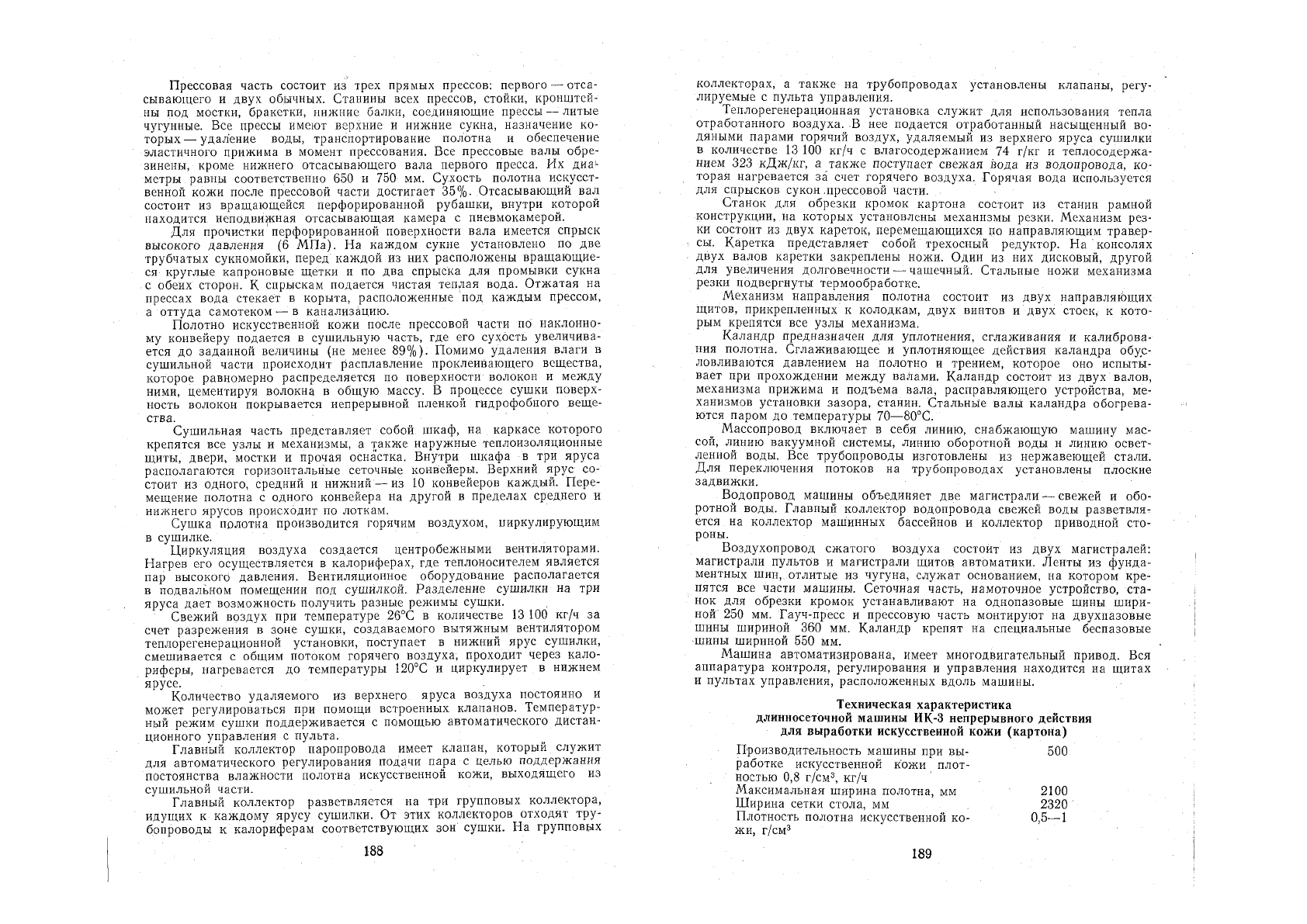
Прессовая часть состоит из трех прямых прессов: первого — отса-
сывающего и двух обычных. Станины всех прессов, стойки, кронштей-
ны под мостки, бракетки, нижние балки, соединяющие прессы — литые
чугунные. Все прессы имеют верхние и нижние сукна, назначение ко-
торых— удаление воды, транспортирование полотна и обеспечение
эластичного прижима в момент прессования. Все прессовые валы обре-
зинены, кроме нижнего отсасывающего вала первого пресса. Их диа^
метры равны соответственно 650 и 750 мм. Сухость полотна искусст-
венной кожи после прессовой части достигает 35%- Отсасывающий вал
состоит из вращающейся перфорированной рубашки, внутри которой
находится неподвижная отсасывающая камера с пневмокамерой.
Для прочистки перфорированной поверхности вала имеется спрыск
высокого давления (6 МПа). На каждом сукне установлено по две
трубчатых сукномойки, перед каждой из них расположены вращающие-
ся круглые капроновые щетки и по два спрыска для промывки сукна
с обеих сторон. К спрыскам подается чистая теплая вода. Отжатая на
прессах вода стекает в корыта, расположенные под каждым прессом,
а оттуда самотеком — в канализацию.
