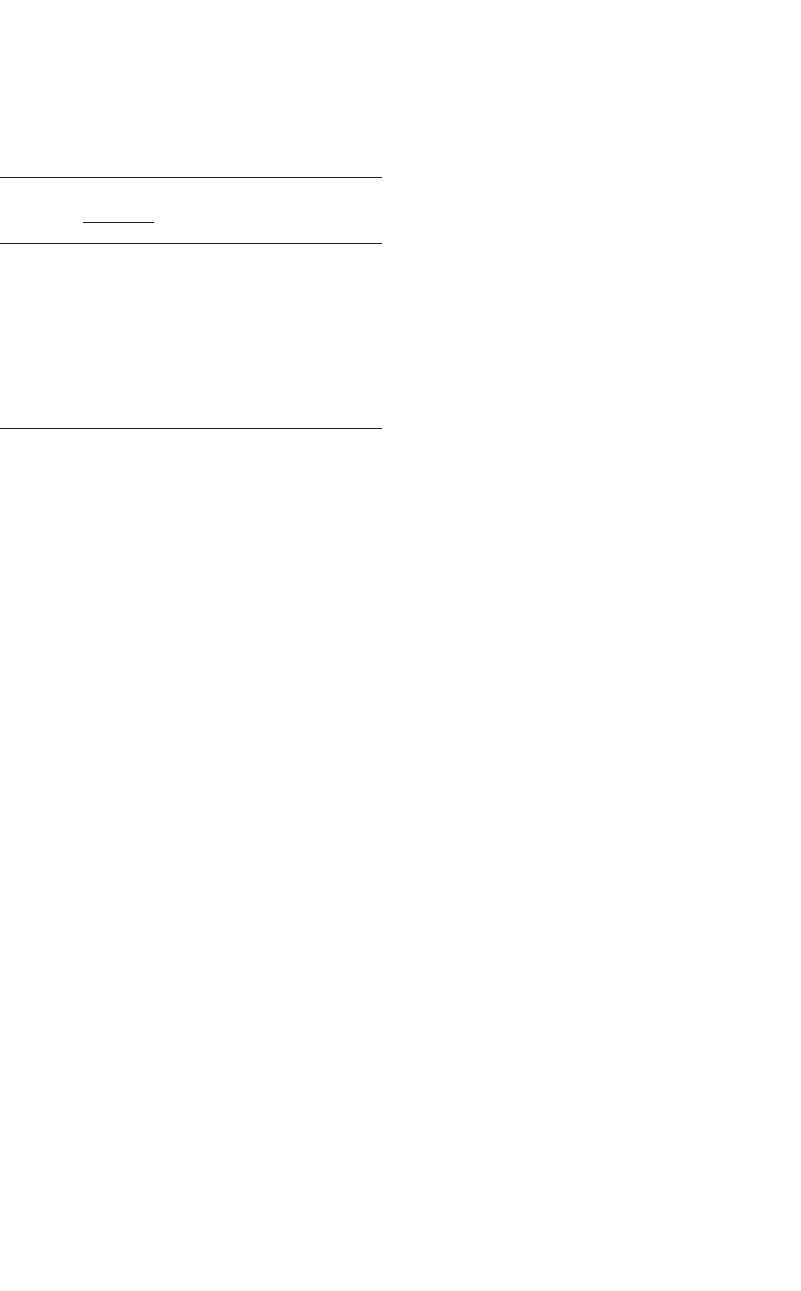
80 / Cold and Hot Forging: Fundamentals and Applications
punch diameter. Thus, the flow stress of the ma-
terial must be known and the appropriate theo-
retical curves should be used to quantify the in-
terface friction. In other words, there is no
“universal” set of calibration curves for this test.
Several double cup backward extrusion tests
have been conducted for various materials in a
160 ton hydraulic press with a ram velocity of
15 mm/s and a punch stroke of 21 mm. The re-
sults of these tests are summarized in Table 7.9.
REFERENCES
[Altan, 1970]: Altan, T., “Heat Generation and
Temperatures in Wire and Rod Drawing,”
Wire J., March 1970, p 54.
[Altan et al., 1983]: Altan, T., Oh, S., Gegel,
H., Metal Forming Fundamentals and Appli-
cations, American Society for Metals, 1983.
[Bay, 1994]: Bay, N., The State of the Art in
Cold Forging Lubrication, J. Mater. Process.
Technol., Vol 46, 1994, p 19–40.
