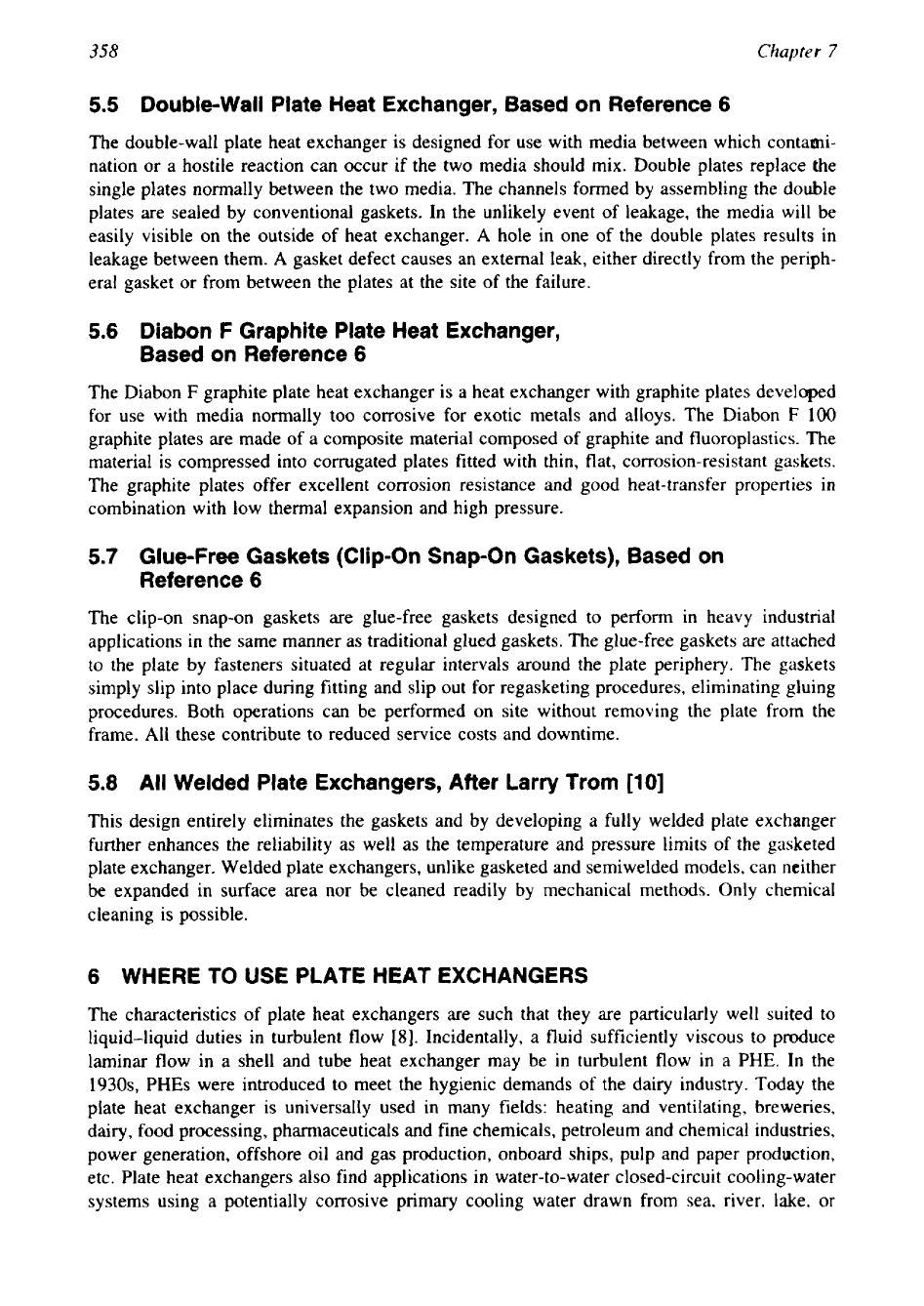
358
Chapter
7
5.5
Double-Wall Plate Heat Exchanger, Based on Reference
6
The double-wall plate heat exchanger is designed for use with media between which contami-
nation or a hostile reaction can occur if the two media should mix. Double plates replace the
single plates normally between the two media. The channels formed by assembling the double
plates are sealed by conventional gaskets. In the unlikely event of leakage, the media will be
easily visible on the outside of heat exchanger. A hole in one of the double plates results in
leakage between them. A gasket defect causes an external leak, either directly from the periph-
eral gasket or from between the plates at the site of the failure.
5.6
Diabon
F
Graphite Plate Heat Exchanger,
Based on Reference
6
The Diabon
F
graphite plate heat exchanger is a heat exchanger with graphite plates developed
for use with media normally too corrosive for exotic metals and alloys. The Diabon
F
100
graphite plates are made
of
a composite material composed
of
graphite and fluoroplastics. The
material is compressed into corrugated plates fitted with thin, flat, corrosion-resistant gaskets.
The graphite plates offer excellent corrosion resistance and good heat-transfer properties
in
combination with low thermal expansion and high pressure.
5.7
Glue-Free Gaskets (Clip-On Snap-On Gaskets), Based on
Reference
6
The clip-on snap-on gaskets are glue-free gaskets designed to perform in heavy industrial
applications in the same manner as traditional glued gaskets. The glue-free gaskets are attached
to
the plate by fasteners situated at regular intervals around the plate periphery. The gaskets
simply slip into place during fitting and slip out for regasketing procedures, eliminating gluing
procedures. Both operations can be performed on site without removing the plate from the
frame. All these contribute to reduced service costs and downtime.
5.8
All Welded Plate Exchangers, After Larry Trom
[lO]
This design entirely eliminates the gaskets and by developing a fully welded plate exchanger
further enhances the reliability as well as the temperature and pressure limits of the gasketed
plate exchanger. Welded plate exchangers, unlike gasketed and semiwelded models, can neither
be expanded in surface area nor be cleaned readily by mechanical methods. Only chemical
cleaning is possible.
6
WHERETOUSEPLATEHEATEXCHANGERS
The characteristics
of
plate heat exchangers are such that they are particularly well suited to
liquid-liquid duties in turbulent flow
[8].
Incidentally, a fluid sufficiently viscous
to
produce
laminar flow in a shell and tube heat exchanger may be in turbulent flow
in
a
PHE.
In the
1930s,
PHEs
were introduced to meet the hygienic demands of the dairy industry. Today the
plate heat exchanger is universally used in many fields: heating and ventilating, breweries,
dairy, food processing, pharmaceuticals and fine chemicals, petroleum and chemical industries,
power generation, offshore oil and gas production, onboard ships, pulp and paper production,
etc. Plate heat exchangers also find applications in water-to-water closed-circuit cooling-water
systems using a potentially corrosive primary cooling water drawn from sea, river, lake, or