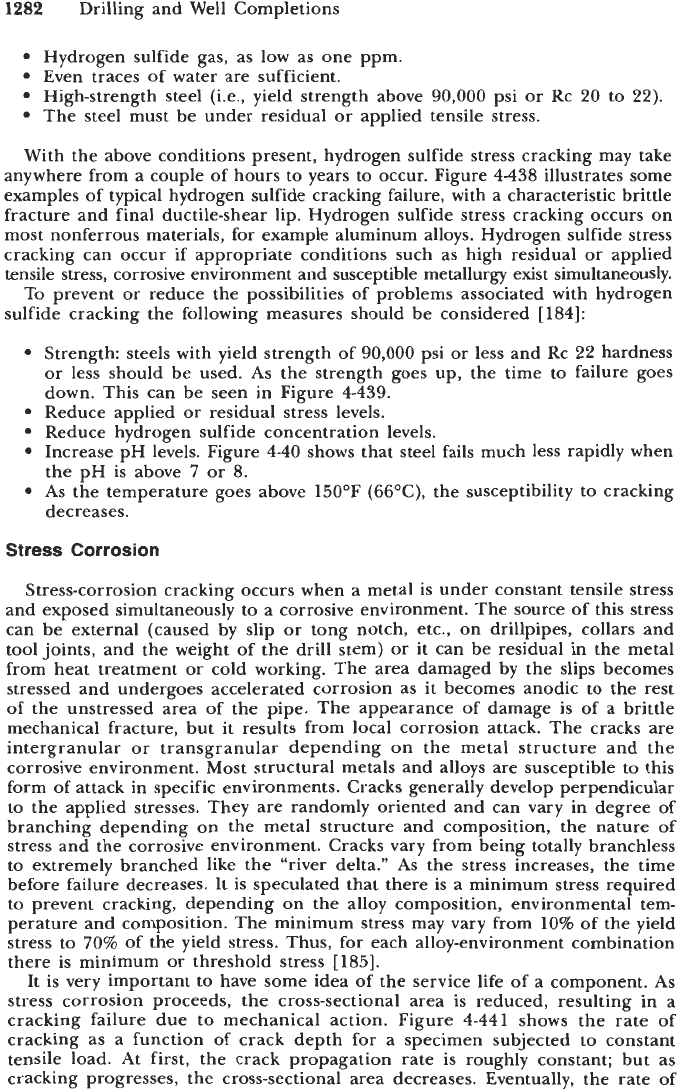
1282 Drilling and Well Completions
Hydrogen sulfide gas, as low as one ppm.
Even traces of water are sufficient.
High-strength steel (i.e., yield strength above
90,000
psi or Rc
20
to
22).
The steel must be under residual or applied tensile stress.
With the above conditions present, hydrogen sulfide stress cracking may take
anywhere from a couple of hours to years to occur. Figure 4-438 illustrates some
examples of typical hydrogen sulfide cracking failure, with a characteristic brittle
fracture and final ductile-shear lip. Hydrogen sulfide stress cracking occurs on
most nonferrous materials, for example aluminum alloys. Hydrogen sulfide stress
cracking can occur if appropriate conditions such as high residual
or
applied
tensile stress, corrosive environment and susceptible metallurgy exist simultaneously.
To prevent
or
reduce the possibilities of problems associated with hydrogen
sulfide cracking the following measures should be considered
[
1841:
Strength: steels with yield strength of
90,000
psi or less and Rc
22
hardness
or less should be used.
As
the strength goes up, the time to failure goes
down. This can be seen in Figure
4-439.
Reduce applied or residual stress levels.
Reduce hydrogen sulfide concentration levels.
Increase pH levels. Figure 4-40 shows that steel fails much less rapidly when
the pH is above
7
or
8.
As
the temperature goes above 150°F
(66’C),
the susceptibility to cracking
decreases.
Stress
Corrosion
Stress-corrosion cracking occurs when a metal is under constant tensile stress
and exposed simultaneously to a corrosive environment. The source of this stress
can be external (caused by slip
or
tong notch, etc., on drillpipes, collars and
tool joints, and the weight of the drill stem) or it can be residual in the metal
from heat treatment or cold working. The area damaged by the slips becomes
stressed and undergoes accelerated corrosion as it becomes anodic to the rest
of the unstressed area of the pipe. The appearance of damage is of a brittle
mechanical fracture, but it results from local corrosion attack. The cracks are
intergranular
or
transgranular depending on the metal structure and the
corrosive environment. Most structural metals and alloys are susceptible to this
form of attack in specific environments. Cracks generally develop perpendicular
to the applied stresses. They are randomly oriented and can vary in degree of
branching depending on the metal structure and composition, the nature
of
stress and the corrosive environment. Cracks vary from being totally branchless
to extremely branched like the “river delta.”
As
the stress increases, the time
before failure decreases. It is speculated that there is a minimum stress required
to prevent cracking, depending on the alloy composition, environmental tem-
perature and composition. The minimum stress may vary from 10% of the yield
stress to
70%
of the yield stress. Thus, for each alloy-environment combination
there is minimum or threshold stress [185].
It is very important to have some idea of the service life of a component.
As
stress corrosion proceeds, the cross-sectional area is reduced, resulting in a
cracking failure due to mechanical action. Figure 4-441 shows the rate of
cracking as a function of crack depth for a specimen subjected to constant
tensile load. At first, the crack propagation rate is roughly constant; but as
cracking progresses, the cross-sectional area decreases. Eventually, the rate of