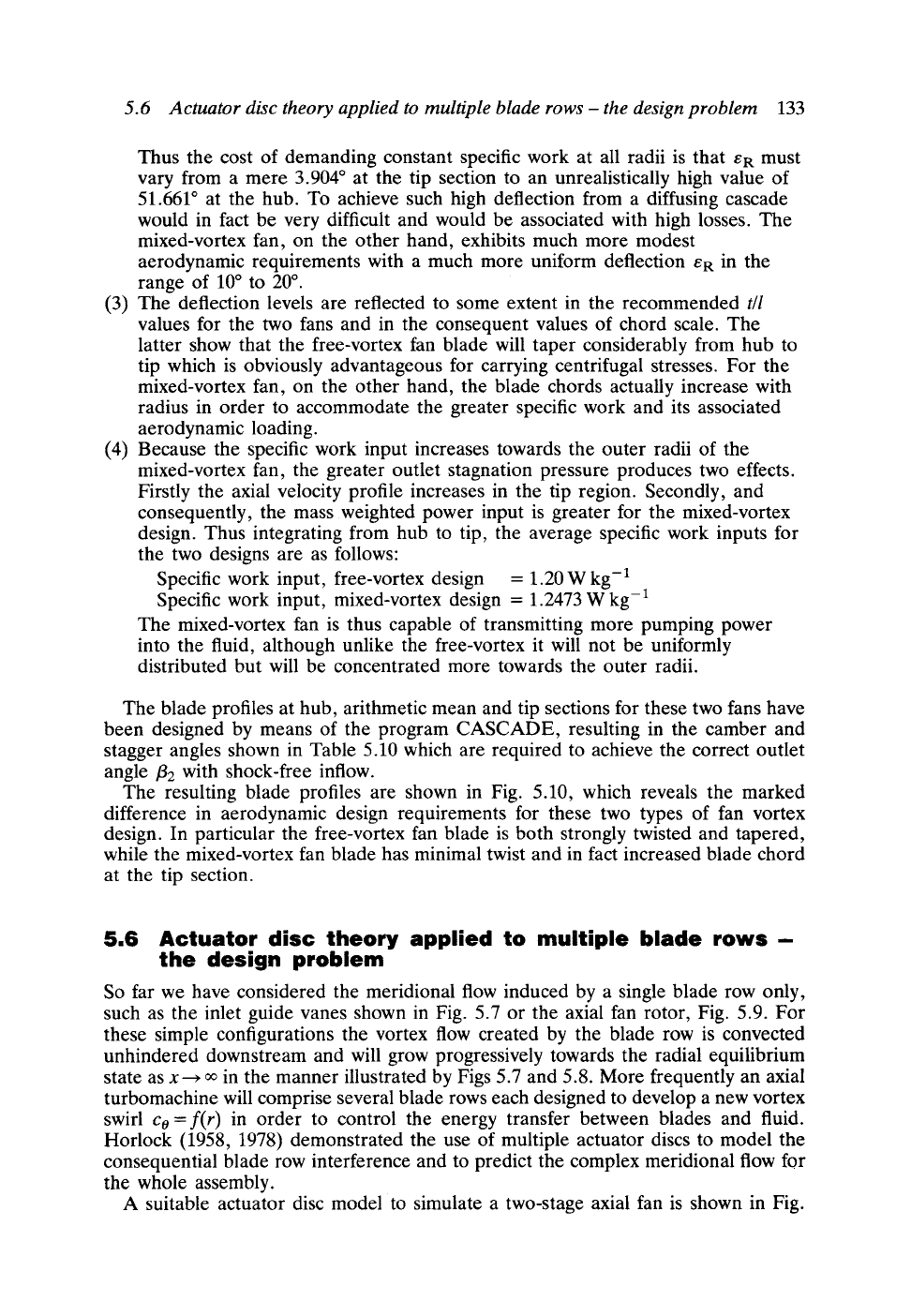
5.6 Actuator disc theory applied to multiple blade rows- the design problem 133
(3)
(4)
Thus the cost of demanding constant specific work at all radii is that eR must
vary from a mere 3.904 ~ at the tip section to an unrealistically high value of
51.661 ~ at the hub. To achieve such high deflection from a diffusing cascade
would in fact be very difficult and would be associated with high losses. The
mixed-vortex fan, on the other hand, exhibits much more modest
aerodynamic requirements with a much more uniform deflection eR in the
range of 10 ~ to 20 ~
The deflection levels are reflected to some extent in the recommended t/l
values for the two fans and in the consequent values of chord scale. The
latter show that the free-vortex fan blade will taper considerably from hub to
tip which is obviously advantageous for carrying centrifugal stresses. For the
mixed-vortex fan, on the other hand, the blade chords actually increase with
radius in order to accommodate the greater specific work and its associated
aerodynamic loading.
Because the specific work input increases towards the outer radii of the
mixed-vortex fan, the greater outlet stagnation pressure produces two effects.
Firstly the axial velocity profile increases in the tip region. Secondly, and
consequently, the mass weighted power input is greater for the mixed-vortex
design. Thus integrating from hub to tip, the average specific work inputs for
the two designs are as follows:
Specific work input, free-vortex design = 1.20 W kg -1
Specific work input, mixed-vortex design = 1.2473 W kg -1
The mixed-vortex fan is thus capable of transmitting more pumping power
into the fluid, although unlike the free-vortex it will not be uniformly
distributed but will be concentrated more towards the outer radii.
The blade profiles at hub, arithmetic mean and tip sections for these two fans have
been designed by means of the program CASCADE, resulting in the camber and
stagger angles shown in Table 5.10 which are required to achieve the correct outlet
angle/32 with shock-free inflow.
The resulting blade profiles are shown in Fig. 5.10, which reveals the marked
difference in aerodynamic design requirements for these two types of fan vortex
design. In particular the free-vortex fan blade is both strongly twisted and tapered,
while the mixed-vortex fan blade has minimal twist and in fact increased blade chord
at the tip section.
5,6
Actuator disc theory applied to multiple blade rows-
the design problem
So far we have considered the meridional flow induced by a single blade row only,
such as the inlet guide vanes shown in Fig. 5.7 or the axial fan rotor, Fig. 5.9. For
these simple configurations the vortex flow created by the blade row is convected
unhindered downstream and will grow progressively towards the radial equilibrium
state as x ~ oo in the manner illustrated by Figs 5.7 and 5.8. More frequently an axial
turbomachine will comprise several blade rows each designed to develop a new vortex
swirl co =f(r) in order to control the energy transfer between blades and fluid.
Horlock (1958, 1978) demonstrated the use of multiple actuator discs to model the
consequential blade row interference and to predict the complex meridional flow for
the whole assembly.
A suitable actuator disc model to simulate a two-stage axial fan is shown in Fig.