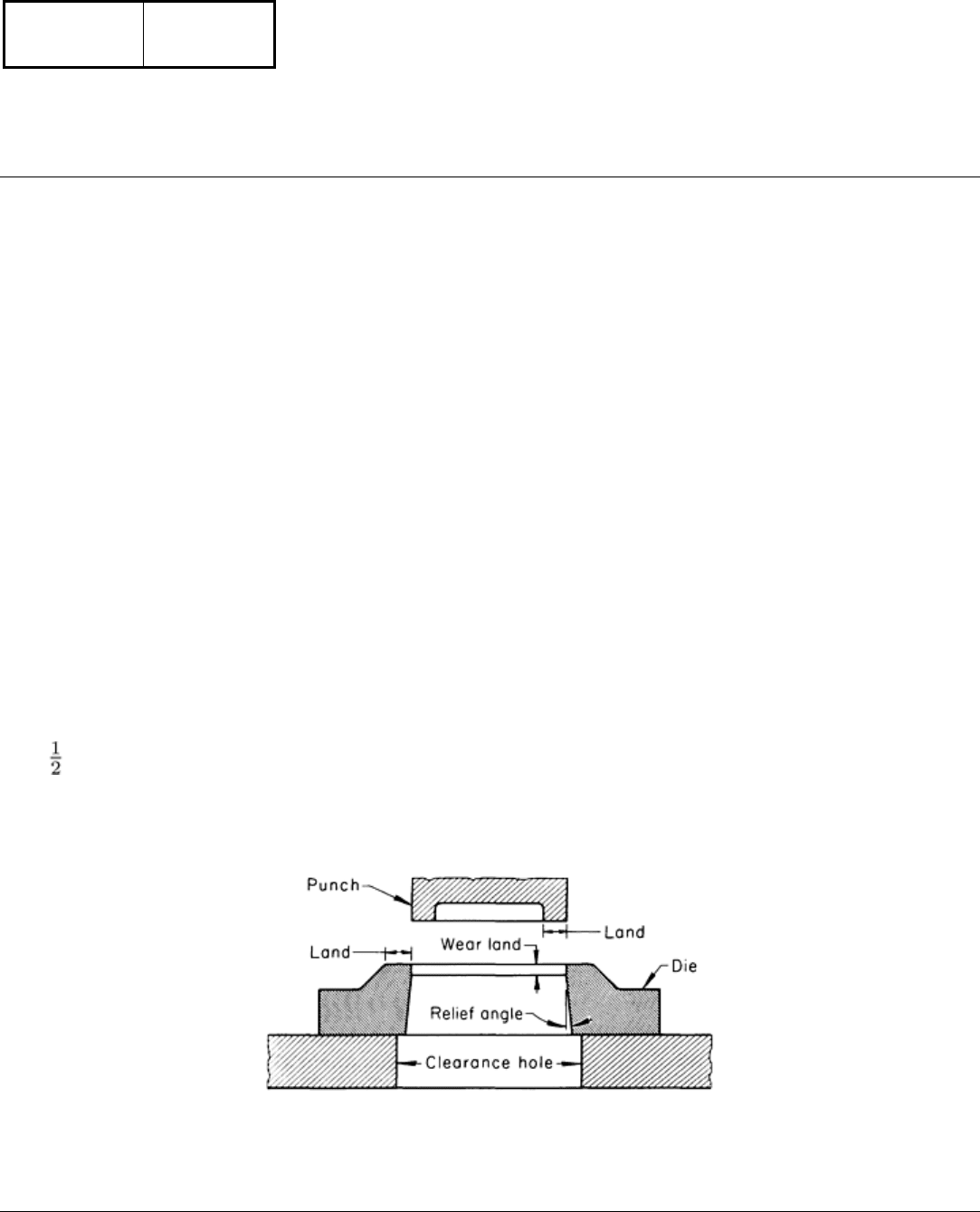
Zinc alloys 50
(a)
Ann, annealed; CR, cold rolled
Blanking of Low-Carbon Steel
Die Clearance
The terms clearance, die clearance, and punch-to-die clearance are used synonymously to refer to the space between
punch and die. Clearance is important for the reliable operation of the blanking equipment, the quality and type of cut
edges, and the life of the punch and die. In general, the effects of clearance on these factors in blanking are the same as in
piercing and are discussed in the article "Piercing of Low-Carbon Steel" in this Volume. The same article also describes
the edge characteristics of slugs produced in piercing holes (see Fig. 2 of that article). The data in that illustration can
serve as a guide for selecting clearances for blanking. All clearance values given in this article are per side, except where
indicated.
Optimal blanking clearance may sometimes be less than optimal piercing clearance. This is partly because the blanked
edge is generally close to the stock edge, and material expansion is therefore less restricted. A piercing tool must move a
great deal of material away from its cutting edge, and for longest life, the clearance should be selected to eliminate as
much compressive loading on the work metal as possible.
A part blanked using clearance much greater than normal may exhibit double shear, which is ordinarily evident only with
extremely small clearance (see edge types 4 and 5 in Fig. 2 in the article "Piercing of Low-Carbon Steel" in this Volume).
In addition, a part blanked using large clearances will be smaller than the die opening (except for a deeply dished blank),
and it is difficult to correct the tooling to compensate for this. In some applications, retaining the blank becomes almost as
great a problem as expelling the slugs into a die cavity after piercing, because of the increased clearance.
Relief in a blanking die (Fig. 9) is the taper provided so that the severed blank can fall free. The relief angle may range
from to 2° from the vertical wall of the die opening. Relief in a die is sometimes called draft or angular clearance. In
some dies, the relief may start at the top of the die surface and have a taper of only 0.002 in./in. (0.002 mm/mm) per side.
In other dies, there is a straight, vertical wear land between the top of the die and the relief.
Fig. 9 Relief in a blanking die
Blanking of Low-Carbon Steel
Calculation of Force Requirements
Calculation of the forces and the work involved in blanking gives average figures that are applicable only when the
correct shear strength for the material is used and when the die is sharp and the punch is in good condition, has correct