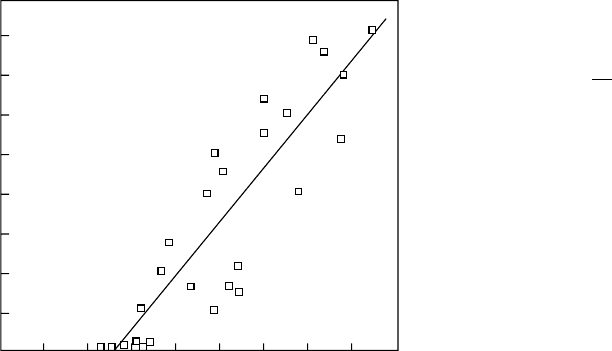
therefore U
l-lim
¼ 0:300 J. If the impact energy determined
in the Charpy test (see the section on impact behavior) is
higher than this value, rapid crack propagation will not occur.
Since the criterion is defined for a class of polyethylenes, a
safety factor somewhat larger than unity may be introduced.
24.2.6 Slow Crack Propagation and Its Prediction
The slow crack propagation (SCP) is vastly different from
RCP, not at all spectacular but in fact ‘‘quiet’’ and insidious.
The crack propagation rate dh/dt might be only, say, 1 mm
per month; an observation for instance two weeks after
installing a polymeric component might reveal nothing.
Experimentalists customarily present the dh/dt rates as a
function of the logarithmic stress intensity factor K
l
as
defined by Eq. (24.16); we now use h as the crack length
(as we did before) to differentiate it from the length L which
pertained to RCP. The problem clearly consisted in relating
dh/dt to K
l
. It was solved [49] by using the CRC approach in
conjunction with the Eq. (24.17) of fracture mechanics. The
problem was different than that of Griffith. He needed the
critical stress s
cr
above which crack propagation occurs for
a given crack length h. In our problem we need to know
whether the crack length is below a certain value, call it h
cr
,
so that the crack will not propagate [49]. We therefore
reformulate the Griffith Eq. (24.17) as
h
cr
¼ 2GE=ps
3
: (24:28)
By definition, the crack will propagate only when h > h
cr
.
This is not only a consequence of the CRC concept but also
supported by the molecular dynamics computer simulations
[50,51] showing that a crossover exists from the force field
region dominated by chain relaxation to one in which crack
propagation occurs.
Since notches with h < h
cr
do not cause crack propaga-
tion, it was only natural to assume
dh
dt
¼ b(h h
cr
) for h $ h
cr
, (24:29)
where b is a time-independent proportionality factor char-
acteristic for the material since it depends on CRC. We do
not have space here to provide details of the derivation; the
final result [49] is
log K
l
¼ (1=2) log (a
2
2GE)þ
(1=2) log [1 þ (1=bh
cr
)]dh=dt:
(24:30)
Equation (24.30) provides the desired connection between
K
l
and dh/dt. In the derivation both the stress level s and the
original crack length h
0
were used but both canceled out,
with the unexpected result that the crack propagation rate is
independent of both! The experimental results support Eq.
(24.30) as shown for instance in Fig. 24.3 for Hoechst PEs
studied under uniaxial tension in water medium at 60 8C.
Each symbol pertains to a different stress level and a differ-
ent original notch length. It is clear that all polyethylenes
with the molecular mass M
A
form a common curve, and the
same is true for the other molecular masses. Moreover, we
see that a higher M results in a lower crack propagation rate;
this result is related to the constituents of CRC listed at the
end of Section 24.1.3, particularly the first two of them.
In the beginning we have called SCP ‘‘insidious’’. The
lowest experimental crack propagation rate value in
Fig. 24.3 is dh=dt ¼ 10
8
cm s
1
; this is only 0.315 cm
per year, but the crack does grow. This fact gives us an
idea on the utility of Eq. (24.30).
24.3 QUASISTATIC TESTING AND TRANSIENT
TESTING
24.3.1 Types of Testing Procedures
We have already referred to various kinds of data on
mechanical behavior of polymers. We are now going to
consider methods of acquisition of such information. The
most frequently used are the so-called quasistatic methods
which involve relatively slow loading. Tension, compres-
sion, and flexure belong here. The quasistatic methods have
to be distinguished from so-called transient tests which
include stress relaxation and creep. There are also impact
tests and dynamic mechanical procedures which will be
defined later.
Specimens for testing may be produced by processing
operations such as injection molding, compression molding,
or machining from sheets. Machined surfaces have to be
smoothed in their long axis direction with abrasive paper.
Any flash on molded specimens shall be removed; the cross-
sectional area has to be uniform along the whole length
subjected to testing. Consequences of any nonuniformity
would show up as stress concentrators discussed above.
800
L/mm
700
600
500
400
300
200
100
0
23456
J/U
FIGURE 24.2. Length L/mm of the cracks in PE pipes
determined by the Greig-Smith test 50 vs. the reciprocal
Charpy impact energy (U=J)
1
; after [48].
MECHANICAL PROPERTIES / 429