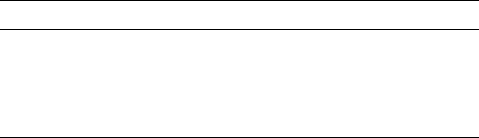
Cutting Tool Wear, Tool Life and Cutting Tool Physical Resource 229
Table 4.3. Coefficients and powers in Eq. (4.7). Tool material –
P20, rake angle γ = 8
◦
, flank angles of the major and minor
cutting edges, α = α
1
= 15
◦
, tool cutting edge angle κ
r
= 45
◦
,
tool cutting edge angle of the minor cutting edge κ
r1
= 15
◦
.
Work material C
θ
n
ν
n
f
n
d
AISI 1010 228 0.25 0.07 0.03
AISI 1020 269 0.27 0.15 0.10
AISI 1045 352 0.22 0.08 0.05
AISI 1080 224 0.33 0.11 0.07
AISI 07 326 0.28 0.12 0.07
and Table 4.3, namely that the same cutting temperature can be achieved using different
combinations of the terms of Eq. (4.7).
Analyzing a great body of experimental data, Makarow formulated the law [14] which
was presented as the First Metal Cutting Law (the Makarow’s law) by Astakhov [16,17]:
For given combination of the tool and work materials, there is the cutting temperature,
referred to as the optimal cutting temperature θ
opt
, at which the combination of minimum
tool wear rate, minimum stabilized cutting force, and highest quality of the machined
surface is achieved. This temperature is invariant to the way it has been achieved (whether
the workpiece was cooled, pre-heated etc.).
The first metal cutting law, established initially for longitudinal turning of various work
materials (example is shown in Fig. 4.5(a), was then experimentally proven for various
machining operations. Figure 4.5(b) shows its applicability in twist drilling, Fig. 4.5(c) –
in thread cutting, Fig. 4.5(d) – in gear hobbing. Considering Fig. 4.5(a), one can see
that when the cutting feed increases, the surface wear rate reduces. However, minimum
tool wear rates, when various cutting feed are used, occur at the same optimal cutting
temperature θ
opt
, although the amount of the surface wear rate varies more than 2 times.
Even more pronounced effect can be observed in Fig. 4.5(b), where the cutting feed has
a much stronger influence on tool life, represented by the total length of the tool path to
achieve VB
B
= 0.3 mm. As shown, there is a specific combination of the cutting speed
and feed at which tool life is at a maximum. Changing the cutting speed and/or feed on
either side reduces tool life while the minimum tool wear rate under a given combination
of these parameters corresponds to the optimal cutting temperature. Figure 4.5(c) shows
that tool life in thread cutting, represented by the total length of the tool path (L (m)) to
achieve VB
B
= 0.5 mm, has its maximum at the same optimal cutting temperature, θ
opt
under different combinations of cutting speed and feeds. Figure 4.5(d) shows that the
same conclusion can be drawn from the data for gear hobbing.
Figure 4.6 shows that the machining at optimal cutting temperature results not only
at the minimum tool wear rate but also leads to obtaining the minimum cutting force
and smallest roughness of the machined surface. As it follows from this picture, under