which is the strain energy
per unit volume (U
0
) required to stress the material from zero stress to the yield stress (σ
0
). The strain energy
per unit volume for uniaxial tension is:
(Eq 8)
From the above definition, the modulus of resilience (U
R
) is:
(Eq 9)
This equation indicates that the ideal material for resisting energy loads in applications where the material must
not undergo permanent distortion, such as in mechanical springs, is one having a high yield stress and a low
modulus of elasticity.
For various grades of steel, the modulus of resilience ranges from 100 to 4500 kJ/m
3
(14.5–650 lbf · in./in.
3
),
with the higher values representing steels with higher carbon or alloy contents (Ref 5). The cross-hatched
regions in Fig. 5 indicate the modulus of resilience for two steels. Due to its higher yield strength, the high-
carbon spring steel has the greater resilience.