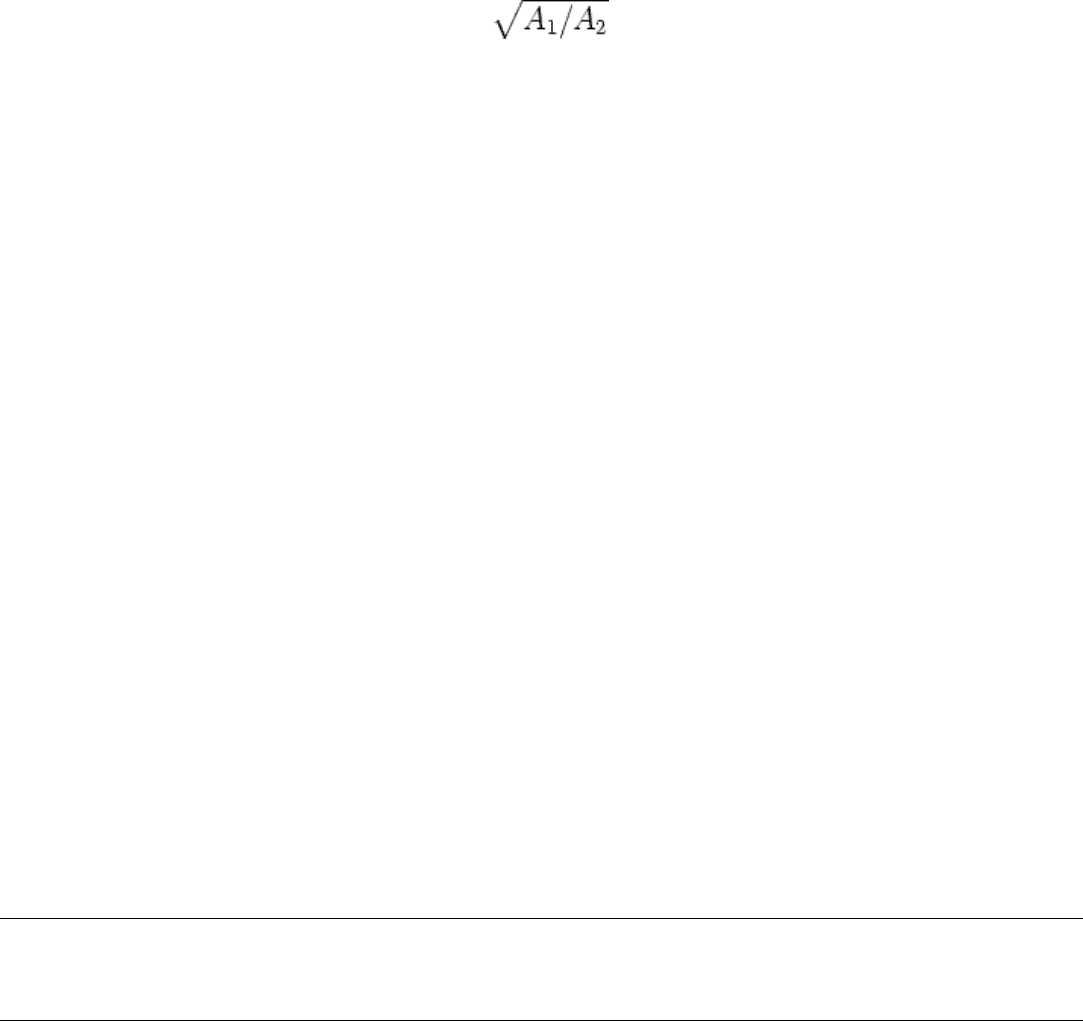
gage length of specimen 1 to conform with L
1
= L
2
. For example, suppose that a 3.2 mm (0.125 in.)
thick sheet is available, and one wishes to predict the elongation with a 50 mm (2 in.) gage length for the
identical material but in 2.0 mm (0.080 in.) thickness. Using 12.7 mm (0.5 in.) wide sheet specimens, a test
specimen with a gage length L = 50 mm (3.2 mm/2.0 mm)
1/2
= 63 mm, or 2 in. (0.125 in./0.080 in.)
1/2
= 2.5
in., made from the 3.2 mm (0.125 in.) sheet would be predicted to give the same elongation as a 50 mm (2 in.)
gage length in 2.0 mm (0.080 in.) thick sheet. Experimental verification for this procedure has been shown in
Ref 23.
The occurrence of necking in the tension test, however, makes any quantitative conversion between elongation
and reduction in area impossible. Although elongation and reduction in area usually vary in the same way—for
example, as a function of test temperature, tempering temperature, or alloy content—this is not always the case.
Generally, elongation and reduction in area measure different types of material behavior. Provided the gage
length is not too short, percent elongation is primarily influenced by uniform elongation, and thus it is
dependent on the strain-hardening capacity of the material.
Reduction in area is more a measure of the deformation required to produce fracture, and its chief contribution
results from the necking process. Because of the complicated stress state in the neck, values of reduction in area
are dependent on specimen geometry and deformation behavior, and they should not be taken as true material
properties. However, reduction in area is the most structure-sensitive ductility parameter, and as such, it is
useful in detecting quality changes in the material.
Footnote
*
Reprinted in part from Mechanical Metallurgy, 3rd ed., McGraw-Hill, New York, 1986, p 275–
permission
References cited in this section
22. M.J. Barba, Mem. Soc. Ing. Civils, Part 1, 1880, p 682
23. E.G. Kula and N.N. Fahey, Mater. Res. Stand., Vol 1, 1961, p 631
Mechanical Behavior Under Tensile and Compressive Loads*
George E. Dieter, University of Maryland
Notch Tensile Test
Ductility measurements on standard smooth tensile specimens do not always reveal metallurgical or
environmental changes that lead to reduced local ductility. The tendency for reduced ductility in the presence of
a triaxial stress field and steep stress gradients (such as occur at a notch) is called notch sensitivity. A common
way of evaluating notch sensitivity is a tension test using a notched specimen.
The notch tensile test has been used extensively for investigating the properties of high-strength steels, for
studying hydrogen embrittlement in steels and titanium, and for investigating the notch sensitivity of high-
temperature alloys. More recently, notched tension specimens have been used for fracture mechanics
measurements (see the Section “Impact Toughness Testing and Fracture Mechanics” in this Volume). Notch
sensitivity can also be investigated with the notched-impact test.
The most common notch tensile specimen uses a 60° notch with a root radius 0.025 mm (0.001 in.) or less
introduced into a round (circumferential notch) or flat (double-edge notch) tensile specimen. Usually, the depth
of the notch is such that the cross-sectional area at the root of the notch is one half of the area in the unnotched
section. The specimen is aligned carefully and loaded in tension until fracture occurs. The notch strength is