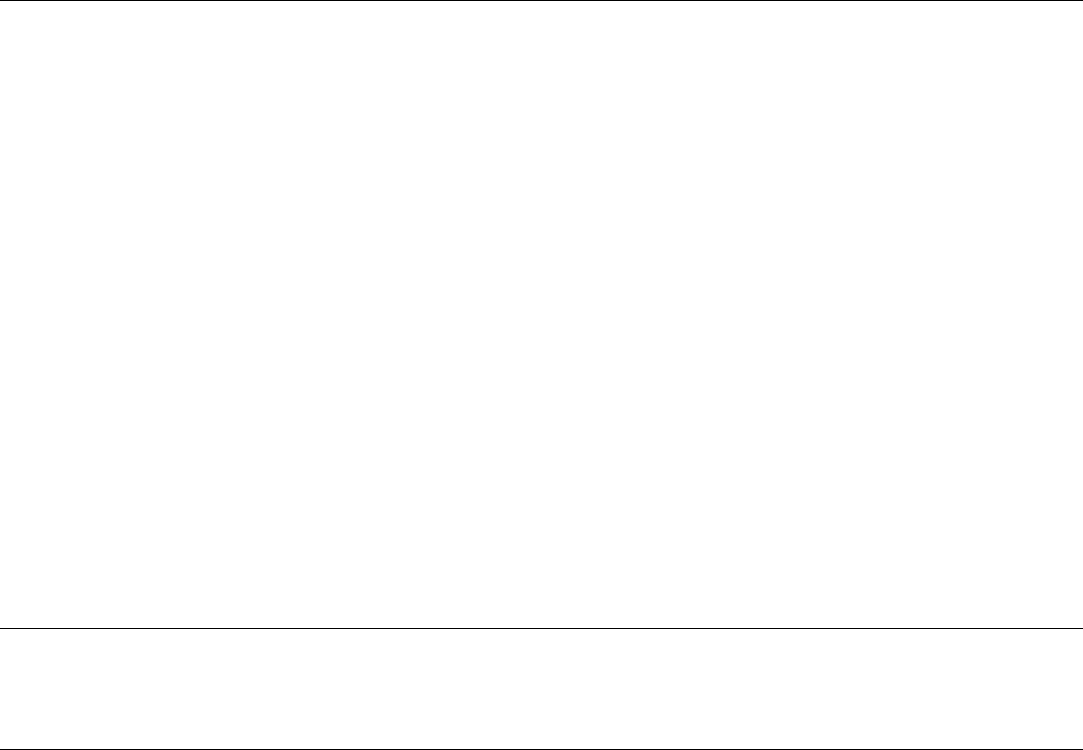
References cited in this section
58.
J.C. Malas, "A Thermodynamic and Continuum Approach to the Design and Control of Precision Forging
Processes," Wright State University, 1985
60.
J.C. Malas, J.T. Morgan, H.L. Gegel, J.S. Gunasekera, S.M. Doraivelu, and S.I.
Oh, An Investigation on the
Mathematical-Modeling Technique Used for Analyzing Industrial Metalworking Processes, in
of the Eleventh NAMRC Conference (Madison, WI), May 1983
61.
S.I. Oh, S.L. Semiatin, S.M. Hwang, J.J. Park, W.T. Wu, and T. Al
tan, "Processing Science Research to
Develop Scientific Methods for Controlling Metal Flow, Microstructures, and Properties in 3-
Forming Processes," Final Report AFWAL-TR87-4077, Wright-Patterson Air Force Base, Sept 1987
62.
H. Gegel, Future Directions of CAD/CAM/CAE in Manufacturing Overview, in
AUTOFACT '87 Conference (Detroit, MI), 1987
63.
J.A. Ficke, S.I. Oh, and J.C. Malas, FEM Simulation of Closed Die Forging of Isothermal Titanium Disk
Forging Using ALPID, in Proceedings of the 1984 Manufacturing Engineering Transactions, NAMRC XIII,
Society of Manufacturing Engineers, May 1986
64.
D.F. Wilhelm, Understanding Presses and Press Operations, Society of Manufacturing Engineers, 1981
65.
T. Altan, F.W. Boulger, J.R. Herman,
and H.J. Henning, Forging Equipment, Materials, and Processes, in
Metals and Ceramics Information Center Handbook, MCIC-HB-
03, Metals and Ceramics Information
Center, 1973
Modeling Techniques Used in Forging Process Design
H. L. Gegel and J.C. Malas, Air Force Wright Aeronautical Laboratories/Materials Laboratory; S.M. Doraivelu and V.A. Shende,
Universal Energy Systems, Knowledge Integration Center
Physical Modeling
Whenever an analytical method for designing a physical system is devised, it is essential that its validity be tested by
physical modeling. Such testing not only provides the feedback that aids in the development/refinement of the analytical
model but also demonstrates the accuracy of the analytical predictions. Therefore, physical modeling provides greater
confidence in the application of these analytical techniques toward the solution of actual problems.
Approaches
Two approaches are generally used in designing physical models. The first consists of simulating, as closely as possible, a
production unit process on a laboratory scale and monitoring or controlling the important process parameters. The product
resulting from such a test can then be analyzed to determine how closely its characteristics match those predicted by the
analytical model. The second approach to physical modeling is to devise a laboratory test that is faster, easier, and less
expensive than a subscale production process and yet provides an equally thorough test of the accuracy and robustness of
the analytical model. Model materials and visioplasticity techniques are utilized in this approach for analyzing flow
behavior.
Model Materials
Model materials such as Plasticine, wax, and polymers are used for physical simulation because:
• The load required for deformation is relatively small
• Observation of the deformation pattern is easy
• Test specimens are easy and inexpensive to make
• Inexpensive die materials such as wood and plastic can be used