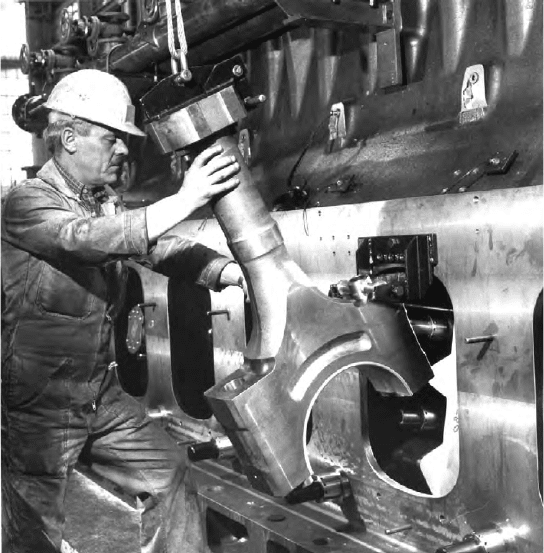
582 Man Diesel
Although most of the basic concept for the L58/64 engine’s revised cylinder
head derived from that of the 48/60B engine, it became apparent during the design
process that adaptation to the structural conditions of the larger bore model dic-
tated the modelling of a new head. By connecting the charge air pipe to the rocker
arm casing—thus simplifying the routing of the air flow—it became possible to
design a flatter and more compact cylinder head. This was also facilitated by the
operational reliability and wear resistance of the valves; renovating the valves and
seats had not been necessary outside regular maintenance intervals.
Both the exhaust pipe and the area around it were redesigned, leading to a
reassessment and tailoring of the insulation and covering, exhaust pipe supports,
exhaust gas blow-off device and charge air bypass to meet the demands set by
resizing. A flow velocity increase called for a redesign of the gas passage between
cylinder head and exhaust pipe, leading to a 50 per cent reduction in the pipe’s
cross-section. This enhanced exhaust admission to the turbocharger in non-
stationary engine operation, resulting in an improved turbocharger response time.
As a large number of new components were integrated into the existing engine
concept, MAN engineers took the opportunity to redesign the supply pipes, com-
bining the passage of media to the engine at optimized connection points.
Figure 22.13 a low piston dismantling height is achieved by the joint in the upper
part of the connecting rod shaft (L58/64, L48/60 and L40/54 engines)