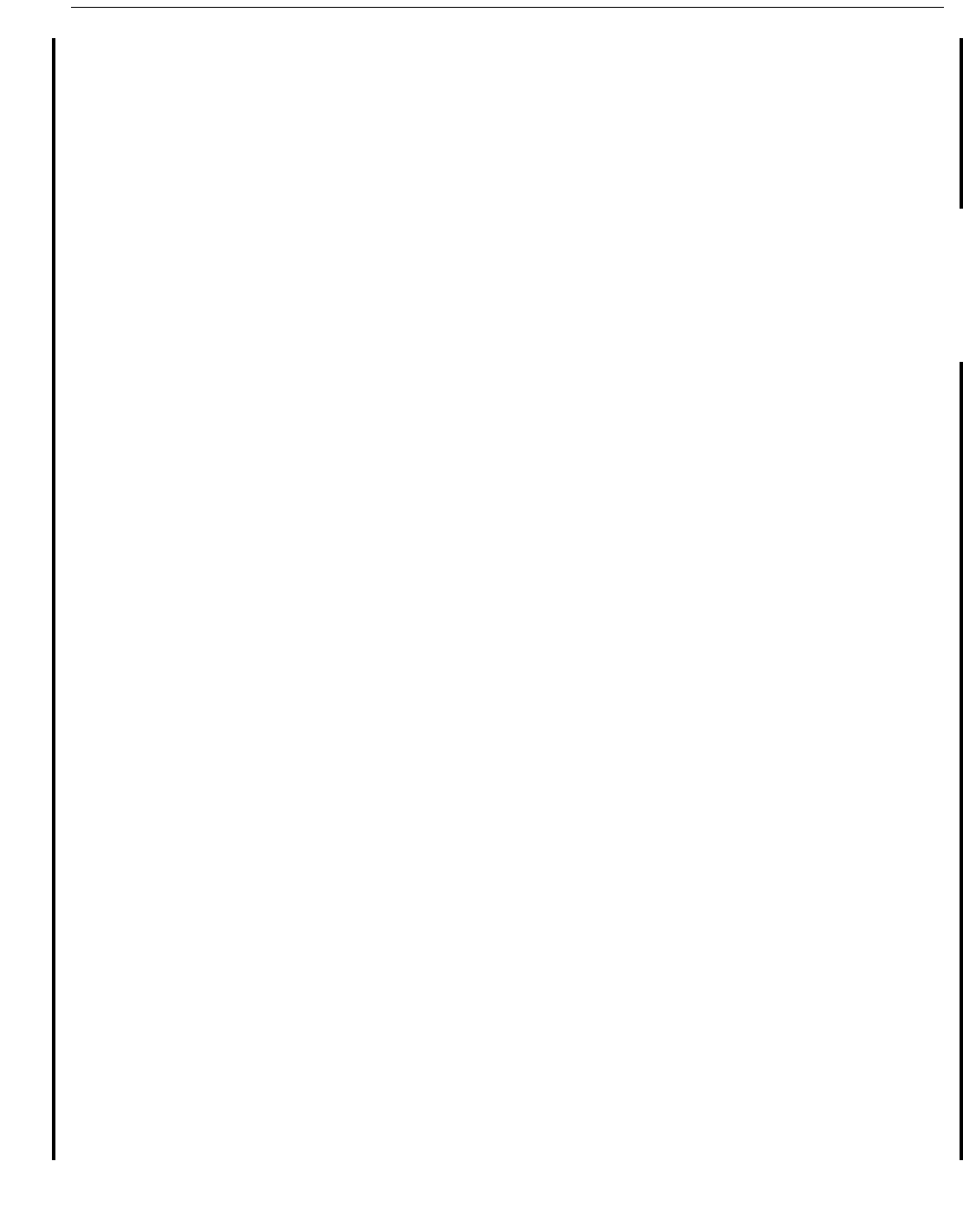
176 API RECOMMENDED PRACTICE 2A-WSD
A recently completed joint industry project (Ref. 10) inves-
tigated the static strength of high strength steel X joints. The
joint industry project involved the testing of four compression
joints (two at a nominal yield strength of 355 MPa and one
each at 500 MPa and 700 MPa) and three tension joints (one
each at nominal yield strength of 355 MPa, 500 MPa and
700 MPa). The findings presented in Ref. 10 indicate that all
the joints performed satisfactorily in the tests in terms of
strength and ductility, confirming the practicality of using
higher strength steels. These data indicate that a yield-to-ten-
sile strength ratio of 0.8 can be used to estimate the ultimate
compression and tension capabilities of the joints. However,
for the tension loaded joints in which cracking prior to reach-
ing the ultimate capacities was observed, no detailed assess-
ments were presented.
