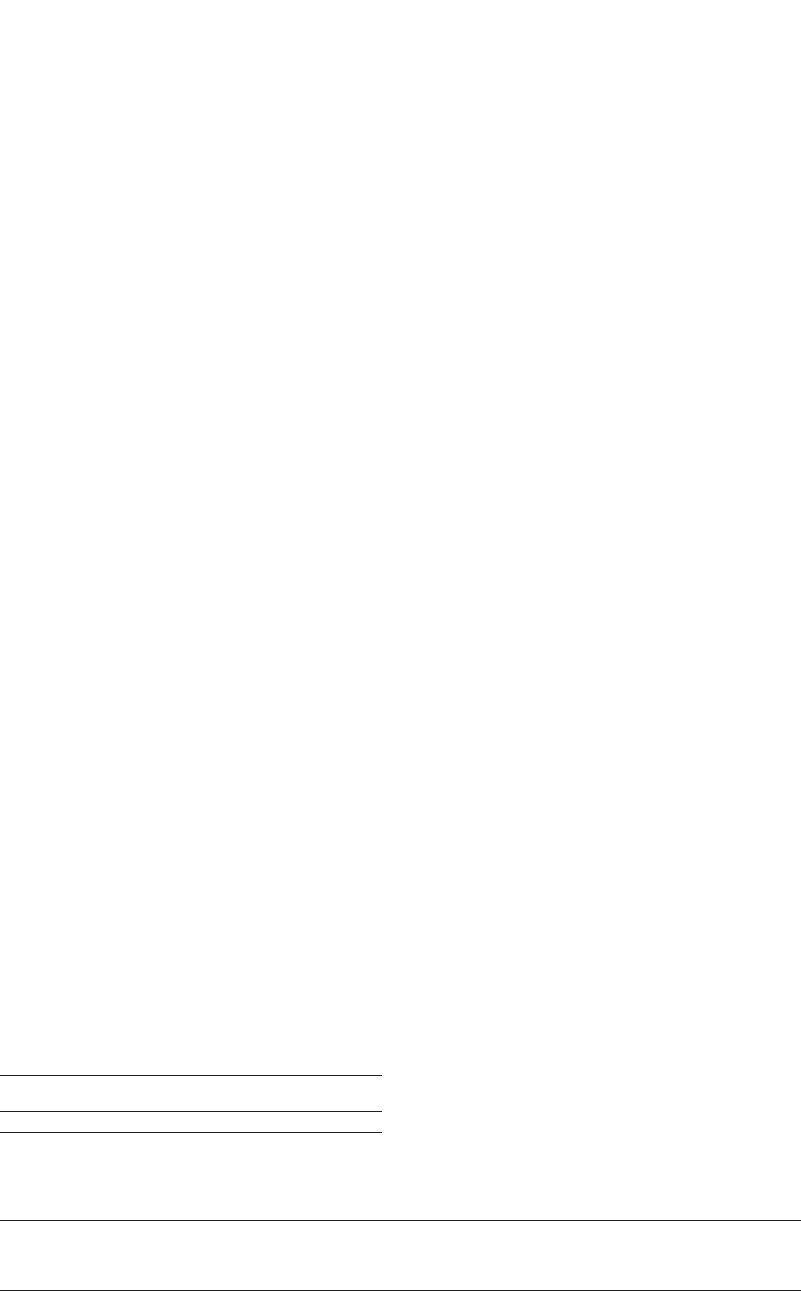
A Simplified Method to Estimate Forging Load in Impression-Die Forging / 191
and P
s
are known, L and L
s
are found. The cross
section of the simplified model is simplified, as
shown in Fig. 15.5(d). The cavity height is de-
noted by H and the radius (or half width of the
cavity) by L, the flash thickness by t and the
flash width by w. The cavity height, H, is the
average height of the actual forging and is ob-
tained by dividing the volume of the forging
without flash by its plan area.
15.4.2 Metal Flow in the Cavity
The load estimation is made for the final stage
of forging operation when the die is totally filled
and the load has its maximum value. In the im-
pression-die forging, an approximate metal flow
in the die cavity at the final forging stage de-
pends on the cavity height, the cavity width, and
flash thickness.
For a large flash thickness (cavity width to
cavity thickness ratio is greater than 2), material
is assumed to flow into the flash by shearing
along a fictitious disk having the same thickness
as the flash, as shown in Fig. 15.6(a).
If the die cavity height is small in relation to
its width, the material forms a dead metal zone
at the die corners, and the material slides along
AB and flows by internal shearing along the line
BC (Fig. 15.6b). At the surface BC, the friction
factor is then 1.
For a high cavity height to cavity width ratio,
the material forms a shear surface ABC, and a
sticking friction condition is assumed at this sur-
face (friction factor, m ⳱ 1) (Fig. 15.6c). The
shearing height, h
s
, and shearing angle, ␣, is de-
termined analytically. In the present method, the
type of metal flow in the die cavity is determined
based on the principle that material flows in a
manner that consumes a minimum amount of
plastic deformation energy. Table 15.1 shows the
equations derived for each type of metal flow to
calculate the load components.
15.5 Example of Load Estimation
The introduced load estimation method has
been programmed at the Engineering Research
Center for Net Shape Manufacturing. ForgePAL
is a computer program running on the program-
mable controller and calculates the forging load
of impression-die forging. Examples of
ForgePAL were shown in this section. A copy
of ForgePAL is included in Appendix 15.A,
given on the CD attached to this book.
15.5.1 Connecting Rod Forging
As discussed earlier in Appendix A of Chap-
ter 14, Nagpal and Altan [Nagpal et al., 1975]
calculated the forging load for the stainless steel
connecting rod. The same dimensions are used
in ForgePAL to estimate the forging load (Fig.
15.7). The other necessary forging conditions
are approximated here. Based on the geometry
transformation rule, the connecting-rod part was
simplified. The perimeter, plan area, and volume
of the forging were found by using a solid mod-
eling software, and the cavity height was cal-
culated (Table 15.2). However, this average
height may not be realistic for certain forging
parts. If the profile of the die is too complex
(changing greatly in height), simply dividing
volume by plan area may yield poor results. In
such cases, the user should experiment with re-
sults and try to guess a more realistic height in-
put.
Simplification of Forging Geometry. With
the perimeter and projected area of the connect-
ing rod, the half cavity length, L, and the depth
of the plane-strain component, L
s
, were found
as follows:
L ⳱ 0.5482 in. and L ⳱ 5.113 in.
s
Estimation of Flow Stress. Using the mate-
rial input data, such as density, specific heat, and
heat-transfer coefficient of SS 304, ForgePAL
first calculated the average forging temperature
required for estimating the flow stress value at
the end of the forging stroke. The results of the
calculations are summarized in Table 15.3.
Table 15.4 Comparison of forging load
ForgePAL
Nagpal
and Altan
Experimental
results
Total forging load, tons 340 312 320
Table 15.5 Geometry input and estimated forging load for a lead disk forging
Flash thickness, t, in. (mm) 0.004 (0.10) . . . ForgePAL Measured
Flash width, w, in. (mm) 0.2 (5.1) Flash load, ton 7 N/A
Cavity height, h
f
, in. (mm) 0.780 (19.8) Cavity load, ton 35 N/A
Half die length, L, in. (mm) 0.877 (22.3) Total load, ton 42 41