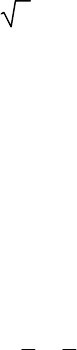
(7) The maximum permitted measurable imperfection, using the procedures of EN 1993-1-6 and
excluding measurements across lap joints, should be found as:
∆w
od
= 0,0375
rt ... (A.12)
(8) The design of the shell against buckling under axial compression above a local support, near a
bracket (e.g. to support a conveyor gantry), and near an opening should be undertaken as stipulated in
5.6.
A.3.2.3 External pressure, internal partial vacuum and wind
(1) For uniform partial internal vacuum (external pressure), where there is a structurally connected
roo
f, the critical buckling external pressure p
nRcu
for the isotropic wall should be found as:
,
0,92
n Rcru
p E
=
... (A.13)
where:
r is the radius of the silo wall;
t is the thickness of the thinnest part of the wall;
l
is the height between stiffening rings or boundaries.
(2) The design value of the maximum external pressure p
n,Ed
acting on the structure under the
combined actions of wind and partial vacuum should satisfy the condition:
p
n,Ed
≤
α
n
p
n,Rcru
/
γ
M1
... (A.14)
NOTE: The National Annex may choose the values of
α
n
and
γ
M1
. The values
α
n
= 0,5 and
γ
M1
= 1,1 are recommended.
(3) If the upper edge of the cylinder is not connected to the roof, this simple procedure should be
replaced with that of 5.3.
A.3.3 Conical welded hoppers
(1) A simple design procedure may be used provided that both the following conditions are met:
a) An enhanced partial factor is used for the hopper of
γ
M0
=
γ
M0g
;
b) No local meridional stiffeners or supports are attached to the hopper wall near the
transition junction.
NOTE: The National Annex may choose the value of
γ
M0g
. The value
γ
M0g
= 1,4 is recommended.
(2) Where the only loading under consideration is gravity and flow loading from the stored solid,
the meridional force per unit circumference n
φh,Ed,s
caused by the symmetrical pressures defined in
EN 1991-4 that must be transmitted through the transition joint should be evaluated using global
equilibrium, see Figure A.1. The design value of the local meridional force per unit circumference
n
φh,Ed
, allowing for the possible non-uniformity of the loading, should then be obtained as
n
φh,Ed
= g
asym
n
φh,Ed,s
… (
A.15)