Beyond 800 MPa, indicative capacity estimates may be
obtained through use of a yield stress of 800 MPa or 0.8 times
the tensile strength, whichever is the lesser. Given the lack of
data and information in this area, this approach should be
considered to be only indicative.
C4.2.2 Design Loads and Joint Flexibility
Given present-day computer power and software packages,
it is generally recommended that working point offsets be
defined in the analysis model to capture secondary moments.
Optionally, rigid offsets from the working points on the chord
centerline to the chord surface can also be defined. Such off-
sets can be used to reduce the bending moments from nodal
values to those at the chord surface (the moment capacity
equations were established for chord surface moments).
Historically, designers of offshore jacket structures have
usually made the assumption that the joints are rigid and that
the frame can be modeled with members extending to work-
ing points at chord centerlines. However, it has long been rec-
ognized that the linear elastic flexibility of tubular joints may
be significant at locations such as skirt pile bracing and in
computing fatigue life estimates for secondary connections.
For conductor framing connections, fatigue life estimates can
be substantially larger when linear elastic flexibilities are
included in the analyses, because the member lengths are
short and member flexibility tends to be less than joint flexi-
bility. From a system ultimate strength standpoint, full, non-
linear, load-deformation curves for joints may be required in
pushover analyses, especially where joint failures are
expected to participate in the sequence of events leading to
system collapse. Such analyses are common in the mainte-
nance of infrastructure and life extension studies of existing
facilities.
In 1993, Buitrago et al. (Ref. 11) published a robust set of
equations for linear elastic flexibility/stiffness of simple tubu-
lar joints. Although a number of other sets of formulations are
available in the literature, Buitrago’s formulations are consid-
ered to be more wide-ranging, have better physical meaning,
compare better with experimental data and are simpler to use
manually and computationally.
In Ref. 6, the technology pertaining to linear elastic flexi-
bility was extended through analyses of the updated database,
to establish a range of closed-form expressions, which permit
the designer to create non-linear load-deformation (P
δ
or M
θ
)
curves in both the loading and unloading regimes for simple
joints across the practical range of load cases and geometries.
The full non-linear expressions will see application primarily
in pushover analyses, especially where joint failures are pos-
tulated to influence to the peak failure load.
Ref. 12 reports on a pilot study to assess the effect of
hydrostatic pressure on tubular joint capacity. DT joints are
studied, and the results indicate that capacity may be reduced
by up to 30%, depending on geometry, brace load case and
hydrostatic pressure magnitudes. Apart from Ref. 12, no
other studies in this area have been identified. Hydrostatic
pressure effects can be significant, especially for deepwater
structures, and the designer is referred to Ref. 12 when con-
sidering these effects. In many instances, members are pur-
posefully flooded to avoid hydrostatic pressure effects.
C4.2.3 Minimum Capacity
API has a broad minimum capacity requirement that
equate to 50 percent of the capacity of the incoming brace.
For earthquake loading, the requirement is essentially 100
percent of the brace capacity. Aside from earthquake regions,
the 50 percent capacity sometimes dominated secondary joint
design (Ref. 13) and took precedence on primary joints. In
general, joint failure prior to member reaching allowable
stress is undesirable, due to uncertainty in failure behavior
and the effect on surrounding structure.
However, joint yielding prior to member buckling may be
a more benign failure mode. Also, where secondary branch
members have been strengthened for localized loadings, cor-
rosion allowance, or section availability, 50% rule need not
apply.
To address the relative reliability of joints and members,
and to ensure that the members fail first, it has been suggested
that the utilization factor of critical joints be limited to 85%
that of its branch members. The designer may wish to deter-
mine critical joints for this minimum capacity imposition, e.g.
joints that influence the reserve strength of the structure in a
design load event (wave load, earthquake, etc.) or joints that
influence the response of the structure when subjected to
accidental loads.
C4.2.4 Joint Classification
API has long recognized that joint classification should be
based on axial load pattern as well as joint configuration. In
principle, classification is an issue for both simple and com-
plex joint configurations and is relevant to both fatigue and
strength assessments. However, the classifications are not
always the same as they can vary with wave direction and
period. Classifications, and subsequent code checks, for
strength should not be based on only a consideration of the
wave loading at maximum shear or overturning moment. In
Copyright American Petroleum Institute
Provided by IHS under license with API
Licensee=Indonesia location/5940240008
Not for Resale, 10/22/2008 00:07:12 MDT
No reproduction or networking permitted without license from IHS