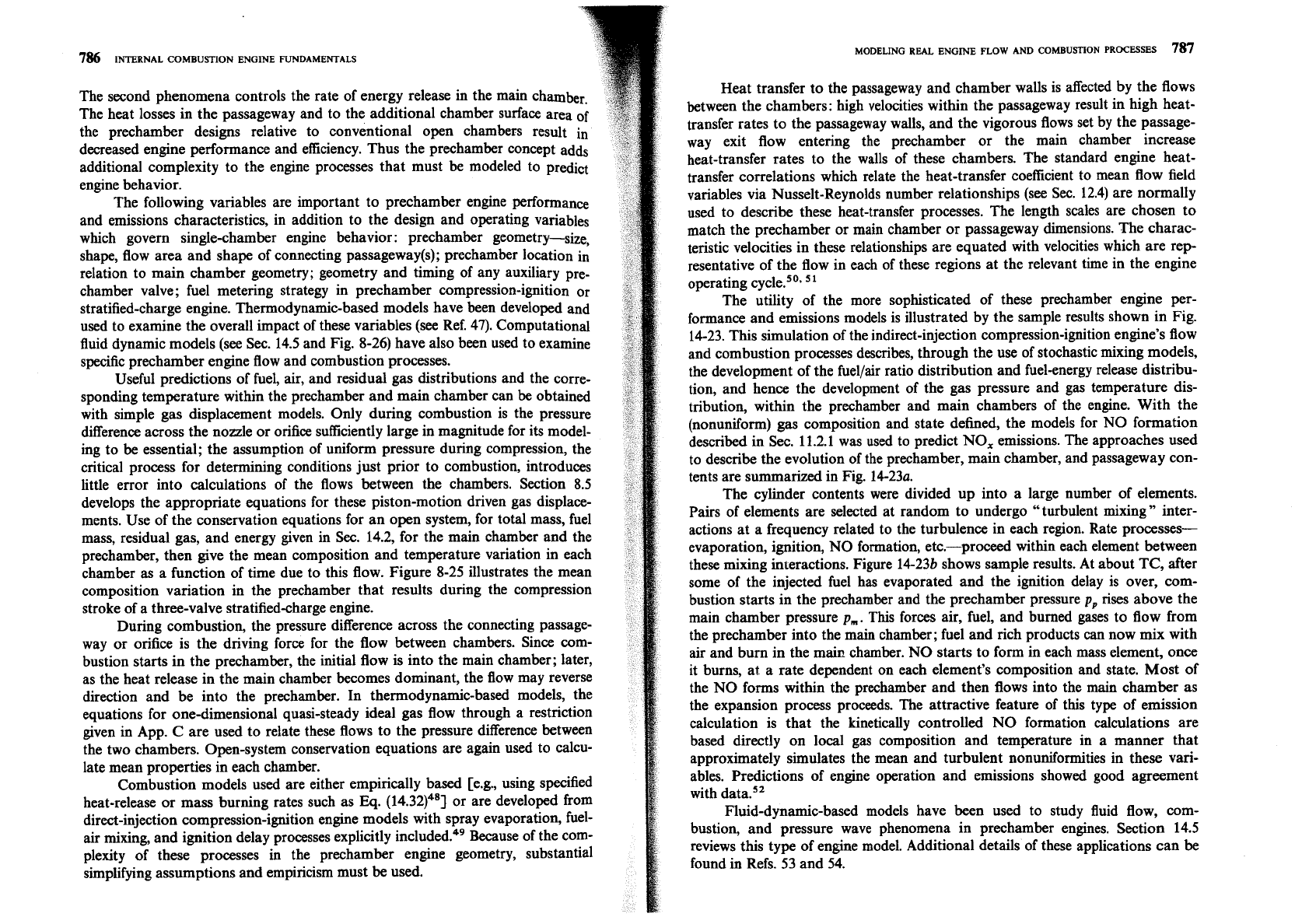
The second phenomena controls the rate of energy release in the main chamber.
The heat losses in the passageway and to the additional chamber surface area
of
the prechamber designs relative to conventional open chambers result in
decreased engine performance and efficiency. Thus the prechamber concept ad&
additional complexity to the engine processes that must be modeled to predict
engine behavior.
The following variables are important to prechamber engine performance
and emissions characteristics, in addition to the design and operating variables
which govern singlechamber engine behavior: prechamber geometry--size,
shape, flow area and shape of connecting
passageway(s); prechamber location in
relation to main chamber geometry; geometry and timing of any auxiliary pre-
chamber valve; fuel metering strategy in prechamber compression-ignition or
stratified-charge engine. Thermodynamic-based models have been developed and
used to examine the overall impact of these variables (see Ref. 47). Computational
fluid dynamic models (see Sec. 14.5 and Fig. 8-26) have also been used to examine
specific prechamber engine flow and combustion processes.
