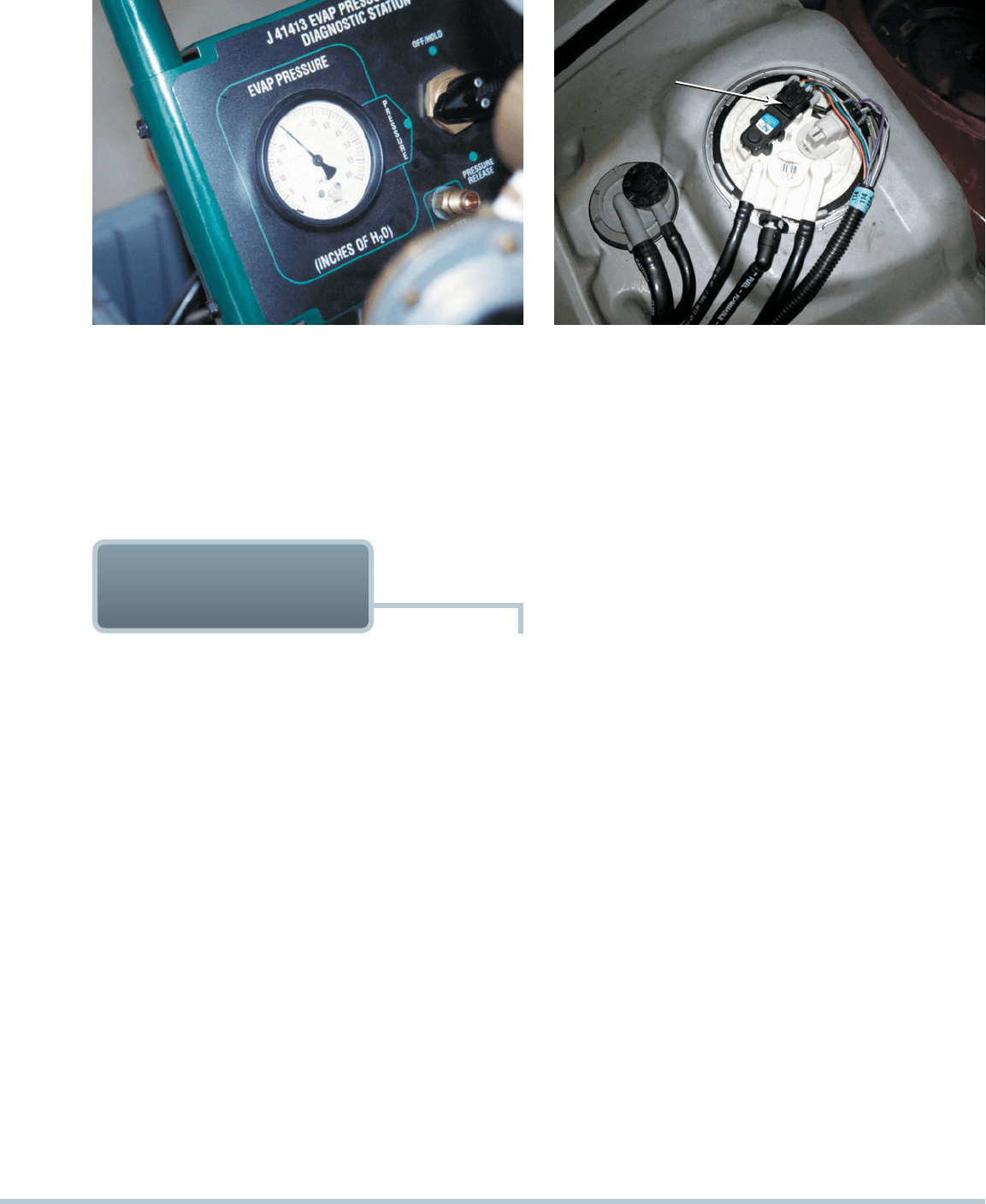
EVAPORATIVE EMISSION CONTROL SYSTEMS 323
Nitrogen gas pressurization. This method uses nitrogen
gas under a very low pressure (lower than 1 PSI) in the
fuel system. The service technician then listens for the
escaping air, using amplified headphones.
SEE
FIGURE 25–11 .
FIGURE 25–11 An emission tester that uses nitrogen to
pressurize the fuel system.
FUEL TANK
PRESSURE
(FTP) SENSOR
FIGURE 25–12 The fuel tank pressure sensor (black unit with
three wires) looks like a MAP sensor and is usually located on
top of the fuel pump module (white unit).
EVAPORATIVE
SYSTEM MONITOR
OBD-II REQUIREMENTS OBD-II computer programs not
only detect faults but also periodically test various systems
and alert the driver before emissions-related components are
harmed by system faults:
Serious faults cause a blinking malfunction indicator lamp
(MIL) or even an engine shutdown.
Less serious faults may simply store a code but not illu-
minate the MIL.
The OBD-II requirements did not affect fuel system design.
However, one new component, a fuel evaporative canister purge
line pressure sensor, was added for monitoring purge line pres-
sure during tests. The OBD-II requirements state that vehicle fuel
systems are to be routinely tested while under way by the PCM.
All OBD-II vehicles perform a canister purge system pres-
sure test, as commanded by the PCM. While the vehicle is being
driven, the vapor line between the canister and the purge valve
is monitored for pressure changes:
When the canister purge solenoid is open, the line should
be under a vacuum since vapors must be drawn from the
canister into the intake system. However, when the purge
solenoid is closed, there should be no vacuum in the line.
The pressure sensor detects if a vacuum is present, and
the information is compared to the command given to the
solenoid.
If, during the canister purge cycle, no vacuum exists in
the canister purge line, a code is set indicating a possible
fault, which could be caused by an inoperative or clogged
solenoid or a blocked or leaking canister purge fuel line.
Likewise, if vacuum exists when no command for purge is
given, a stuck solenoid is evident, and a code is set. The
EVAP system monitor tests for purge volume and leaks.
A typical EVAP monitor first closes off the system to at-
mospheric pressure and opens the purge valve during cruise
operation. A fuel tank pressure (FTP) sensor then monitors
the rate with which vacuum increases in the system. The moni-
tor uses this information to determine the purge volume flow
rate. To test for leaks, the EVAP monitor closes the purge valve,
creating a completely closed system. The fuel tank pressure
sensor then monitors the leak-down rate. If the rate exceeds
PCM-stored values, a leak greater than or equal to the OBD-II
standard of 0.04 inch (1 mm) or 0.02 inch (0.5 mm) exists. After
two consecutive failed trips testing either purge volume or the
presence of a leak, the PCM lights the MIL and sets a DTC.
The fuel tank pressure sensor is similar to a MAP sensor,
and instead of monitoring intake manifold absolute pressure, it
is used to monitor fuel tank pressure.
SEE FIGURE 25–12 .
ENGINE-OFF NATURAL VACUUM System integrity
(leakage) can also be checked after the engine is shut off.
The premise is that a warm evaporative system will cool
down after the engine is shut off and the vehicle is stable.
A slight vacuum will be created in the gas tank during this
cool-down period. If a specific level of vacuum is reached
and maintained, the system is said to have integrity (no
leakage). Actually, the vacuum is created after a period of
time because the vapor pressure tends to increase after the
engine is shut off and gradually decreases over time. The
PCM monitors the pressure rise and decrease over time and
triggers a diagnostic trouble code (DTC) if the pressure indi-
cates a leak in the system.
SEE FIGURE 25–13 .