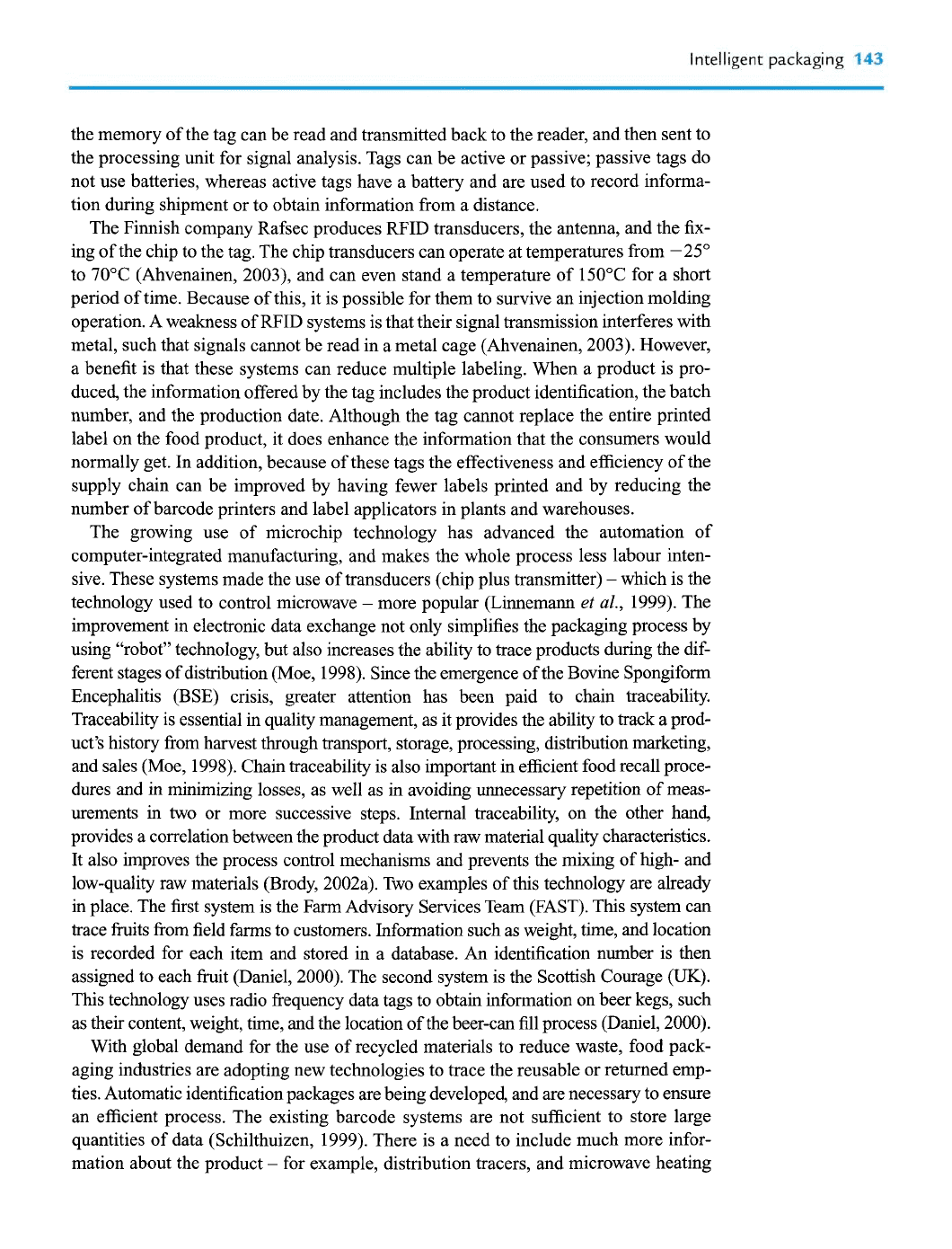
Intelligent packaging 143
the memory of the tag can be read and transmitted back to the reader, and then sent to
the processing unit for signal analysis. Tags can be active or passive; passive tags do
not use batteries, whereas active tags have a battery and are used to record informa-
tion during shipment or to obtain information from a distance.
The Finnish company Rafsec produces RFID transducers, the antenna, and the fix-
ing of the chip to the tag. The chip transducers can operate at temperatures from -25°
to 70°C (Ahvenainen, 2003), and can even stand a temperature of 150°C for a short
period of
time.
Because of
this,
it is possible for them to survive an injection molding
operation. A weakness of RFID systems is that their signal transmission interferes with
metal, such that signals cannot be read in a metal cage (Ahvenainen, 2003). However,
a benefit is that these systems can reduce multiple labeling. When a product is pro-
duced, the information offered by the tag includes the product identification, the batch
number, and the production date. Although the tag cannot replace the entire printed
label on the food product, it does enhance the information that the consumers would
normally get. In addition, because of these tags the effectiveness and efficiency of the
supply chain can be improved by having fewer labels printed and by reducing the
number of barcode printers and label applicators in plants and warehouses.
The growing use of microchip technology has advanced the automation of
computer-integrated manufacturing, and makes the whole process less labour inten-
sive.
These systems made the use of transducers (chip plus transmitter) - which is the
technology used to control microwave - more popular (Linnemann et aL, 1999). The
improvement in electronic data exchange not only simplifies the packaging process by
using "robot" technology, but also increases the ability to trace products during the
dif-
ferent stages of distribution (Moe, 1998). Since the emergence of the Bovine Spongiform
Encephalitis (BSE) crisis, greater attention has been paid to chain traceability.
Traceability is essential in quality management, as it provides the ability to track a prod-
uct's history from harvest through transport, storage, processing, distribution marketing,
and sales (Moe, 1998). Chain traceability is also important in efficient food recall proce-
dures and in minimizing losses, as well as in avoiding unnecessary repetition of meas-
urements in two or more successive steps. Internal traceability, on the other hand,
provides a correlation between the product data with raw material quality characteristics.
It also improves the process control mechanisms and prevents the mixing of high- and
low-quality raw materials (Brody, 2002a). Two examples of
this
technology are already
in place. The first system is the Farm Advisory Services Team (FAST). This system can
trace finits from field farms to customers. Information such as weight, time, and location
is recorded for each item and stored in a database. An identification number is then
assigned to each finit (Daniel, 2000). The second system is the Scottish Courage (UK).
This technology uses radio frequency data tags to obtain information on beer kegs, such
as their content, weight, time, and the location of the beer-can fill process (Daniel, 2000).
With global demand for the use of recycled materials to reduce waste, food pack-
aging industries are adopting new technologies to trace the reusable or returned emp-
ties.
Automatic identification packages are being developed, and are necessary to ensure
an efficient process. The existing barcode systems are not sufficient to store large
quantities of data (Schilthuizen, 1999). There is a need to include much more infor-
mation about the product - for example, distribution tracers, and microwave heating