Useful predictions of fuel,
air,
and residual gas distributions and the corre-
sponding temperature within the prechamber and main chamber can be obtained
with simple gas displacement models. Only during combustion is the pressure
difference across the nozzle or orifice sufficiently large in magnitude for its model-
ing to be essential; the assumption of uniform pressure during compression, the
critical process for determining conditions just prior to combustion, introduces
little error into calculations of the flows between the chambers. Section 8.5
develops the appropriate equations for these piston-motion driven gas displace-
ments. Use of the conservation equations for an open system, for total mass, fuel
mass, residual gas, and energy given in
Sec. 14.2, for the main chamber and the
prechamber, then give the mean composition and temperature variation in each
chamber as a function of time due to this flow. Figure 8-25 illustrates the mean
composition variation in the prechamber that results during the compression
stroke of a three-valve stratifiedcharge engine.
During combustion, the pressure difference across the connecting passage-
way or orifice is the driving force for the flow between chambers. Since com-
bustion starts in the prechamber, the initial flow is into the main chamber; later,
as the heat release in the main chamber becomes dominant, the flow may reverse
direction and be into the prechamber. In thermodynamic-based models, the
equations for one-dimensional quasi-steady ideal gas flow through a restriction
given in App. C are used to relate these flows to the pressure difference between
the two chambers. Open-system conservation equations are again used to calcu-
late mean properties in each chamber.
Combustion models used are either empirically based
[e.g., using specified
heat-release or mass burning rates such as Eq. (14.32)48] or are developed from
direct-injection compression-ignition engine models with spray evaporation, fuel-
air mixing, and ignition delay processes explicitly included?' Because of the com-
plexity of these processes
in the prechamber engine geometry, substantial
simplifying assumptions and empiricism must be used.
MODELING REAL
ENGINE
FLOW
AND COMBUSTION PROCESSES
787
Heat transfer to the passageway and chamber walls is affected by the flows
between the chambers: high velocities within the passageway result in high heat-
transfer rates to the passageway walls, and the vigorous flows set by the passage-
way exit flow entering the prechamber or the main chamber increase
heat-transfer rates to the walls of these chambers. The standard engine heat-
transfer correlations which relate the heat-transfer coefficient to mean flow field
variables via Nusselt-Reynolds number relationships (see
Sec. 12.4) are normally
used to describe these heat-transfer processes. The length scales are chosen to
match the prechamber or main chamber or passageway dimensions. The charac-
teristic velocities in these relationships are equated with velocities which are rep-
resentative of the flow in each of these regions at the relevant time in the engine
operating
cycle.50.
The utility of the more sophisticated of these prechamber engine per-
formance and emissions models is illustrated by the sample results shown in Fig.
14-23. This simulation of the indirect-injection compression-ignition engine's flow
and combustion processes describes, through the use of stochastic mixing models,
the development of the
fuellair ratio distribution and fuel-energy release distribu-
tion, and hence the development of the gas pressure and gas temperature dis-
tribution, within the prechamber and main chambers of the engine. With the
(nonuniform) gas composition and state defined, the models for NO formation
described in
Sec. 11.2.1 was used to predict NO, emissions. The approaches used
to describe the evolution of the prechamber, main chamber, and passageway con-
tents are summarized in Fig.
14-23a.
The cylinder contents were divided up into a large number of elements.
Pairs of elements are selected at random to undergo "turbulent mixing" inter-
actions at a frequency related to the turbulence in each region. Rate
processes-
evaporation, ignition, NO formation, etc.-proceed within each element between
these mixing interactions. Figure 14-23b shows sample results. At about TC, after
some of the injected fuel has evaporated and the ignition delay is over, com-
bustion starts in the prechamber and the prechamber pressure
p,
rises above the
main chamber pressure
p,.
This forces air, fuel, and burned gases to flow from
the prechamber into the main chamber; fuel and rich products can now mix with
air and burn in the main chamber. NO starts to form in each mass element, once
it burns, at a rate dependent on each element's composition and state. Most of
the NO forms within the prechamber and then flows into the main chamber as
the expansion process proceeds. The attractive feature of this type of emission
calculation is that the kinetically controlled NO formation calculations are
based directly on local gas composition and temperature in a manner that
approximately simulates the mean and turbulent
nonuniformities in these vari-
ables. Predictions of engine operation and emissions showed good agreement
with
data."
Fluid-dynamic-based models have been used to study fluid flow, com-
bustion, and pressure wave phenomena in prechamber engines. Section 14.5
reviews this type of engine model. Additional details of these applications can be
found
in
Refs. 53 and 54.