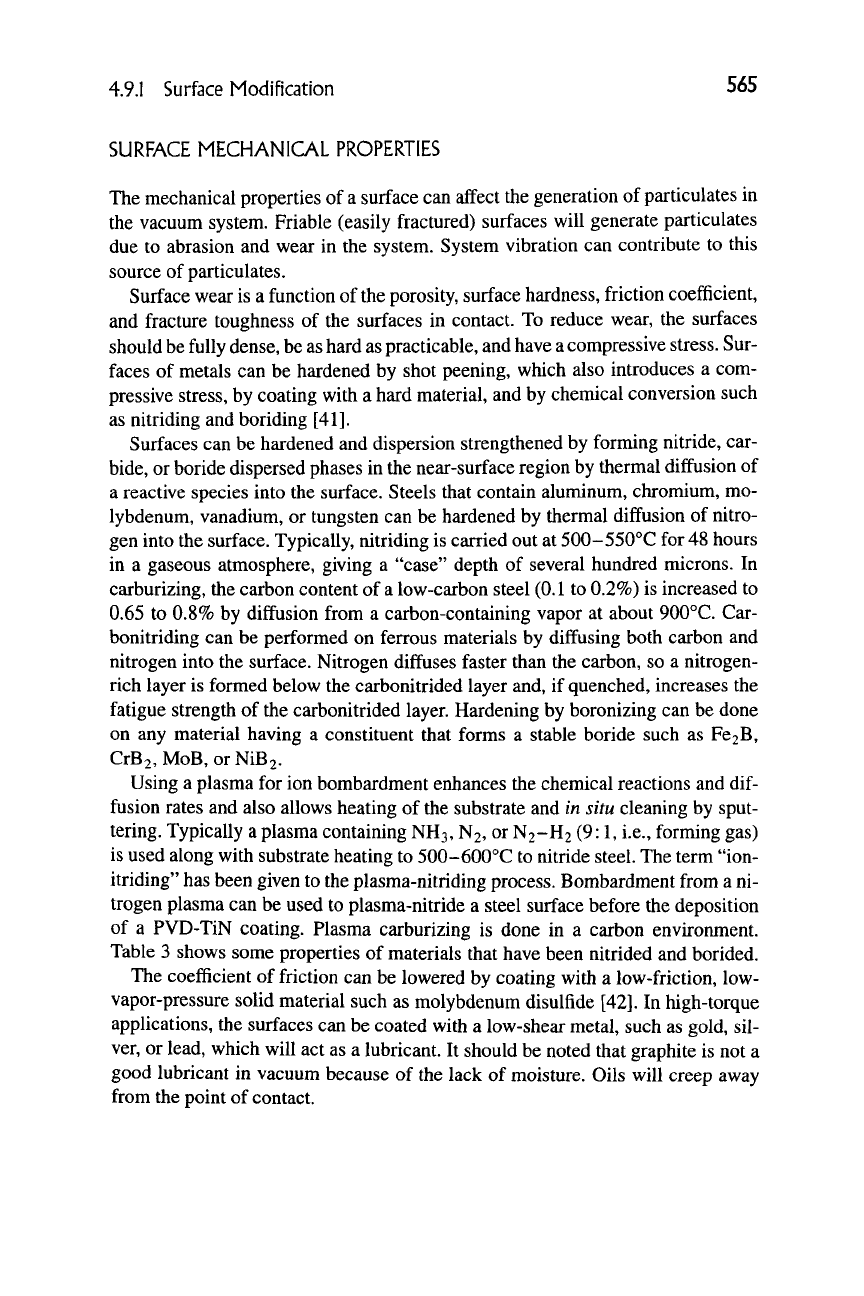
4.9.1 Surface Modification 565
SURFACE MECHANICAL PROPERTIES
The mechanical properties of a surface can affect the generation of particulates in
the vacuum system. Friable (easily fractured) surfaces will generate particulates
due to abrasion and wear in the system. System vibration can contribute to this
source of particulates.
Surface wear is a function of the porosity, surface hardness, friction coefficient,
and fracture toughness of the surfaces in contact. To reduce wear, the surfaces
should be fully dense, be as hard as practicable, and have
a
compressive
stress.
Sur-
faces of metals can be hardened by shot peening, which also introduces a com-
pressive stress, by coating with a hard material, and by chemical conversion such
as nitriding and bonding [41].
Surfaces can be hardened and dispersion strengthened by forming nitride, car-
bide,
or boride dispersed phases in the near-surface region by thermal diffusion of
a reactive species into the surface. Steels that contain aluminum, chromium, mo-
lybdenum, vanadium, or tungsten can be hardened by thermal diffusion of nitro-
gen into the surface. Typically, nitriding is carried out at 500-550°C for 48 hours
in a gaseous atmosphere, giving a "case" depth of several hundred microns. In
carburizing, the carbon content of a low-carbon steel (0.1 to 0.2%) is increased to
0.65 to 0.8% by diffusion from a carbon-containing vapor at about 900°C. Car-
bonitriding can be performed on ferrous materials by diffusing both carbon and
nitrogen into the surface. Nitrogen diffuses faster than the carbon, so a nitrogen-
rich layer is formed below the carbonitrided layer and, if quenched, increases the
fatigue strength of the carbonitrided layer. Hardening by boronizing can be done
on any material having a constituent that forms a stable boride such as Fe2B,
CrB2,
MoB, orNiB2.
Using a plasma for ion bombardment enhances the chemical reactions and
dif-
fusion rates and also allows heating of the substrate and in situ cleaning by sput-
tering. Typically a plasma containing NH3, N2, or N2-H2
(9:1,
i.e., forming gas)
is used along with substrate heating to 500-600°C to nitride steel. The term "ion-
itriding" has been given to the plasma-nitriding process. Bombardment from a ni-
trogen plasma can be used to plasma-nitride a steel surface before the deposition
of a PVD-TiN coating. Plasma carburizing is done in a carbon environment.
Table 3 shows some properties of materials that have been nitrided and borided.
The coefficient of friction can be lowered by coating with a low-friction, low-
vapor-pressure solid material such as molybdenum disulfide [42]. In high-torque
applications, the surfaces can be coated with a low-shear metal, such as gold, sil-
ver, or lead, which will act as a lubricant. It should be noted that graphite is not a
good lubricant in vacuum because of the lack of moisture. Oils will creep away
from the point of contact.