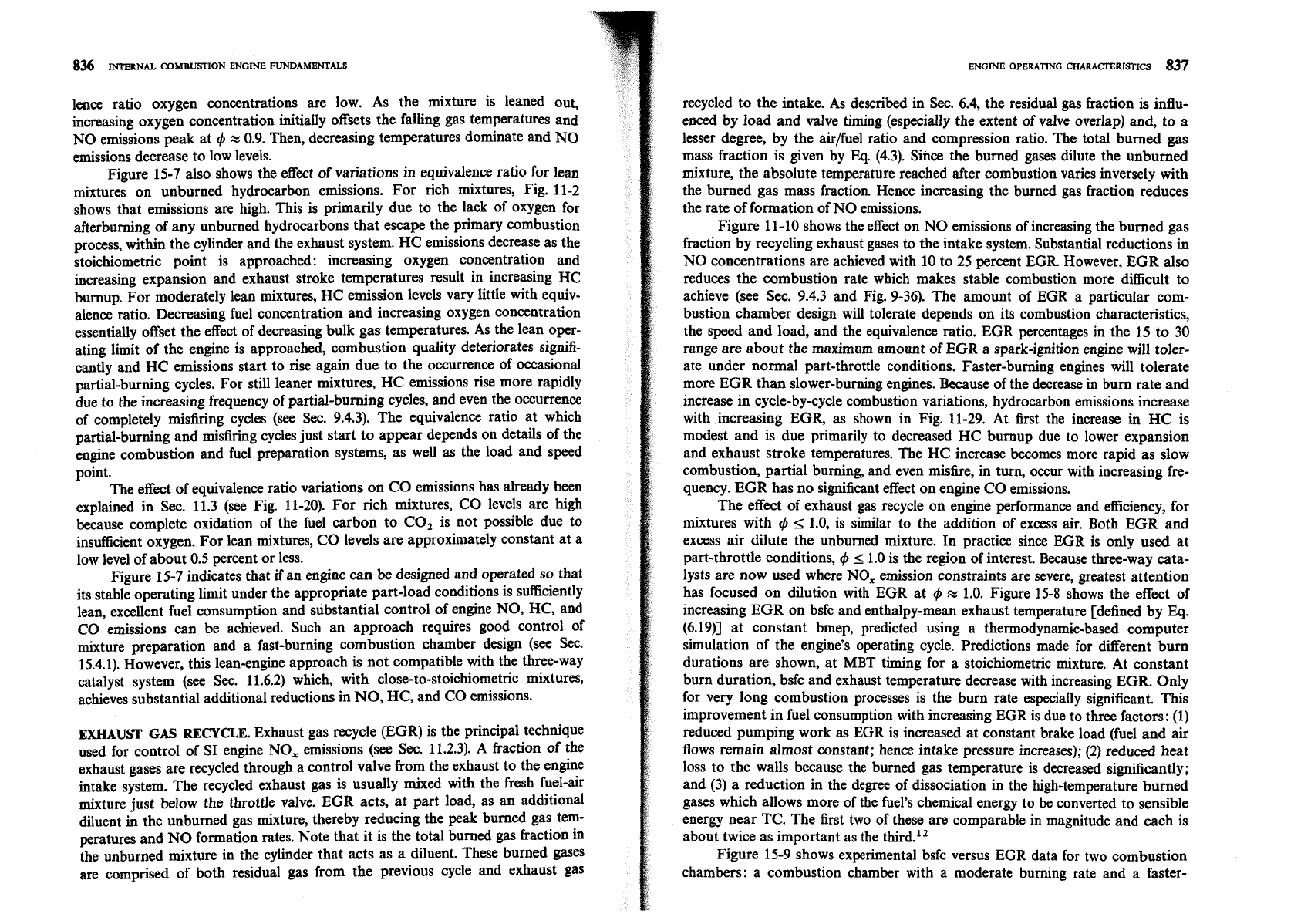
836
INTERNAL
COMBUSTION
ENGINE
FUNDAMENTALS
lence ratio oxygen concentrations are low. As the mixture is leaned out,
increasing oxygen concentration initially offsets the falling gas temperatures and
NO emissions peak at
4
%
0.9. Then, decreasing temperatures dominate and NO
emissions decrease to low levels.
Figure 15-7 also shows the effect of variations in equivalence ratio for lean
mixtures on unburned hydrocarbon emissions. For rich mixtures, Fig. 11-2
shows that emissions are high. This is primarily due to the lack of oxygen for
afterburning of any unburned hydrocarbons that escape the primary combustion
process, within the cylinder and the exhaust system. HC emissions decrease as the
stoichiometric point is approached: increasing oxygen concentration and
increasing expansion and exhaust stroke temperatures result in increasing HC
bumup. For moderately lean mixtures, HC emission levels vary little with equiv-
alence ratio. Decreasing fuel concentration and increasing oxygen concentration
essentially offset the effect of decreasing bulk gas temperatures. As the lean oper-
ating limit of the engine is approached, combustion quality deteriorates
sign&
cantly and HC emissions start to rise again due to the occurrence of occasional
partial-burning cycles. For still leaner mixtures, HC emissions rise more rapidly
due to the increasing frequency of partial-burning cycles, and even the occurrence
of completely misfiring cycles (see
Sec.
