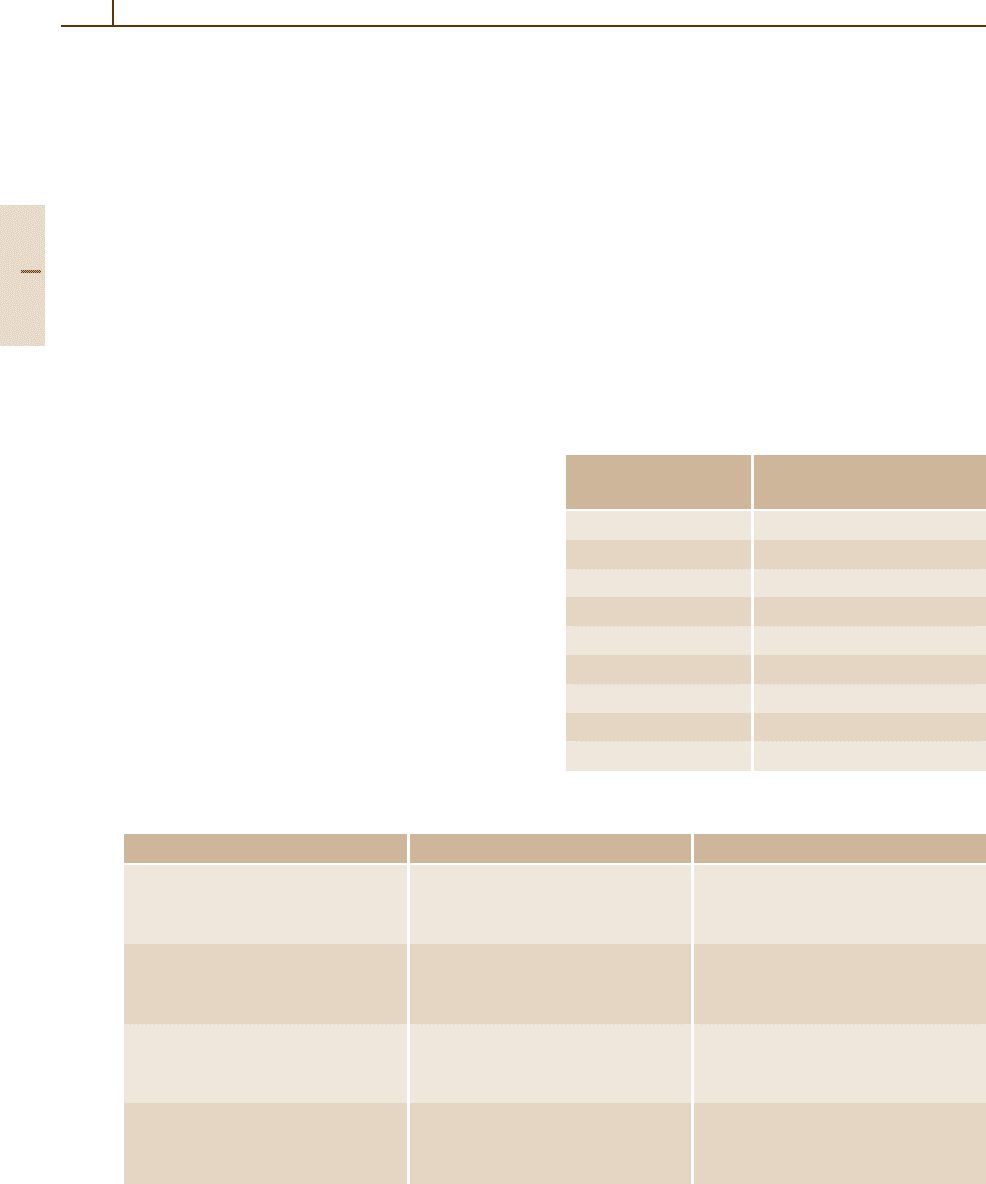
432 Part 3 Classes of Materials
3.2.1 Traditional Ceramics and Cements
3.2.1.1 Traditional Ceramics
Traditional ceramics are obtained by the firing of
clay-based materials. They are commonly composed
of a clay mineral (kaolinite, montmorillonite, or il-
lite), fluxing agents (orthoclase and plagioclase), and
filler materials (SiO
2
,Al
2
O
3
, and MgO). The pro-
cessing steps are mixing, forming, drying, firing
(high-temperature treatment in air), and finishing (enam-
eling, cleaning, and machining). The main classes of
traditional ceramics are fired bricks, whiteware (china,
stoneware, and porcelain), glazes, porcelain enamels,
high-temperature refractories, cements, mortars, and
concretes. Table 3.2-1 lists some of main groups of
traditional ceramics, with some of their properties and
applications.
3.2.1.2 Cements
Cement is the common binder of traditional build-
ing ceramics. It is produced by mixing about 80 wt%
of low-magnesium (< 3 wt% MgO) calcium carbonate
(CaCO
3
) (limestone, marl, or chalk) with about 20 wt%
clay (which may be obtained from clays, shale, or slag).
In terms of oxide content, this corresponds to a ratio
of CaO to SiO
2
of 3:1 by weight. The common term
“Portland cement” is based on the early use of a par-
ticular limestone called Portland stone. The processing
steps are milling and mixing, heating to 260
◦
C, pre-
calcining at 900
◦
C, and calcining in a rotary kiln at
Table 3.2-1 Examples of traditional ceramics [2.4]
Type Properties Applications
Fired brick Porosity 15–30% Bricks, pipes, ducts, walls,
Firing temperature 950–1050
◦
C floor tiles
May be enameled or not
China Porosity 10–15% Sanitary, tiles
Firing temperature 950–1200
◦
C
Enameled, opaque
Stoneware Porosity 0.5–3% Crucibles, labware, pipes
Firing temperature 1100–1300
◦
C
Glassy surface
Porcelain Porosity 0–2% Insulators, labware, cookware
Firing temperature 1100–1400
◦
C
Glassy, translucent
temperatures ≤ 1450
◦
C. The resulting product is termed
“clinker” and consists of a vitreous nodular material
composed of calcium silicates and aluminates. This is
mixed with 2 to 4 wt% gypsum (CaSO
4
·2H
2
O) to ad-
just the setting time, and ground to the final product. The
ranges of the percentages of the constituents are given
in Table 3.2-2.
Some standardized grades of Portland cement and
their uses are listed in Table 3.2-3. Mortars and con-
cretes are mixtures of cement with specified amounts of
sand, gravel, or crushed stones with specified particle
sizes.
Table 3.2-2 Chemical composition of Portland ce-
ment [2.4]
Component Average mass fraction
(wt%)
SiO
2
21.8 – 21.9
Al
2
O
3
4.9 – 6.9
Fe
2
O
3
2.4 – 2.9
CaO 63.0 – 65.0
MgO 1.1 – 2.5 (max. 3.0)
SO
3
1.7 – 2.6
Na
2
O 0.2
K
2
O 0.4
H
2
O 1.4 – 1.5
Part 3 2.1