[Bay, 1995]: Bay, N., Aspects of Lubrication in
Cold Forging of Aluminum and Steel, Pro-
ceedings of the 9th International Cold Forg-
ing Congress, Solihull, UK, May 1995, p
135–146.
[Bhushan, 2001]: Bhushan, B., Modern Tribol-
ogy Handbook—Vol 2: Materials, Coatings,
and Industrial Applications, CRC Press,
2000.
[Buschhausen et al., 1992]: Buschhausen, A.,
Lee, J.Y., Weinmann, K., Altan, T., “Evalua-
tion of Lubrication and Friction in Cold Forg-
ing Using Double Backward Extrusion Pro-
cess,” J. Mater. Process. Technol., Vol 33,
1992, p 95–108.
[Doege et al., 1996]: Doege, E., Seidel, R., Ro-
manowski, C., “Increasing Tool Life Quantity
in Die Forging: Chances and Limits of Tri-
bological Measures,” Technical Papers of the
North American Manufacturing Research In-
stitution of SME, 1996, p 89–94.
[Douglas et al., 1975]: Douglas, J.R., Altan, T.,
Flow Stress Determination for Metals at Forg-
ing Rates and Temperatures, Trans. ASME, J.
Eng. Ind., Feb 1975, p 66.
[Forcellese et al., 1994]: Forcellese, A., Ga-
brielli, F., Barcellona, A., Micari, F., “Evalu-
ation of Friction in Cold Metal Forming,” J.
Mater. Process. Technol., Vol 45, 1994, p
619–624.
[Gariety et al., 2002]: Gariety, M., Ngaile, G.,
Altan, T., “Identification of Lubricants and
Enhancement of Lubricant Performance for
Cold Heading—Progress Report 1—Identifi-
cation of Lubricants Used for Cold Heading,”
Report No. PF/ERC/NSM-02-R-32A, 2002.
[Gariety et al., 2003]: Gariety, M., Padwad, S.,
Ngaile, G., Altan, T., “Identification of Lu-
bricants and Enhancement of Lubricant Per-
formance for Cold Heading—Progress Report
2—Preliminary Lubrication Tests for Cold
Heading,” Report No. PF/ERC/NSM-02-R-
32B, 2003.
[Hannan et al., 2000]: Hannan, D., Ngaile, G.,
Altan, T., “Development of Forming Pro-
cesses for Copper Components for Stanford
Linear Accelerator,” Report No. PF/ERC/
NSM-B-00-20, 2000.
[ICFG, 1996]: International Cold Forging
Group, “Lubrication Aspects in Cold Forging
of Aluminum and Aluminum Alloys,” Doc-
ument No. 10/95, 1996.
[Lazzarotto et al., 1999]: Lazzarotto, L., Ma-
rechal, C., Dubar, L., Dubois, A., Oudin, J.,
“The Effects of Processing Bath Parameters
on the Quality and Performance of Zinc Phos-
phate Stearate Coatings,” Surf. Coat. Tech-
nol., Vol 122, 1999, p 94–100.
[Lee et al., 1972]: Lee, C.H., Altan, T., “Influ-
ence of Flow Stress and Friction Upon Metal
Flow in Upset Forging of Rings and Cylin-
ders,” Trans. ASME, J. Eng. Ind., Aug 1972,
p 775.
[Lenard, 2000]: Lenard, J., “Tribology in Metal
Rolling,” Ann. CIRP, Vol 49, 2000, p 1–24.
[Male et al., 1970]: Male, A.T., DePierre, V.,
“The Validity of Mathematical Solutions for
Determining Friction from the Ring Com-
pression Test,” Trans. ASME, J. Lubr. Tech-
nol., Vol 92, 1970, p 389.
Table 7.9 Values of frictional shear factor, m,
obtained from double cup backward extrusion
tests conducted in a hydraulic press (punch/die
temperatures ⬇ 75 ⬚F, or 24 ⬚C)
Specimen
temperatures
Frictional
shear
factor
Material ⬚F ⬚C (m) Lubrication system
AISI 8610 75 24 0.065 Zinc phosphate coating
Ⳮ soap
0.035 Metallic compounds
Ⳮ sulfur
compounds(a)
0.075 Zinc-based dry film(b)
AISI 1038 75 24 0.050 Zinc phosphate coating
Ⳮ soap
(a) Billet size ⳱ 1.25 in. diam ⳯ 1.25 in. height (31.75 mm diameter ⳯ 31.75
mm height). (b) Environmentally friendly lubrication system developed for re-
placement of zinc phosphate coating based systems. Source: [Ngaile et al., 2002]