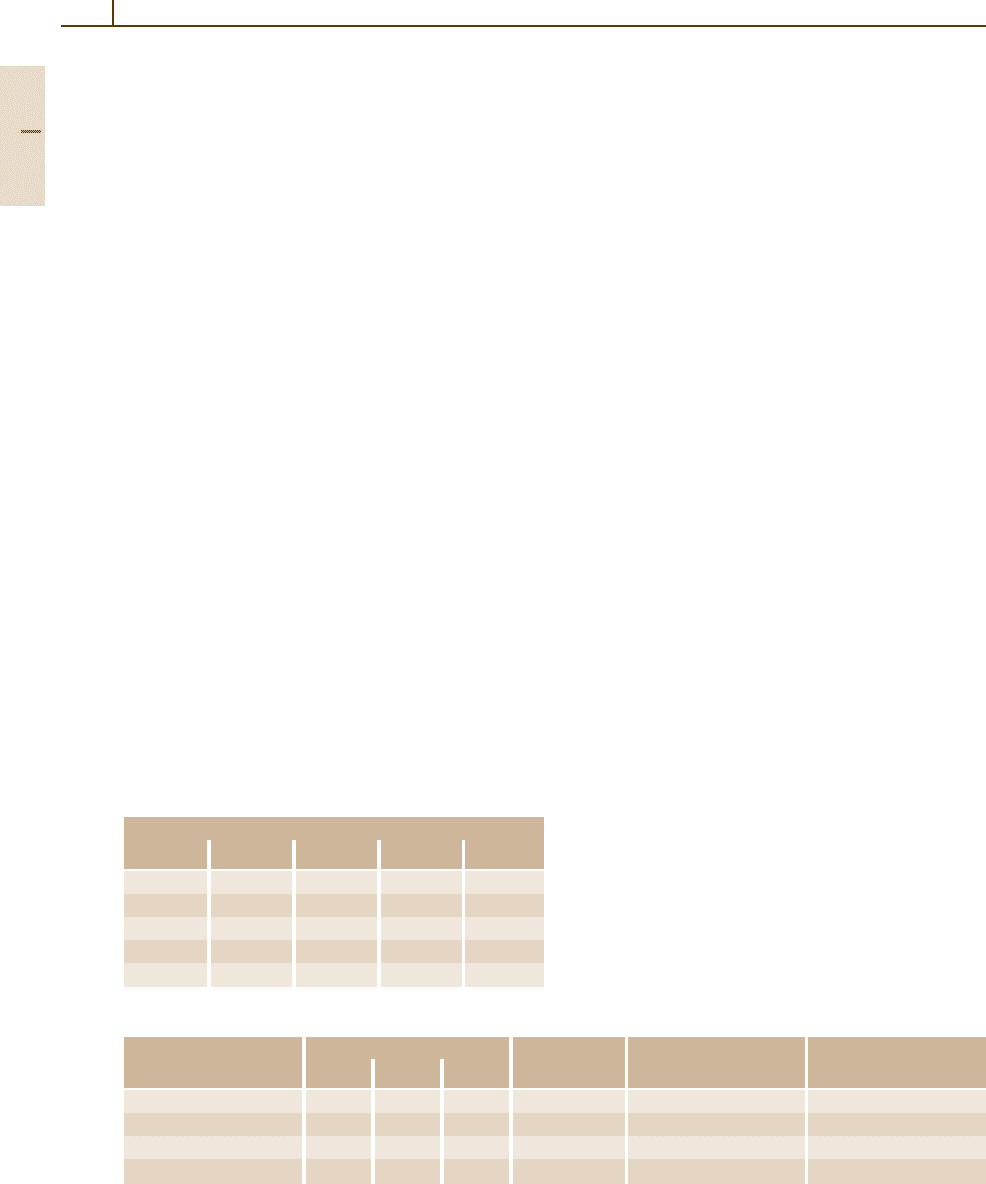
414 Part 3 Classes of Materials
discharge cycling. However, Sb migration from Pb
−
Sb
based positive grid alloys to negative electrode results
in the reduction of hydrogen over-voltage and conse-
quent decrease in cell voltage. This led to increased
degassing and water loss. To minimize this poisoning
of negative plates, lower Sb contents (1–3 wt% Sb) are
now used in battery grids. The posts and straps use
about 3 wt% Sb. Low Sb content promotes the forma-
tion of solidification shrinkage porosity and cracking
but the cracking tendency is overcome by the use of
grain-refining additions of S, Cu, and Se. Arsenic addi-
tions to Pb
−
Sb alloys increase the rate of age-hardening
and reduce the time of grid storage required after cast-
ing. Arsenic addition also increases the creep resistance
which is very beneficial in deep cycling conditions. The
addition of tin is used to act synergistically with As
and Sb to improve fluidity and castability. It also in-
creases cycle life of deep cycling batteries containing
thin plates. Silver additions increases both the corro-
sion and creep resistance in Pb
−
Sb alloy grids. Cast
Pb
−
Sb based alloys are typically used in grid alloys
as the Pb
−
Sb based wrought alloys have lower yield
strength, tensile strength, and creep strength. The cor-
rosion behavior of wrought alloys is inferior due to the
nature of distribution of the PbSb eutectic phase and
lower creep resistance. Corrosion of cast Pb
−
Sb occurs
by the attack of Pb
−
Sb eutectic. It solubilizes some Sb
and stresses of corrosion product are accommodated. In
rolled alloys the eutectic phase is isolated, which leads to
stresses in the grid. The current choice of alloy composi-
tion is Pb
−
1.6Sb
−
0.2As
−
0.2Sn
−
0.2Se. Table 3.1-280
Table 3.1-280 Alloying components of common lead–
antimony battery grid alloys [1.300,307]
Alloy concentration (wt%)
Sb
Sn As Cu Se
2.75 0.2 0.18 0.075 −
2.75 0.3 0.3 0.075 −
2.9 0.3 0.15 0.04 −
2.9 0.3 0.15 0.05 −
1.6 0.2 0.2 − 0.2
Table 3.1-281 Typical compositions and properties of selected type metals [1.299,300]
Alloy Composition (wt%) Hardness HB Liquidus temperature Solidus temperature
Pb Sn Sb (
◦
C) (
◦
C)
Electrotype – General 94 3 3 14 299 245
