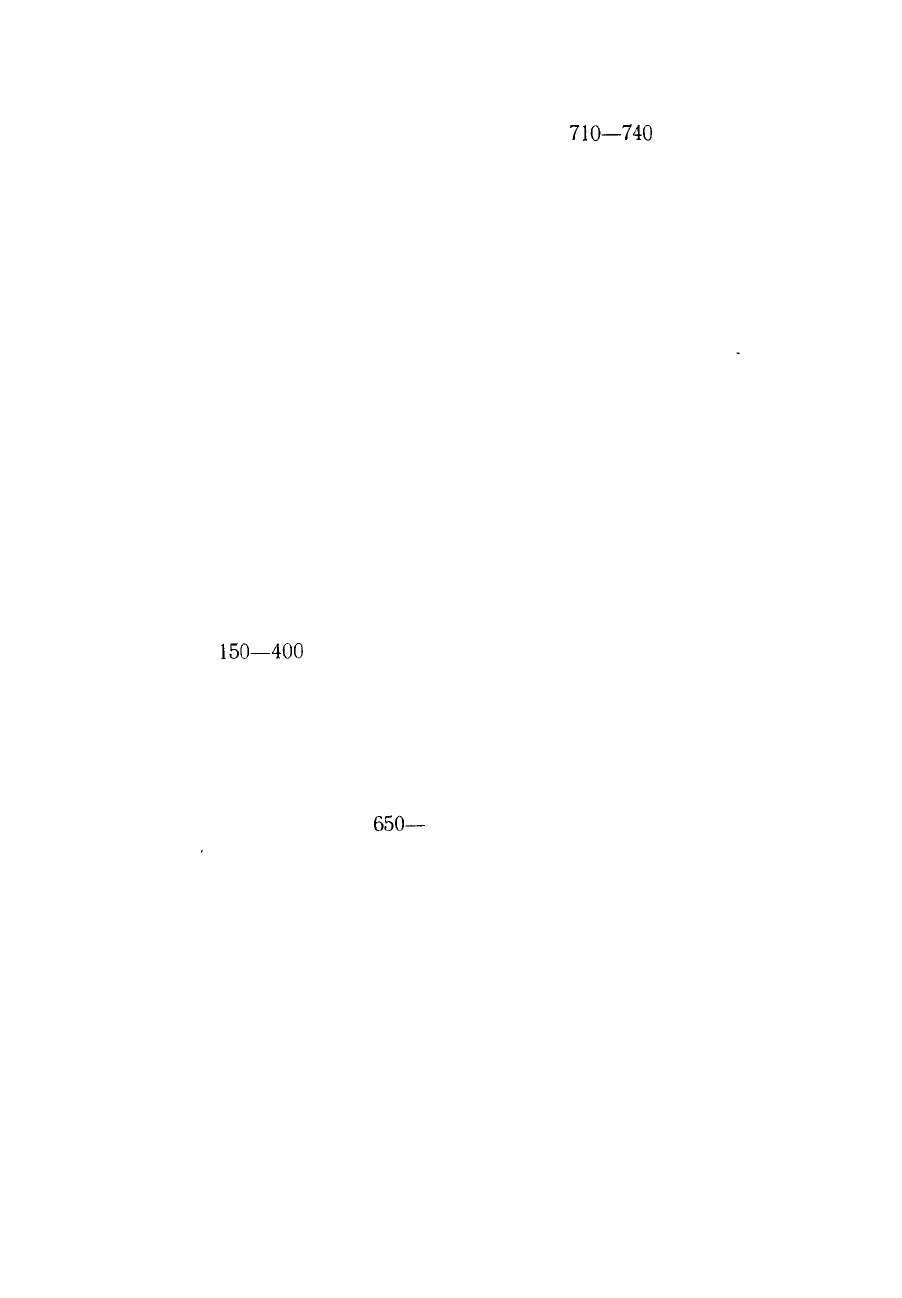
Работоспособность сварных сое-
динений в значительной степени за-
висит от правильно выбранной кон-
струкции шва, от качества обработки
кромок и сборки деталей под сварку.
