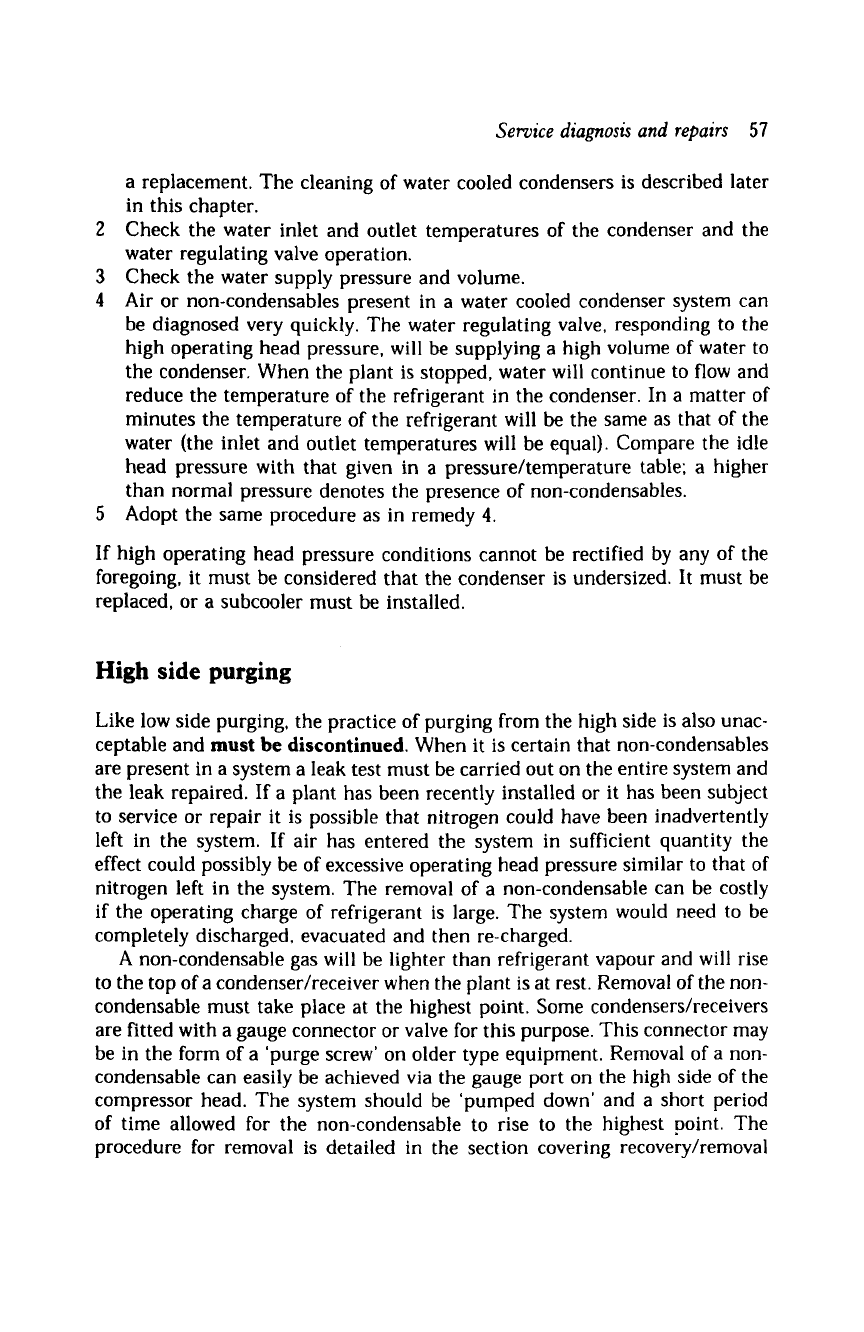
Service diagnosis and repairs
57
a replacement. The cleaning of water cooled condensers is described later
in this chapter.
2 Check the water inlet and outlet temperatures of the condenser and the
water regulating valve operation.
3 Check the water supply pressure and volume.
4 Air or non-condensables present in a water cooled condenser system can
be diagnosed very quickly. The water regulating valve, responding to the
high operating head pressure, will be supplying a high volume of water to
the condenser. When the plant is stopped, water will continue to flow and
reduce the temperature of the refrigerant in the condenser. In a matter of
minutes the temperature of the refrigerant will be the same as that of the
water (the inlet and outlet temperatures will be equal). Compare the idle
head pressure with that given in a pressure/temperature table; a higher
than normal pressure denotes the presence of non-condensables.
5 Adopt the same procedure as in remedy 4.
If high operating head pressure conditions cannot be rectified by any of the
foregoing, it must be considered that the condenser is undersized. It must be
replaced, or a subcooler must be installed.
High side purging
Like low side purging, the practice of purging from the high side is also unac-
ceptable and must be discontinued. When it is certain that non-condensables
are present in a system a leak test must be carried out on the entire system and
the leak repaired. If a plant has been recently installed or it has been subject
to service or repair it is possible that nitrogen could have been inadvertently
left in the system. If air has entered the system in sufficient quantity the
effect could possibly be of excessive operating head pressure similar to that of
nitrogen left in the system. The removal of a non-condensable can be costly
if the operating charge of refrigerant is large. The system would need to be
completely discharged, evacuated and then re-charged.
A non-condensable gas will be lighter than refrigerant vapour and will rise
to the top of a condenser/receiver when the plant is at rest. Removal of the non-
condensable must take place at the highest point. Some condensers/receivers
are fitted with a gauge connector or valve for this purpose. This connector may
be in the form of a 'purge screw' on older type equipment. Removal of a non-
condensable can easily be achieved via the gauge port on the high side of the
compressor head. The system should be 'pumped down' and a short period
of time allowed for the non-condensable to rise to the highest point. The
procedure for removal is detailed in the section covering recovery/removal