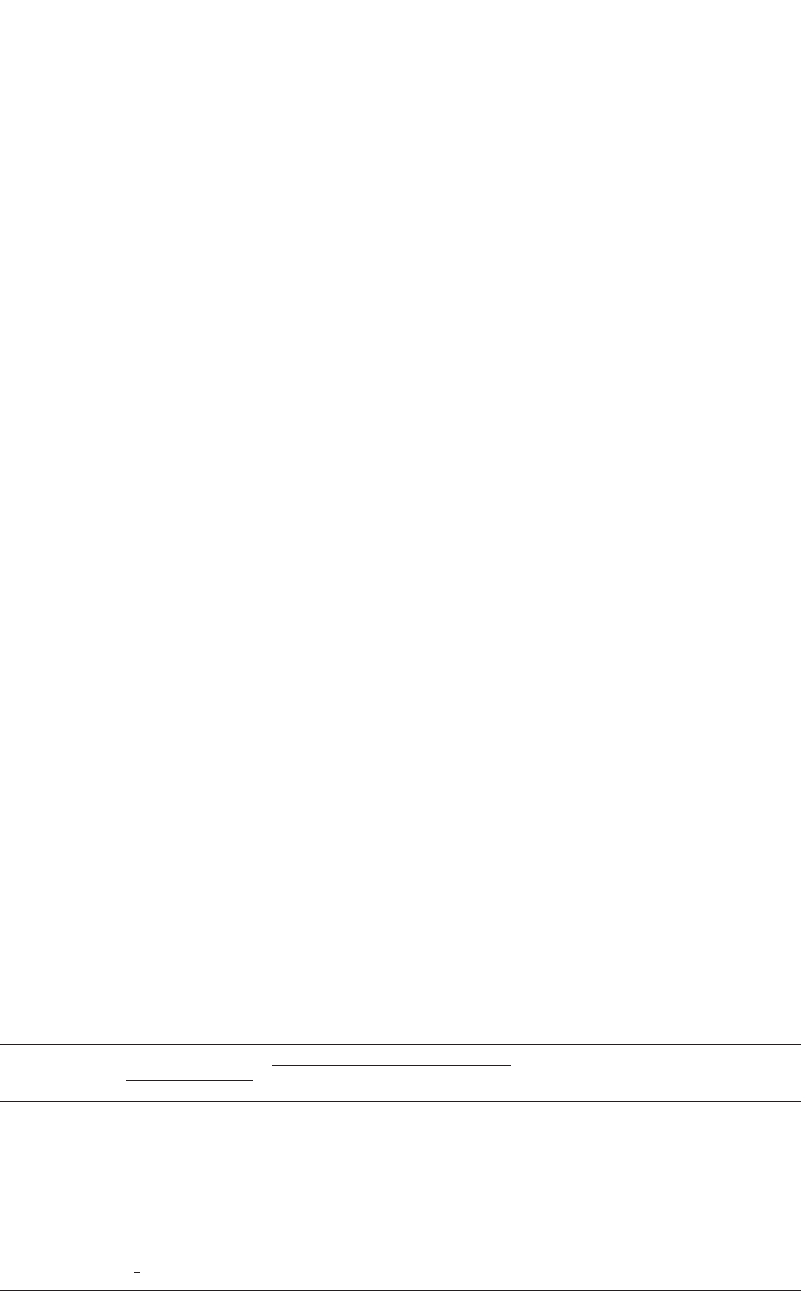
92 / Cold and Hot Forging: Fundamentals and Applications
Table 9.1 Characteristics of various methods of analysis
Input
Output
Method Flow stress Friction
Velocity
field
Stress
field
Temperature
field
Stresses
on tools Comments
Slab Average (a)(b) No Yes No Yes Ignores redundant work
Uniform energy Average (b) No No No Average Redundant work can be included approximately
Slip line Average (a)(b) Yes Yes No Yes Valid for plane-strain problems
Upper bound Distribution (b) Yes No No Average Gives upper bound on loads, can determine
free boundaries
Hill’s Distribution (a)(b) Yes No No Average Can treat 3-D problems
Finite difference Distribution (a)(b) Yes Yes Yes Yes Requires considerable computer time
Finite element Distribution (a)(b) Yes Yes Yes Yes Same as above
Matrix Distribution (a)(b) Yes Yes Yes Yes Treats rigid/plastic material
Weighted residuals Distribution (a)(b) Yes Yes Yes Yes Very general approach
(a) s ⳱ lr
n
.(b)s ⳱ . Source: [Altan et al., 1979]m¯r/3
冪
yield stress) and uses the hyperbolic properties
that the stress equations have in such cases. The
construction of slip-line fields, although produc-
ing an “exact” stress distribution, is still quite
limited in predicting results that give good cor-
relations with experimental work. From the
stress distributions, velocity fields can be cal-
culated through plasticity equations [Kobayashi
et al., 1989].
The visioplasticity method [Thomsen et al.,
1954] combines experiment and analysis. A grid
is imprinted on the metal or modeling substance
before deformation starts. Pictures taken at small
intervals during processing enable the investi-
gator to construct a flow pattern. After the ve-
locity vectors have been determined from an ac-
tual test, strain rates are calculated and the stress
distributions are obtained from plasticity equa-
tions. The method can be used to obtain reliable
solutions in detail for processes in which the ex-
perimental determination of the velocity vectors
was possible.
The upper-bound method requires the
“guessing” of admissible velocity fields (i.e.,
satisfying the boundary conditions), among
which the best one is chosen by minimizing total
potential energy. Information leading to a good
selection of velocity fields comes from experi-
mental evidence and experience. This method,
with experience, can deliver fast and relatively
accurate prediction of loads and velocity distri-
butions [Kobayashi et al., 1989].
All of the above highlighted methods of anal-
ysis fail to consider temperature gradients,
which are present in the deforming material dur-
ing hot forming operations. As a result, the ef-
fect of temperatures on flow stress and metal
flow during hot forming are often not considered
adequately.
In the finite difference method, the deriv-
atives in the governing partial differential equa-
tions are written in terms of difference equa-
tions. Therefore, for a two-dimensional domain,
a grid of cells is placed inside the domain and
the differencing approximation applied to each
interior point. This results in a system of linear
algebraic equations (with a banded solution ma-
trix), which yields a unique solution provided
the boundary conditions of the actual problem
are satisfied. Though temperature gradients can
be taken into account, this method is limited to
problems with simple boundaries [Becker,
1992].
In the finite element method, the entire so-
lution domain is divided into small finite seg-
ments (hence, the name “finite elements”). Over
each element, the behavior is described by the
differential equations. All these small elements
are assembled together, and the requirements of
continuity and equilibrium are satisfied between
neighboring elements. Provided the boundary
conditions of the actual problem are satisfied, a
unique solution can be obtained to the overall
system of linear algebraic equations (with a
sparsely populated solution matrix) [Becker,
1992].
In recent years, the finite element method has
gained wide acceptance in the industry and ac-
ademia. This can be attributed to the rapid ad-
vancement in the computing technology, user-
friendly commercial FE software and the
detailed information FEM can provide as com-
pared to other methods of analysis. The FE
method allows the user to incorporate in the
simulation: (a) the tool and workpiece tempera-
tures, (b) the heat transfer during deformation,
(c) strain-rate-dependent material properties, (d)
strain hardening characteristics, and (e) capabil-
ities for microstructure analysis. This results in
a more accurate analysis of the forging process.
Commercial FE software packages have been