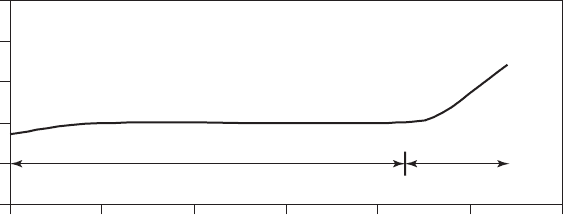
12-16 WATER AND WASTEWATER ENGINEERING
Membrane Element Design. Equations 12-5 and 12-11 are used to design the membrane mod-
ule, rack, and total membrane system. Flux rates range from 0.034 to 0.170 m
3
/h · m
2
( m/h).
In a fashion similar to granular filters, s ome excess capacity is provided to account for racks
being off-line for backwashing and/or maintenance. The flux for MF/UF units treating backwash
water may be as low as one-fourth of that for MF/UF units treating source water (Pressdee et al.,
2006).
Although preliminary
screening estimates of flux and membrane area can be made based on
literature values, for any realistic design, results from pilot testing are required.
Backwashing. The backwash cleaning cycle is automatically controlled. All modules in a rack
are washed simu
ltaneously. Backwashing occurs at some preset interval ranging from 30 to 90
minutes and it las ts 1 to 5 minutes. The off-line time for a rack may be longer than 5 minutes
because of the time inherent in valve sequencing for shut down and start up.
M F systems may be backwa
shed with either air or permeate water. UF systems are back-
washed with permeate water. Because, in general, one rack at a time is backwashed, the design
must ensure that there is sufficient time (plus a factor of safety) for all units to be washed in one
backwash cycle. In general, the backwash supply (air or water) is from a single so
urce, but mul-
tiple sources may be required to clean all racks in the allotted time.
A dding chlorine to the backwash water aids in reducing biofouling as shown in Figure 12-9 .
The test conditions shown were made with 45 s backwash with permeate water containing 3 mg/L
chlorine (Jacangelo et al., 1992). Most sys
tems use air scour during backwash.
Chemical Cleaning. Even with frequent backwashing, membrane performance will deteriorate
over time. The cleaning procedure may take a few hours. The modules may be cleaned in place
(CIP) or may be removed for cleaning. Sufficient excess capac ity or redundancy
must be pro-
vided to maintain production flow rates during the time units are off-line for chemical cleaning.
In addition, the design mu st provide for storage and application of the chemicals and, in some
cases, heating of the cleaning solutions to temperatures of 30C to 40 C.
0
35
70
105
140
175
0 5 10 15 20 25 30
Days of operation
Transmembrane pressure, kPa
Chlorine during backwash
No chlorine during
backwash
FIGURE 12-9
Effect of backwashing with chlorine on membrane fouling.