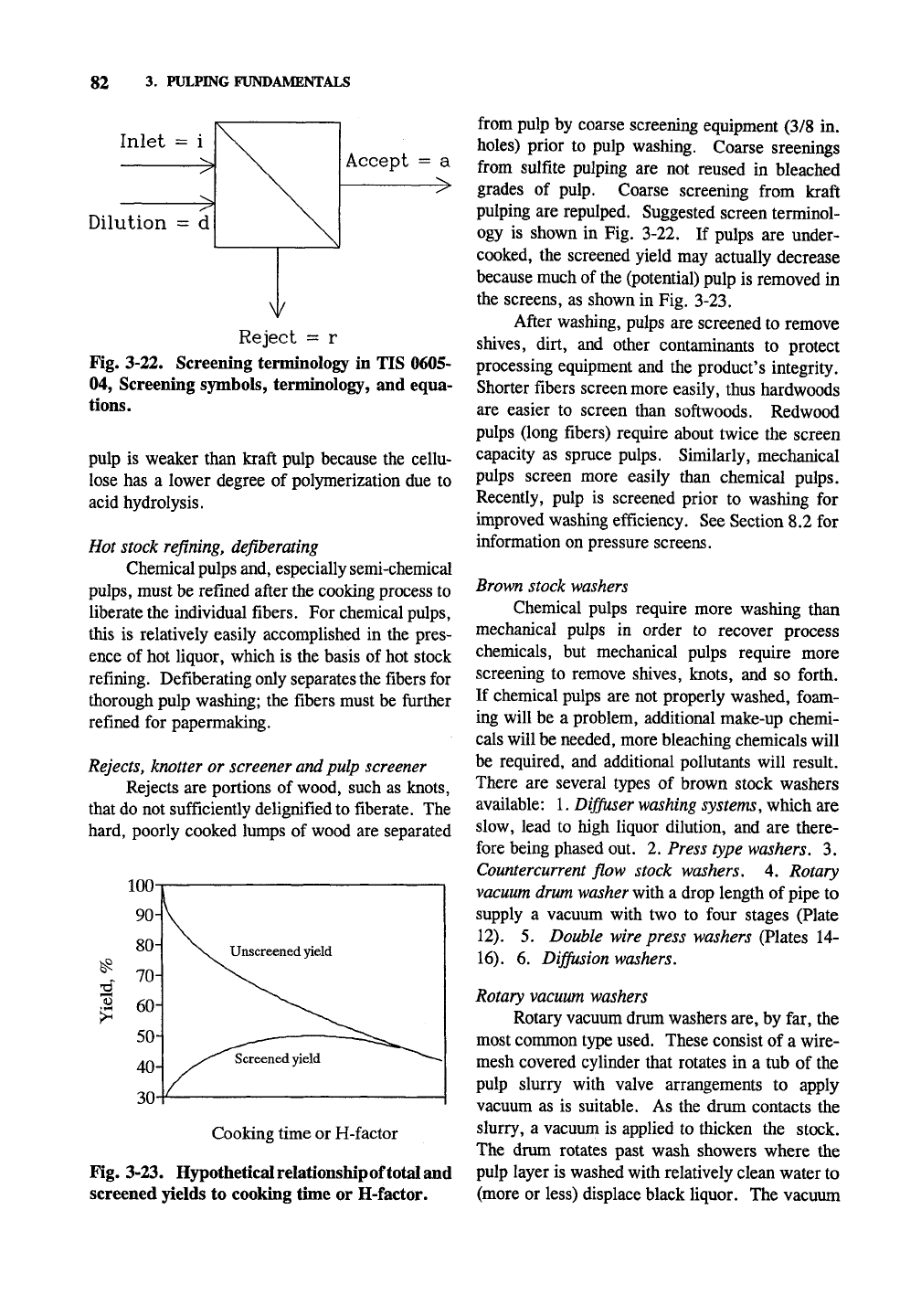
82
3.
PULPING FUNDAMENTALS
Inlet
Dilution = d
V
Reject = r
Fig. 3-22. Screening terminology in TIS 0605-
04,
Screening symbols, terminology, and equa-
tions.
pulp is weaker than kraft pulp because the cellu-
lose has a lower degree of polymerization due to
acid hydrolysis.
Hot stock refining, defiberating
Chemical pulps and, especially semi-chemical
pulps,
must be refined after the cooking process to
liberate the individual fibers. For chemical pulps,
this is relatively easily accomplished in the pres-
ence of hot liquor, which is the basis of hot stock
refining. Defiberating only separates the fibers for
thorough pulp washing; the fibers must be further
refined for papermaking.
Rejects, knotter or screener and pulp screener
Rejects are portions of wood, such as knots,
that do not sufficiently delignified to
fiber
ate. The
hard, poorly cooked lumps of wood are separated
Unscreened yield
Cooking time or H-factor
Fig. 3-23. Hypothetical relationship of total and
screened yields to cooking time or H-factor.
from pulp by coarse screening equipment (3/8 in.
holes) prior to pulp washing. Coarse sreenings
from sulfite pulping are not reused in bleached
grades of pulp. Coarse screening from kraft
pulping are repulped. Suggested screen terminol-
ogy is shown in Fig. 3-22. If pulps are under-
cooked, the screened yield may actually decrease
because much of the (potential) pulp is removed in
the screens, as shown in Fig. 3-23.
After washing, pulps are screened to remove
shives, dirt, and other contaminants to protect
processing equipment and the product's integrity.
Shorter fibers screen more easily, thus hardwoods
are easier to screen than softwoods. Redwood
pulps (long fibers) require about twice the screen
capacity as spruce pulps. Similarly, mechanical
pulps screen more easily than chemical pulps.
Recently, pulp is screened prior to washing for
improved washing efficiency. See Section 8.2 for
information on pressure screens.
Brown stock washers
Chemical pulps require more washing than
mechanical pulps in order to recover process
chemicals, but mechanical pulps require more
screening to remove shives, knots, and so forth.
If chemical pulps are not properly washed, foam-
ing will be a problem, additional make-up chemi-
cals will be needed, more bleaching chemicals will
be required, and additional pollutants will result.
There are several types of brown stock washers
available: 1. Diffuser
washing
systems, which are
slow, lead to high liquor dilution, and are there-
fore being phased out. 2. Press type washers. 3.
Countercurrent flow stock washers. 4. Rotary
vacuum drum
washer
with a drop length of pipe to
supply a vacuum with two to four stages (Plate
12).
5. Double wire press washers (Plates 14-
16).
6. Diffusion washers.
Rotary vacuum washers
Rotary vacuum drum washers are, by far, the
most common type used. These consist of a wire-
mesh covered cylinder that rotates in a tub of the
pulp slurry with valve arrangements to apply
vacuum as is suitable. As the drum contacts the
slurry, a vacuum is applied to thicken the stock.
The drum rotates past wash showers where the
pulp layer is washed with relatively clean water to
(more or less) displace black liquor. The vacuum