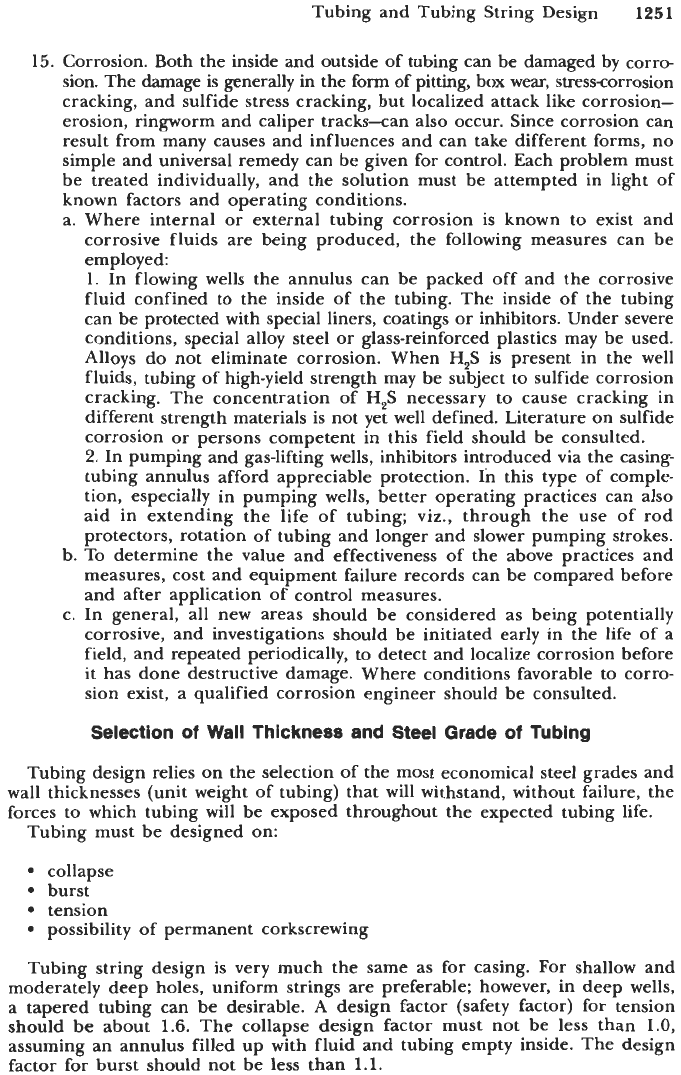
Tubing and Tubing String Design
1251
15.
Corrosion. Both the inside and outside of tubing can be damaged by corro-
sion. The damage is generally in the form of pitting, box wear, stresscorrosion
cracking, and sulfide stress cracking, but localized attack like corrosion-
erosion, ringworm and caliper tracks-can also occur. Since corrosion can
result from many causes and influences and can take different forms, no
simple and universal remedy can be given for control. Each problem must
be treated individually, and the solution must be attempted in light of
known factors and operating conditions.
a. Where internal or external tubing corrosion
is
known
to
exist and
corrosive fluids are being produced, the following measures can be
employed:
1.
In flowing wells the annulus can be packed off and the corrosive
fluid confined to the inside of the tubing. The inside of the tubing
can be protected with special liners, coatings or inhibitors. Under severe
conditions, special alloy steel or glass-reinforced plastics may be used.
Alloys do not eliminate corrosion. When
H,S
is present in the well
fluids, tubing of high-yield strength may be subject to sulfide corrosion
cracking. The concentration of
H,S
necessary to cause cracking in
different strength materials is not yet well defined. Literature on sulfide
corrosion or persons competent in this field should be consulted.
2.
In pumping and gas-lifting wells, inhibitors introduced via the casing-
tubing annulus afford appreciable protection.
In
this type of comple-
tion, especially in pumping wells, better operating practices can also
aid in extending the life of tubing; viz., through the use of rod
protectors, rotation of tubing and longer and slower pumping strokes.
b. To determine the value and effectiveness of the above practices and
measures, cost and equipment failure records can be compared before
and after application of control measures.
c. In general, all new areas should be considered as being potentially
corrosive, and investigations should be initiated early in the life of a
field, and repeated periodically,
to
detect and localize corrosion before
it has done destructive damage. Where conditions favorable to corro-
sion exist, a qualified corrosion engineer should be consulted.
Selection
of
Wall Thickness and Steel Grade of Tubing
Tubing design relies on the selection
of
the most economical steel grades and
wall thicknesses (unit weight of tubing) that will withstand, without failure, the
forces to which tubing will be exposed throughout the expected tubing life.
Tubing must be designed on:
collapse
burst
tension
possibility
of
permanent corkscrewing
Tubing string design is very much the same as for casing. For shallow and
moderately deep holes, uniform strings are preferable; however, in deep wells,
a tapered tubing can be desirable.
A
design factor (safety factor) for tension
should be about
1.6.
The collapse design factor must not be less than
1.0,
assuming an annulus filled up with fluid and tubing empty inside. The design
factor for burst should not be less than
1.1.