Linotype – Special 84 5 11 22 246 239
Stereotype – Flat 80 6 14 23 256 239
Monotype – Ordinary 78 7 15 24 262 239
lists the compositions of common lead–antimonybattery
grid alloys [1.300,307].
Lead–antimony alloys containing 0.2to1wt%Sb
are used to form barrier sheaths in high voltage cables.
Properties of Pb
−
0.85Sb cable sheathing alloy are pre-
sented in the section on cable sheathing alloys. Lead
alloys with 6–8 wt% Sb are used to fabricate a wide va-
riety of equipment such as tank linings, pipe and one
type of anode used in chromium plating. Alloys with
13 wt% Sb are used to make castings when hardness is
of key importance. About 6% of the Pb produced in the
world was used in the production of sports and military
ammunition due to its high density and low cost. Lead
containing up to 8 wt% Sb and 2 wt% As is used.
Pb–Sb–Sn Alloys
These alloys have low melting points, high hardness,
and excellent high temperature strength and fluidity.
These characteristics together with its applicability for
the replication of detail make them suitable as printing
types. Table 3.1-281 lists the characteristics of selected
type-metal alloys [1.300].
The Pb-rich ternary Pb
−
Sb
−
Sn white metal alloys
are also used in journal bearings due to the excellent
anti-friction (and anti-seizure) characteristics and hard-
ness. These Pb-rich white metal alloys, also referred to
as Babbit alloys, contain 9–15 wt% Sb, 1–20 wt% Sn,
and small amounts of Cu and As. Table 3.1-282 lists the
physical properties of different bearing alloys [1.299,
300]. The mechanical property data for some of these
alloys are presented in Table 3.1-283 [1.299,308]. Most
of the alloys lie in the primary crystallization field of
Sb or SbSn of the ternary system. They contain pri-
mary crystals of Sb (or SbSn) in a binary (or ternary)
eutectic matrix apart from the high-melting Cu-rich
phases. Copper contents above 1.5 wt% also increase
the hardness. Arsenic addition leads to a fine and uni-
form structure, improvesfatigue strength, and minimizes
softening. Arsenic is present in solid solution in Pb, Sb,
and Sb-containing phases such as SbSn. The lead–alkali
alloys, e.g., Bahnmetall, or the Pb
−
Sn
−
alkali alloys,
also have a limited significance as bearing metals.
Part 3 1.11