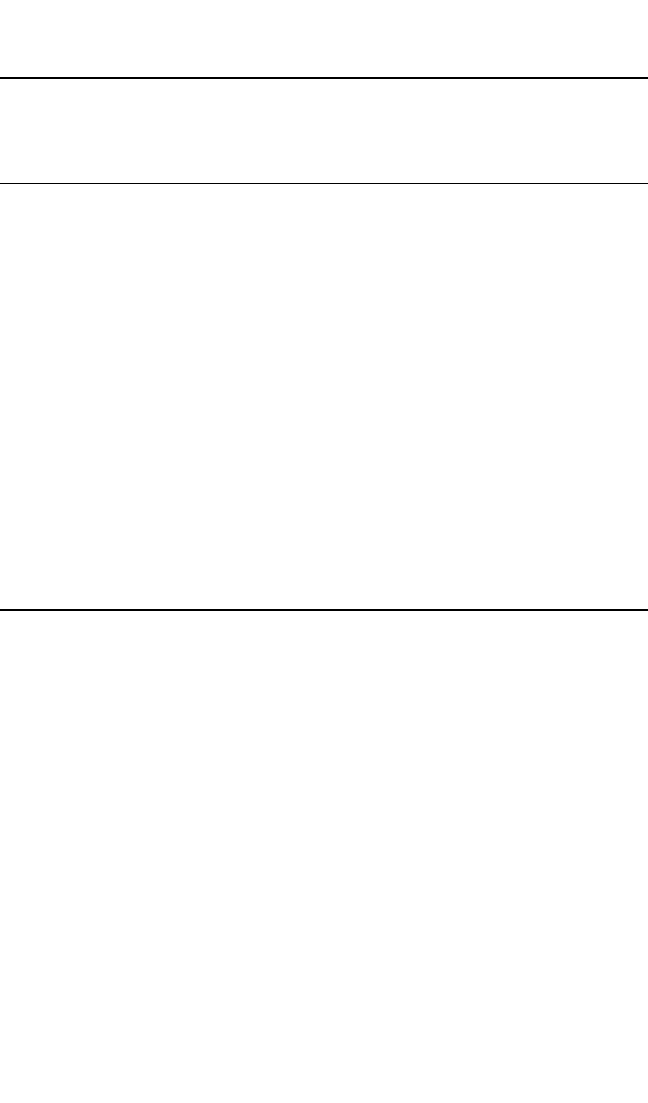
a fatigue-strength reduction factor. Parameters characteristic of the specific compo-
nent which make it more susceptible to fatigue failure than the unnotched specimen
are reflected in the strength-reduction factor. Early applications of this method were
based on the results of rotating bending tests. The application of such tests, in which
mirror-polished specimens were subjected to reversed bending, requires considera-
tion of a number of factors which present themselves in design situations. Among
these factors are size, type of loading, surface finish, surface treatments, temperature,
and environment.
In the rotating beam test, a relatively small volume of material is subjected to the
maximum stress. For larger rotating beam specimens, the volume of material is
greater, and therefore there will be a greater probability of initiating a fatigue crack.
Similarly, an axially loaded specimen which has no gradient will exhibit an
endurance limit smaller than that obtained from the rotating beam test. Surface fin-
ish will have a similar effect. Surface finish is more significant for higher-strength
steels. At shorter lives (high stress levels), surface finish has a smaller effect on the
fatigue life. Surface treatment, temperature, and environment have similar effects.
The effect of mean stress on fatigue life is conveniently represented in the form
of a modified Goodman fatigue diagram (Fig. 34.6). In this figure, the ordinate is the
maximum stress, and the abscissa is the minimum stress. Radial lines indicate the
stress ratio. The curves n
1
, n
2
, etc., represent failure at various lives.
Many design specifications
12–15
contain provisions for repeated loadings based
on laboratory tests. In these specifications, fabricated details are categorized for
ENGINEERING PROPERTIES OF METALS 34.11
TABLE 34.5 Tensile and Fatigue Properties of Steels (J. M. Lessells.
8
)
Endur-
Yield Tensile ance
strength, strength, Reduc- limit,
lb/in.
2
, lb/in.
2
, Elonga- tion of lb/in.
2
, Ratio
Material State σ
y
σ
u
tion, % area, % σ
e
σ
e
/σ
u
0.02% C As received 19,000 42,400 48.3 76.2 26,000 0.61
Wrought iron As received 29,600 47,000 35.0 29.0 23,000 0.49
0.24% C As received 38,000 60,500 39.0 64.0 25,600 0.425
0.24% C Water-quenched 45,600 67,000 38.0 71.0 30,200 0.45
and drawn
0.37% C Normalized 34,900 71,900 29.4 53.5 33,000 0.46
0.37% C Water-quenched 63,100 94,200 25.0 63.0 45,000 0.476
and drawn
0.52% C Normalized 47,600 98,000 24.4 41.7 42,000 0.43
0.52% C Water-quenched 84,300 111,400 21.9 56.6 55,000 0.48
and drawn
0.93% C Normalized 33,400 84,100 24.8 37.2 30,500 0.36
0.93% C Oil-quenched 67,600 115,000 23.0 39.6 56,000 0.487
and drawn
1.2% C Normalized 60,700 116,900 7.9 11.6 50,000 0.43
1.2% C Oil-quenched 130,000 180,000 9.0 15.2 92,000 0.51
and drawn
0.31% C, 3.35% Ni Normalized 53,500 104,000 23.0 45.0 49,500 0.47
0.31% C, 3.35% Ni Oil-quenched 130,000 154,000 17.0 49.0 63,500 0.41
and drawn
0.24% C, 3.3% Ni, Oil-quenched 128,000 138,000 18.2 61.8 68,000 0.49
0.87% Cr and drawn
8434_Harris_34_b.qxd 09/20/2001 12:30 PM Page 34.11