Полотно искусственной кожи после прессовой части по наклонно-
му конвейеру подается в сушильную часть, где его сухость увеличива-
ется до заданной величины (не менее 89%). Помимо удаления влаги в
сушильной части происходит расплавление проклеивающего вещества,
которое равномерно распределяется по поверхности волокон и между
ними, цементируя волокна в общую массу. В процессе сушки поверх-
ность волокон покрывается непрерывной пленкой гидрофобного веще-
ства.
Сушильная часть представляет собой шкаф, на каркасе которого
крепятся все узлы и механизмы, а также наружные теплоизоляционные
щиты, двери, мостки и прочая оснастка. Внутри шкафа в три яруса
располагаются горизонтальные сеточные конвейеры. Верхний ярус со-
стоит из одного, средний и нижний — из 10 конвейеров каждый. Пере-
мещение полотна с одного конвейера на другой в пределах среднего и
нижнего ярусов происходит по лоткам.
Сушка полотна производится горячим воздухом, циркулирующим
в сушилке.
Циркуляция воздуха создается центробежными вентиляторами.
Нагрев его осуществляется в калориферах, где теплоносителем является
пар высокого давления. Вентиляционное оборудование располагается
в подвальном помещении под сушилкой. Разделение сушилки на три
яруса дает возможность получить разные режимы сушки.
Свежий воздух при температуре 26°С в количестве 13 100 кг/ч за
счет разрежения в зоне сушки, создаваемого вытяжным вентилятором
теплорегенерационной установки, поступает в нижний ярус сушилки,
смешивается с общим потоком горячего воздуха, проходит через кало-
риферы, нагревается до температуры 120°С и циркулирует в нижнем
ярусе.
Количество удаляемого из верхнего яруса воздуха постоянно и
может регулироваться при помощи встроенных клапанов. Температур-
ный режим сушки поддерживается с помощью автоматического дистан-
ционного управления с пульта.
Главный коллектор паропровода имеет клапан, который служит
для автоматического регулирования подачи пара с целью поддержания
постоянства влажности полотна искусственной кожи, выходящего из
сушильной части.
Главный коллектор разветвляется на три групповых коллектора,
идущих к каждому ярусу сушилки. От этих коллекторов отходят тру-
бопроводы к калориферам соответствующих зон сушки. На групповых
188
коллекторах, а также на трубопроводах установлены клапаны, регу-
лируемые с пульта управления.
Теплорегенерационная установка служит для использования тепла
отработанного воздуха. В нее подается отработанный насыщенный во-
дяными парами горячий воздух, удаляемый из верхнего яруса сушилки
в количестве 13 100 кг/ч с влагосодержанием 74 г/кг и теплосодержа-
нием 323 кДж/кг, а также поступает свежая вода из водопровода, ко-
торая нагревается за счет горячего воздуха. Горячая вода используется
для спрысков сукон .прессовой части.
Станок для обрезки кромок картона состоит из станин рамной
конструкции, на которых установлены механизмы резки. Механизм рез-
ки состоит из двух кареток, перемещающихся по направляющим травер-
сы. Каретка представляет собой трехосный редуктор. На консолях
двух валов каретки закреплены ножи. Один из них дисковый, другой
для увеличения долговечности — чашечный. Стальные ножи механизма
резки подвергнуты термообработке.
Механизм направления полотна состоит из двух направляющих
щитов, прикрепленных к колодкам, двух винтов и двух стоек, к кото-
рым крепятся все узлы механизма.
Каландр предназначен для уплотнения, сглаживания и калиброва-
ния полотна. Сглаживающее и уплотняющее действия каландра обус-
ловливаются давлением на полотно и трением, которое оно испыты-
вает при прохождении между валами. Каландр состоит из двух валов,
механизма прижима и подъема вала, расправляющего устройства, ме-
ханизмов установки зазора, станин. Стальные валы каландра обогрева-
ются паром до температуры 70—80°С.
Массопровод включает в себя линию, снабжающую машину мас-
сой, линию вакуумной системы, линию оборотной воды и линию освет-
ленной воды. Все трубопроводы изготовлены из нержавеющей стали.
Для переключения потоков на трубопроводах установлены плоские
задвижки.
Водопровод машины объединяет две магистрали — свежей и обо-
ротной воды. Главный коллектор водопровода свежей воды разветвля-
ется на коллектор машинных бассейнов и коллектор приводной сто-
роны.
Воздухопровод сжатого воздуха состоит из двух магистралей:
магистрали пультов и магистрали щитов автоматики. Ленты из фунда-
ментных шин, отлитые из чугуна, служат основанием, на котором кре-
пятся все части машины. Сеточная часть, намоточное устройство, ста-
нок для обрезки кромок устанавливают на однопазовые шины шири-
ной 250 мм. Гауч-пресс и прессовую часть монтируют на двухпазовые
шины шириной 360 мм. Каландр крепят на специальные беспазовые
-шины шириной 550 мм.
Машина автоматизирована, имеет многодвигательный привод. Вся
аппаратура контроля, регулирования и управления находится на щитах
и пультах управления, расположенных вдоль машины.
Техническая характеристика
длинносеточной машины ИК-3 непрерывного действия
для выработки искусственной кожи (картона)
Производительность машины при вы- 500
работке искусственной кожи плот-
ностью 0,8 г/см
3
, кг/ч
Максимальная ширина полотна, мм 2100
Ширина сетки стола, мм , 2320
Плотность полотна искусственной ко- 0,5—1
жи, г/см
3
189