Форма и конструктивные размеры
подготовленных под стыковую свар-
ку кромок зависят от способа сварки
и толщины стенки труб.
Качество электродуговой сварки
в значительной степени зависит от
правильного выбора марки электро-
дов и вида их покрытия. Покрытие
предназначено для ионизации газов
и стабилизации горения дуги, а так-
же для защиты расплавленного ме-
талла от кислорода и азота воздуха.
Большинство теплоустойчивых
перлитных сталей проявляет при свар-
ке без предварительного подогрева
склонность к образованию трещин,
обусловленных сварочными напряже-
ниями и структурными превращения-
ми. Для предотвращения этих явле-
ний при сварке применяются пред-
варительный и сопутствующий подо-
гревы, температура которых выбира-
ется в пределах
150—400
°С в зависи-
мости от марки стали и толщины сва-
риваемых деталей.
Сварные соединения толстостен-
ных труб из сталей 20 и 16ГС подвер-
гаются после выполнения сварного
стыка термообработке для
снятия остаточных сварочных напря-
жений с температурой нагрева
650—
680 °С.
Сварные соединения труб из ста-
лей 12Х1МФ и 15Х1М1Ф, как прави-
ло, после сварки имеют низкие пла-
стические и высокие прочностные свой-
ства (закалочную структуру). Такие
сварные соединения не удовлетворя-
ют требованиям Госгортехнадзора
СССР при испытании на угол загиба
и ударную вязкость и имеют чрезмер-
но высокую твердость. Это может быть
причиной образования трещин в шве
и в околошовной зоне. Вероятность
образования трещин возрастает с уве-
личением толщины стенки, так как
возрастают остаточные сварочные на-
пряжения. Для их снятия и улучше-
ния свойств металла шва и околошов-
ной зоны, повышения пластичности и
получения стабильной структуры при-
меняется термообработка в виде вы-
сокотемпературного отпуска — на-
грева до
710—740
°С.
Для контроля качества сварки
применяется ряд методов. Сварные
соединения до эксплуатации подвер-
гаются просвечиванию у-
излучением и проверке
ультразвуком. Для выявле-
ния поверхностных трещин в свар-
ных стыках применяются цветная де-
фектоскопия, магнитография и трав-
ление.
6.2. РАСЧЕТ ТРУБОПРОВОДОВ
НА ПРОЧНОСТЬ
Трубопроводы ТЭС и их детали
воспринимают избыточное внутрен-
нее давление. К напряжениям, вы-
званным давлением, добавляются тер-
мические напряжения от разности тем-
ператур по толщине стенки и по ок-
ружности трубы, от самокомпенсации
температурных удлинений трубопро-
вода, от весовой нагрузки и др.
Расчет трубопроводов на проч-
ность производится в соответствии с
упоминавшимся выше ОСТ 108.031.
02-75. Прочность трубопровода, как
и корпусов теплообменников, оцени-
вается по несущей способности (по
предельной нагрузке). Метод расче-
та по предельным нагрузкам допустим
для пластичных материалов, к кото-
рым относятся и трубопроводные ста-
ли, и позволяет уменьшить металло-
емкость трубопроводов.
В качестве основной нагрузки при
расчетах трубопроводов принято дав-
ление рабочей среды. Дополнительные
внешние нагрузки, действующие по-
стоянно (от самокомпенсации темпе-
ратурных удлинений и от собствен-
ного веса трубопровода), учитываются
дополнительным расчетом, имеющим
характер поверочного расчета. На-
пряжения от температурной неравно-
мерности, возникающие в стенке тру-
бопровода в переходных температур-
ных режимах и отсутствующие в ста-
ционарных режимах эксплуатации,
нормами расчета на прочность не учи-
тываются и регламентируются ре-
жимными мероприятиями.
85