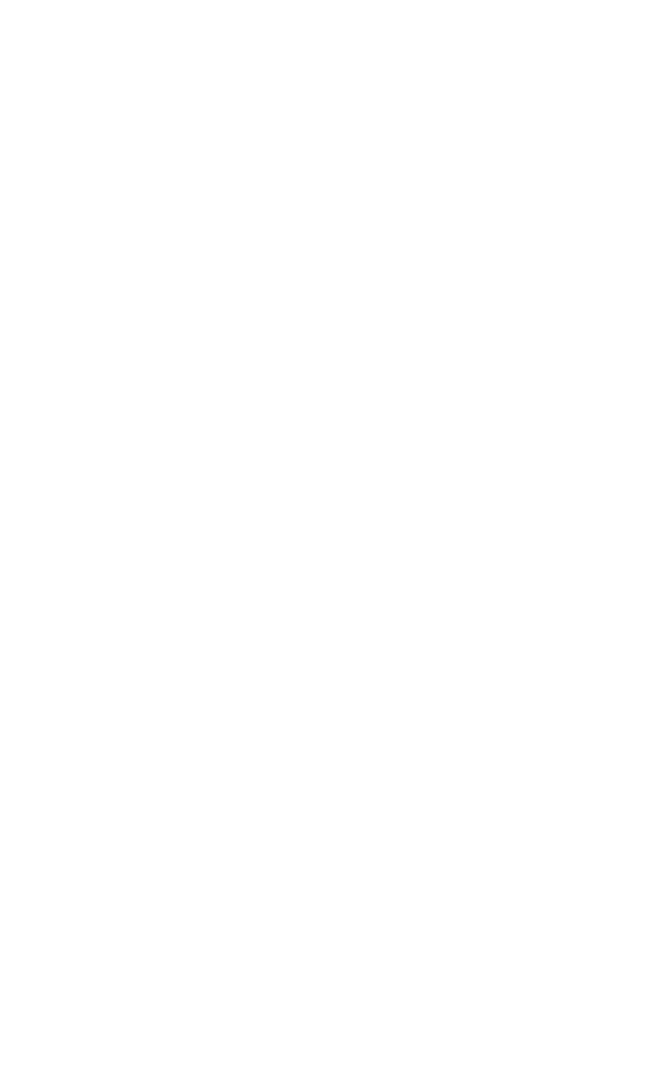
where m is the mass of the rotor, is the eccentricity or radial distance of the center-
of-gravity from the axis of rotation, and ω is the rotational speed in radians per sec-
ond. Since the rotor is assumed to be rigid and thus not capable of distortion, this
force is balanced by two reaction forces. There is one force at each bearing. Their
algebraic sum is equal in magnitude and opposite in sense. The relative magnitudes
of the two forces depend, in part, upon the axial position of each bearing with
respect to the center-of-gravity of the rotor. In simplified form, this illustrates the
“balancing problem.” One must choose a practical method of constructing a per-
fectly balanced rotor from this unbalanced rotor.
The center-of-gravity may be moved to the shaft axis (or as close to this axis as is
practical) in one of two ways.The journals may be modified so that the shaft axis and
an axis through the center-of-gravity are moved to essential coincidence. From the-
oretical considerations, this is a valid method of minimizing unbalance caused by the
displacement of the center-of-gravity from the shaft axis, but for practical reasons it
is difficult to accomplish. Instead, it is easier to achieve a radial shift of the center-of-
gravity by adding mass to or subtracting it from the mass of the rotor; this change in
mass takes place in the longitudinal plane which includes the shaft axis and the cen-
ter-of-gravity. From Eq. (39.1), it follows that there can be no net radial force acting
on the rotor at any speed of rotation if
m′r = m (39.2)
where m′ is the mass added to or subtracted from that of the rotor and r is the radial
distance to m′. There may be a couple, but there is no net force. Correspondingly,
there can be no net bearing reaction. Any residual reactions sensed at the bearings
would be due solely to the couple acting on the rotor.
If this rotor-bearing assembly were supported on a scale having a sufficiently
rapid response to sense the change in force at the speed of rotation of the rotor, no
fluctuations in the magnitude of the force would be observed. The scale would reg-
ister only the dead weight of the rotor-bearing assembly.
This process of effecting essential coincidence between the center-of-gravity of the
rotor and the shaft axis is called “single-plane (static) balancing.” The latter name for
the process is more descriptive of the end result than of the procedure that is followed.
If a rotor which is supported on two bearings has been balanced statically, the
rotor will not rotate under the influence of gravity alone. It can be rotated to any
position and, if left there, will remain in that position. However, if the rotor has not
been balanced statically, then from any position in which the rotor is initially placed,
it will tend to turn to that position in which the center-of-gravity is lowest.
As indicated below, single-plane balancing can be accomplished most simply (but
not necessarily with great accuracy) by supporting the rotor on flat, horizontal ways
and allowing the center-of-gravity to seek its lowest position. It also can be accom-
plished in a centrifugal balancing machine by sensing and correcting for the unbal-
ance force characterized by Eq. (39.1).
RIGID-ROTOR BALANCING—DYNAMIC UNBALANCE
When a rotor is balanced statically, the shaft axis and principal inertia axis may not
coincide; single-plane balancing ensures that the axes have only one common point,
namely, the center-of-gravity.Thus, perfect balance is not achieved. To obtain perfect
balance, the principal axis must be rotated about the center-of-gravity in the longi-
tudinal plane characterized by the shaft axis and the principal axis. This rotation can
BALANCING OF ROTATING MACHINERY 39.3
8434_Harris_39_b.qxd 09/20/2001 12:24 PM Page 39.3