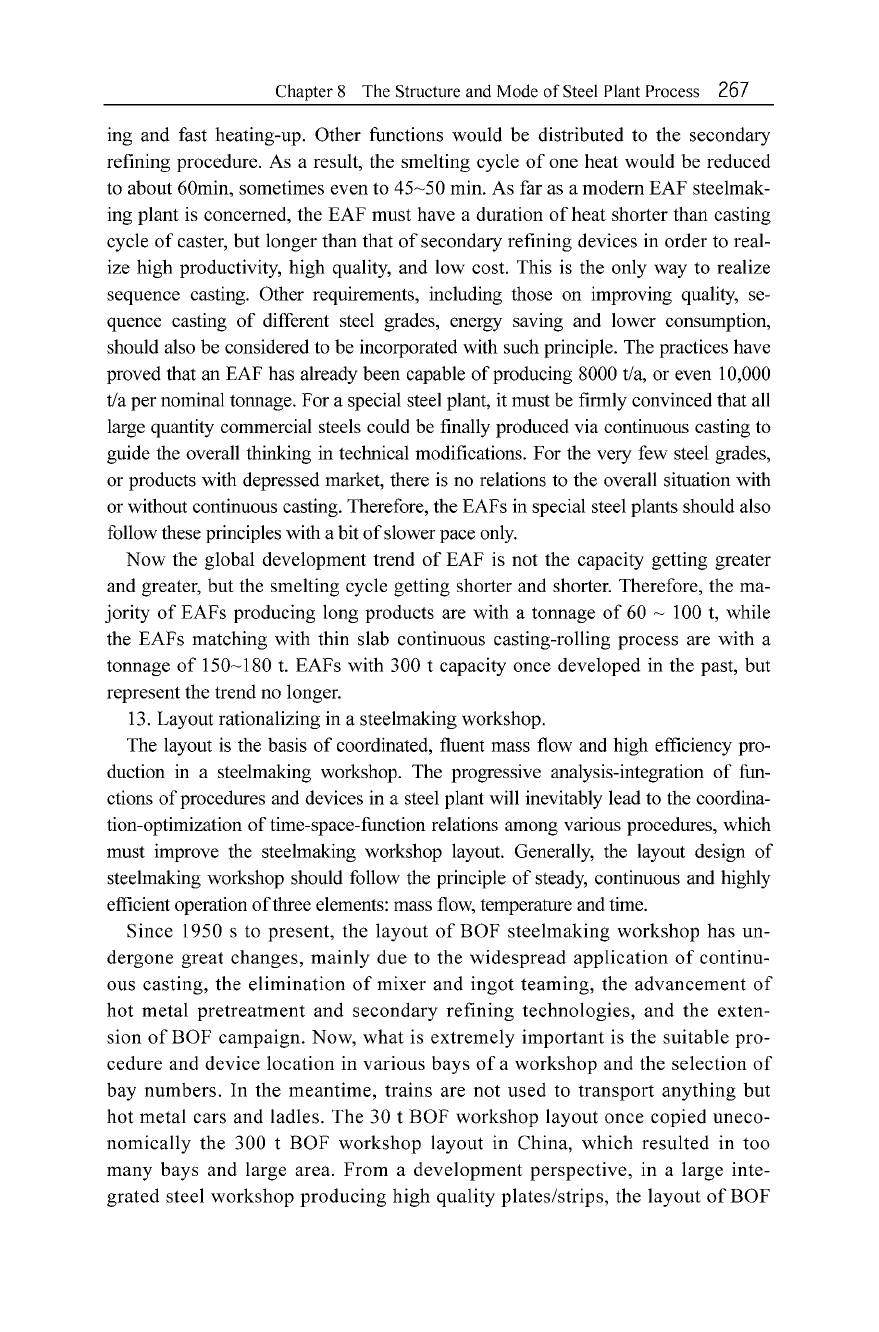
Chapter 8 The Structure and Mode
of
Steel Plant Process 267
ing and fast heating-up. Other functions would be distributed to the secondary
refining procedure. As a result, the smelting cycle
of
one heat would be reduced
to about 6Omin,sometimes even to
45
~50
min. As far as a modern EAF steelmak-
ing plant is concerned, the EAF must have a duration
of
heat shorter than casting
cycle
of
caster, but longer than that
of
secondary refining devices in order to real-
ize high productivity, high quality, and low cost. This is the only way to realize
sequence casting. Other requirements, including those on improving quality, se-
quence casting
of
different steel grades, energy saving and lower consumption,
should also be considered to be incorporated with such principle. The practices have
proved that an EAF has already been capable of producing 8000 t/a, or even 10,000
t/a per nominal tonnage. For a special steel plant, it must be firmly convinced that all
large quantity commercial steels could be finally produced via continuous casting to
guide the overall thinking in technical modifications. For the very few steel grades,
or products with depressed market, there is no relations to the overall situation with
or without continuous casting. Therefore, the EAFs in special steel plants should also
follow these principles with a bit
of
slower pace only.
Now the global development trend
of
EAF is not the capacity getting greater
and greater, but the smelting cycle getting shorter and shorter. Therefore, the ma-
jority
of
EAFs producing long products are with a tonnage
of
60
~
100 t, while
the EAFs matching with thin slab continuous casting-rolling process are with a
tonnage
of
150
~
180 t. EAFs with 300 t capacity once developed in the past, but
represent the trend no longer.
13. Layout rationalizing in a steelmaking workshop.
The layout is the basis
of
coordinated, fluent mass flow and high efficiency pro-
duction in a steelmaking workshop. The progressive analysis-integration
of
fun-
ctions of procedures and devices in a steel plant will inevitably lead to the coordina-
tion-optimization
of
time-space-function relations among various procedures, which
must improve the steelmaking workshop layout. Generally, the layout design
of
steelmaking workshop should follow the principle
of
steady, continuous and highly
efficientoperation ofthree elements:mass flow,temperature and time.
Since 1950 s to present, the layout
of
BOF steelmaking workshop has un-
dergone great changes, mainly due to the widespread application
of
continu-
ous casting, the elimination
of
mixer and ingot teaming, the advancement
of
hot metal pretreatment and secondary refining technologies, and the exten-
sion
of
BOF campaign. Now, what is extremely important is the suitable pro-
cedure and device location in various bays
of
a workshop and the selection
of
bay numbers. In the meantime, trains are not used to transport anything but
hot metal cars and ladles. The 30 t BOF workshop layout once copied uneco-
nomically the 300 t BOF workshop layout in China, which resulted in too
many bays and large area. From a development perspective, in a large inte-
grated steel workshop producing high quality plates/strips, the layout
of
BOF