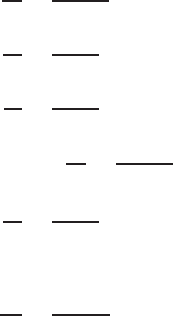
376 15 DIRECT-STRENGTH METHOD
15.4 DIRECT-STRENGTH METHOD
DESIGN GUIDE
In order to provide practical and detailed guidance on
the use of the DSM, Schafer prepared the Design Guide
published by AISI in 2006.
1.383
This Guide presents the
basic technical information on elastic buckling analysis
using the finite-strip method, finite-element method, general
beam theory, and manual solutions. The finite-strip method
for cold-formed steel was pioneered at the University of
Sydney and a long-used program (THIN-WALLED) is
commercially available from them. Through partial research
support of AISI, an open-source and free finite-strip method
program (CUFSM) was developed by Professor Schafer at
Johns Hopkins University. A fully commercial implemen-
tation integrated alongside with complete Specification and
member checking is also available as (CFS).
The Guide lists the following three computer programs
for the use of the DSM:
1. CUFSM (www.ce.jhu.edu/bschafer/cufsm)
15.6
2. CFS (www.rsgsoftware.com)
15.7
3. THIN-WALL (www.civil.usyd.edu.au/case/
thinwall.php)
15.4
These programs can provide a proper handling of element
interaction for general cross sections and can be used
to investigate various possible buckling modes, including
local, distortional, and global (overall) buckling for the
design of cold-formed steel structural members. Based
on the computed elastic buckling stresses as shown in
Figs. 4.42 and 5.15 with the full-section properties, the
DSM can be used.
In addition, the Design Guide includes 12 design
examples covering different cold-formed steel cross
sections under various loading and boundary conditions.
Most of the examples are based on those sections used in
the 2002 edition of the AISI Cold-Formed Steel Design
Manual.
1.340
Comparison between the 2001 edition of the
main specification and DSM is summarized in Table 6 of
the Guide. In general, when distortional buckling controls
the design, the DSM provides a relatively lower strength
than the main specification. Since new provisions for
distortional buckling strengths of beams and columns were
added in the 2007 edition of the North American Specifica-
tion, similar capacities can be achieved by using the main
Specification and DSM, if Sections C3.1.4 (b) and C4.2
(b) of the main Specification are used for the design of
flexural members and compression members, respectively.
For numerical comparisons, see Examples II-4 and III-3
of the 2008 edition of the AISI Cold-Formed Steel Design
Manual.
1.349
The column chart for the C-section with lips (9CS 2.5
×059) and the beam chart for the same C-section in the
Design Guide are shown here in Figs. 15.5 and 15.6,
respectively, to illustrate the behavior of typical members.
In Fig. 15.5 on the column chart, it is noted that (1)
local buckling dominates the actual column strength, (2)
the reduction due to local buckling is large even for short
columns, and (3) distortional buckling never controls in this
section.
1.383
For the beam chart shown in Fig. 15.6, it is noted that
(1) distortional buckling (M
nd
) controls the strength for
a small group of lengths approximately between 2 and
5 ft and (2) beyond approximately 10 ft in length, local
buckling (M
nl
) does not reduce the capacity below the
global buckling strength (M
ne
). (In the parlance of the North
American Specification, this section is fully effective for
unbraced length beyond 10 ft.)
1.383
15.5 DESIGN EXAMPLES
Example 15.1 For the C-section used in Examples 4.2
and 4.13 as a beam member, use the DSM (Section 1.2.2 of
Appendix 1 of the specification) to determine the allowable
moment about the x axis for the ASD method. Assume that
lateral bracing is adequately provided and F
y
= 50 ksi.
SOLUTION
1. Geometric and Material Limitations . As the first step,
the limitations for prequalified beams should be checked by
using Table 1.1.1-2 of Appendix 1 as follows:
h
0
t
=
10.000
0.075
= 133.33 < 321
b
0
t
=
3.500
0.075
= 46.67 < 75
D
t
=
0.720
0.075
= 9.60 < 34
1.5 <
h
0
b
0
=
10.000
3.500
= 2.86
< 17.0
D
b
0
=
0.720
3.500
= 0.21 < 0.70
44
◦
<(θ = 90
◦
) = 90
◦
E
F
y
=
29,500
50
= 590 > 421
Since the given C-section meets the geometric and material
limitations provided in Table 1.1.1-2, use
b
= 1.67 for
ASD as defined in Section 1.2.2 of Appendix 1.
2. Lateral–Torsional Buckling. Since the lateral bracing
is adequately provided, the beam is not subject to lateral–
torsional buckling. According to Section 1.2.2.1 of