9.4.3). The equivalence ratio at which
partial-burning and misfiring cycles just start to appear depends on details of the
engine combustion and fuel preparation systems, as well as the load and speed
point.
The effect of equivalence ratio variations on CO emissions has already been
explained in
Sec. 11.3
(see
Fig. 11-20). For rich mixtures, CO levels are high
because complete oxidation of the fuel carbon to CO, is not possible due to
insufficient oxygen. For lean mixtures, CO levels are approximately constant at a
low level of about 0.5 percent or less.
Figure 15-7 indicates that
if
an engine can be designed and operated so that
its stable operating limit under the appropriate part-load conditions is sufficiently
lean, excellent fuel consumption and substantial control of engine NO, HC, and
CO emissions can
be
achieved. Such an approach requires good control of
mixture preparation and a fast-burning combustion chamber design
(see
Sec.
15.4.1). However, this lean-engine approach is not compatible with the three-way
catalyst system (see Sec. 11.6.2) which, with close-to-stoichiometric mixtures,
achieves substantial additional reductions in
NO,
HC, and CO emissions.
EXHAUST
GAS
RECYCLE.
Exhaust gas recycle (EGR) is the principal technique
used for control of SI engine NO, emissions (see Sec. 11.2.3). A fraction of the
exhaust gases are recycled through a control valve from the exhaust to the engine
intake system. The recycled exhaust gas is usually mixed with the fresh fuel-air
mixture just below the throttle valve. EGR acts, at part load, as an additional
diluent in the unburned gas mixture, thereby reducing the peak burned gas tem-
peratures and NO formation rates. Note that it is the total burned gas fraction in
the unburned mixture in the cylinder that acts as a diluent. These burned gases
are comprised of both residual gas from the previous cycle and exhaust gas
recycled to the intake. As described in
Sec. 6.4, the residual gas fraction is influ-
enced by load and valve timing (especially the extent of valve overlap) and, to a
lesser degree, by the airlfuel ratio and compression ratio. The total burned gils
mass fraction is given by Eq. (4.3). Since the burned gases dilute the unburned
mixture, the absolute temperature reached after combustion varies inversely with
the burned gas mass fraction. Hence increasing the burned gas fraction reduces
the rate of formation of NO emissions.
Figure 11-10 shows the effect on NO emissions of increasing the burned gas
fraction by recycling exhaust gases to the intake system. Substantial reductions in
NO concentrations are achieved with 10 to 25 percent EGR. However, EGR also
reduces the combustion rate which makes stable combustion more difficult to
achieve (see
Sec. 9.4.3 and Fig. 9-36). The amount of EGR a particular com-
bustion chamber design
will
tolerate depends on its combustion characteristics,
the speed and load, and the equivalence ratio. EGR percentages in the 15 to 30
range are about the maximum amount of EGR a spark-ignition engine will toler-
ate under normal part-throttle conditions. Faster-burning engines will tolerate
more EGR than slower-burning engines. Because of the decrease in bum rate and
increase in cycle-by-cycle combustion variations, hydrocarbon emissions increase
with increasing EGR, as shown in Fig. 11-29. At first the increase in HC is
modest and is due primarily to decreased HC
burnup due to lower expansion
and exhaust stroke temperatures. The HC increase becomes more rapid
as
slow
combustion, partial burning, and even misfire, in turn, occur with increasing fre-
quency. EGR has no significant effect on engine CO emissions.
The effect of exhaust gas recycle on engine performance and efficiency, for
mixtures with
q5
s
1.0, is similar to the addition of excess air. Both EGR and
excess air dilute the unburned mixture. In practice since EGR is only used at
part-throttle conditions,
4
I
1.0 is the region of interest. Because three-way cata-
lysts are now used where NO, emission constraints are severe, greatest attention
has focused on dilution with EGR at
4
FZ
1.0. Figure 15-8 shows the effect of
increasing EGR on bsfc and enthalpy-mean exhaust temperature [defined by Eq.
(6.19)] at constant bmep, predicted using a thermodynamic-based computer
simulation of the engine's operating cycle. Predictions made for different bum
durations are shown, at MBT timing for a stoichiometric mixture. At constant
burn duration, bsfc and exhaust temperature decrease with increasing EGR. Only
for very long combustion processes is the burn rate especially
significant. This
improvement in fuel consumption with increasing EGR is due to three factors: (1)
reduced pumping work as EGR is increased at constant brake load (fuel and air
flows remain almost constant; hence intake pressure increases); (2) reduced heat
loss to the walls because the burned gas temperature is decreased significantly;
and (3) a reduction in the degree of dissociation in the high-temperature burned
gases which allows more of the fuel's chemical energy to
be
converted to sensible
energy near TC. The first two of these are comparable in magnitude and each is
about twice as important as the third."
Figure 15-9 shows experimental bsfc versus EGR data for two combustion
chambers: a combustion chamber with a moderate burning rate and a
faster-