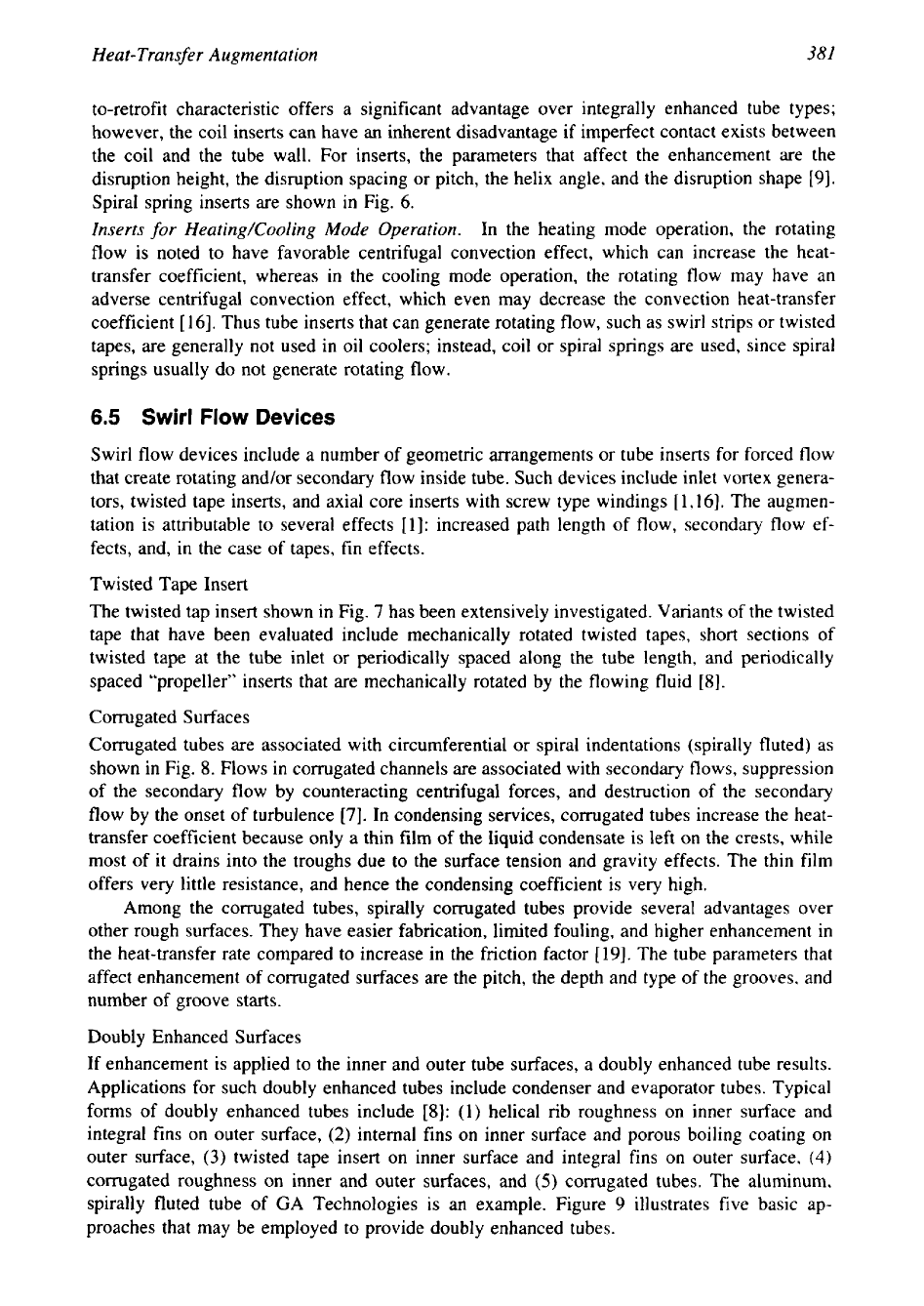
Heat-Transfer Augmentation
381
to-retrofit characteristic offers a significant advantage over integrally enhanced tube types;
however, the coil inserts can have
an
inherent disadvantage if imperfect contact exists between
the coil and the tube wall. For inserts, the parameters that affect the enhancement are the
disruption height, the disruption spacing or pitch, the helix angle, and the disruption shape
[9].
Spiral spring inserts are shown in Fig.
6.
Inserts
for
HeatingKooling Mode Operation.
In the heating mode operation, the rotating
flow is noted to have favorable centrifugal convection effect, which can increase the heat-
transfer coefficient, whereas in the cooling mode operation, the rotating flow may have an
adverse centrifugal convection effect, which even may decrease the convection heat-transfer
coefficient
[
161. Thus tube inserts that can generate rotating flow, such as swirl strips or twisted
tapes, are generally not used in oil coolers; instead, coil or spiral springs are used, since spiral
springs usually do not generate rotating flow.
6.5
Swirl
Flow
Devices
Swirl flow devices include a number of geometric arrangements
or
tube inserts for forced flow
that create rotating and/or secondary flow inside tube. Such devices include inlet vortex genera-
tors, twisted tape inserts, and axial core inserts with screw type windings [1,16]. The augmen-
tation is attributable to several effects [l]: increased path length
of
flow, secondary flow ef-
fects, and, in the case of tapes, fin effects.
Twisted Tape Insert
The twisted tap insert shown in Fig.
7
has been extensively investigated. Variants of the twisted
tape that have been evaluated include mechanically rotated twisted tapes, short sections of
twisted tape at the tube inlet or periodically spaced along the tube length, and periodically
spaced “propeller” inserts that are mechanically rotated by the flowing fluid [8].
Corrugated Surfaces
Corrugated tubes are associated with circumferential or spiral indentations (spirally fluted) as
shown in Fig.
8.
Flows in corrugated channels are associated with secondary flows, suppression
of the secondary flow by counteracting centrifugal forces, and destruction of the secondary
flow by the onset of turbulence
[7].
In condensing services, corrugated tubes increase the heat-
transfer coefficient because only a thin film of the liquid condensate is left on the crests, while
most of it drains into the troughs due to the surface tension and gravity effects. The thin film
offers very little resistance, and hence the condensing coefficient is very high.
Among the corrugated tubes, spirally corrugated tubes provide several advantages over
other rough surfaces. They have easier fabrication, limited fouling, and higher enhancement in
the heat-transfer rate compared to increase in the friction factor
[19].
The tube parameters that
affect enhancement of corrugated surfaces are the pitch, the depth and type of the grooves, and
number of groove starts.
Doubly Enhanced Surfaces
If enhancement is applied to the inner and outer tube surfaces, a doubly enhanced tube results.
Applications for such doubly enhanced tubes include condenser and evaporator tubes. Typical
forms
of
doubly enhanced tubes include
[8]:
(1) helical rib roughness on inner surface and
integral fins on outer surface,
(2)
internal fins on inner surface and porous boiling coating on
outer surface,
(3)
twisted tape insert on inner surface and integral fins on outer surface,
(4)
corrugated roughness on inner and outer surfaces, and
(5)
corrugated tubes. The aluminum,
spirally fluted tube of GA Technologies is an example. Figure
9
illustrates five basic ap-
proaches that may be employed to provide doubly enhanced tubes.